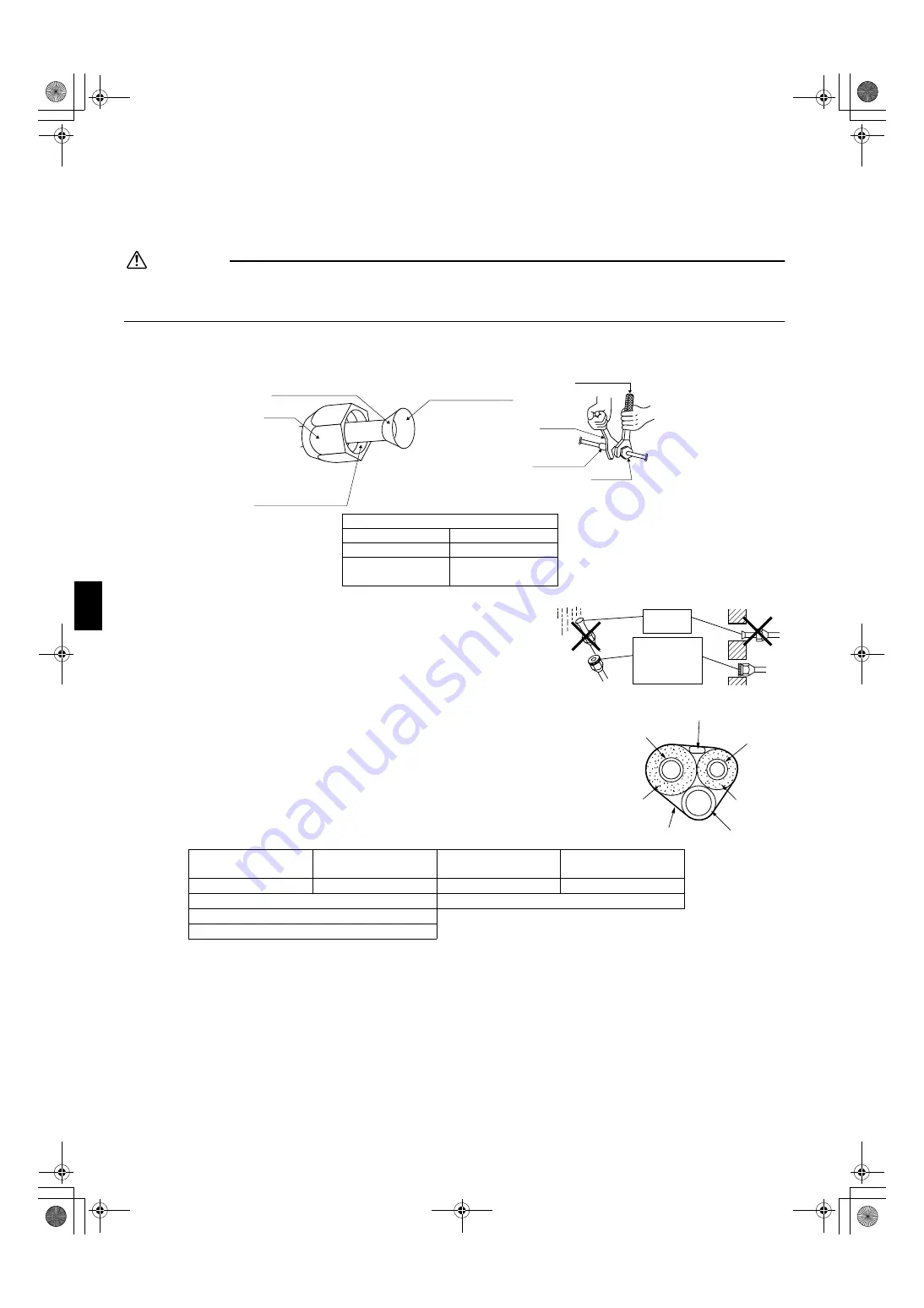
11
■
English
Refrigerant Piping Work
2.
Refrigerant piping.
CAUTION
1) Use the flare nut fixed to the main unit. (To prevent cracking of the flare nut by aged deterioration.)
2) To prevent gas leakage, apply refrigeration oil only to the inner surface of the flare. (Use refrigeration oil for R410A.)
3) Use torque wrenches when tightening the flare nuts to prevent damage to the flare nuts and gas leakage.
Align the centres of both flares and tighten the flare nuts 3 or 4 turns by hand. Then tighten them fully with the torque wrenches.
2-1. Caution on piping handling.
1) Protect the open end of the pipe against dust and moisture.
2) All pipe bends should be as gentle as possible. Use a pipe bender
for bending.
2-2. Selection of copper and heat insulation materials.
• When using commercial copper pipes and fittings, observe the following:
1) Insulation material: Polyethylene foam
Heat transfer rate: 0.041 to 0.052W/mK (0.035 to 0.045 kcal/(mh•°C))
Refrigerant gas pipe’s surface temperature reaches 110°C max.
Choose heat insulation materials that will withstand this temperature.
2) Be sure to insulate both the gas and liquid piping and to provide insulation dimen-
sions as below.
3) Use separate thermal insulation pipes for gas and liquid refrigerant pipes.
Gas side
Liquid side
Gas pipe thermal
insulation
Liquid pipe thermal
insulation
O.D. 9.5mm
O.D. 6.4mm
I.D. 12-15mm
I.D. 8-10mm
Minimum bend radius
Thickness 10mm Min.
30mm or more
Thickness 0.8mm (C1220T-O)
Do not apply refrigeration
oil to the outer surface.
Flare nut
Apply refrigeration oil to
the inner surface of the
flare.
Do not apply refrigeration
oil to the flare nut avoid
tightening with over torque.
[Apply oil]
Torque wrench
Piping union
Flare nut
Spanner
[Tighten]
Flare nut tightening torque
Gas side
Liquid side
3/8 inch
1/4 inch
32.7-39.9N
l
m
(330-407kgf
l
cm)
14.2-17.2N
l
m
(144-175kgf
l
cm)
Gas pipe
Liquid pipe
Gas pipe
insulation
Liquid pipe
insulation
Finishing tape
Drain hose
Inter-unit wiring
01_EN_3P207973-1D.fm Page 11 Friday, September 4, 2009 10:44 AM