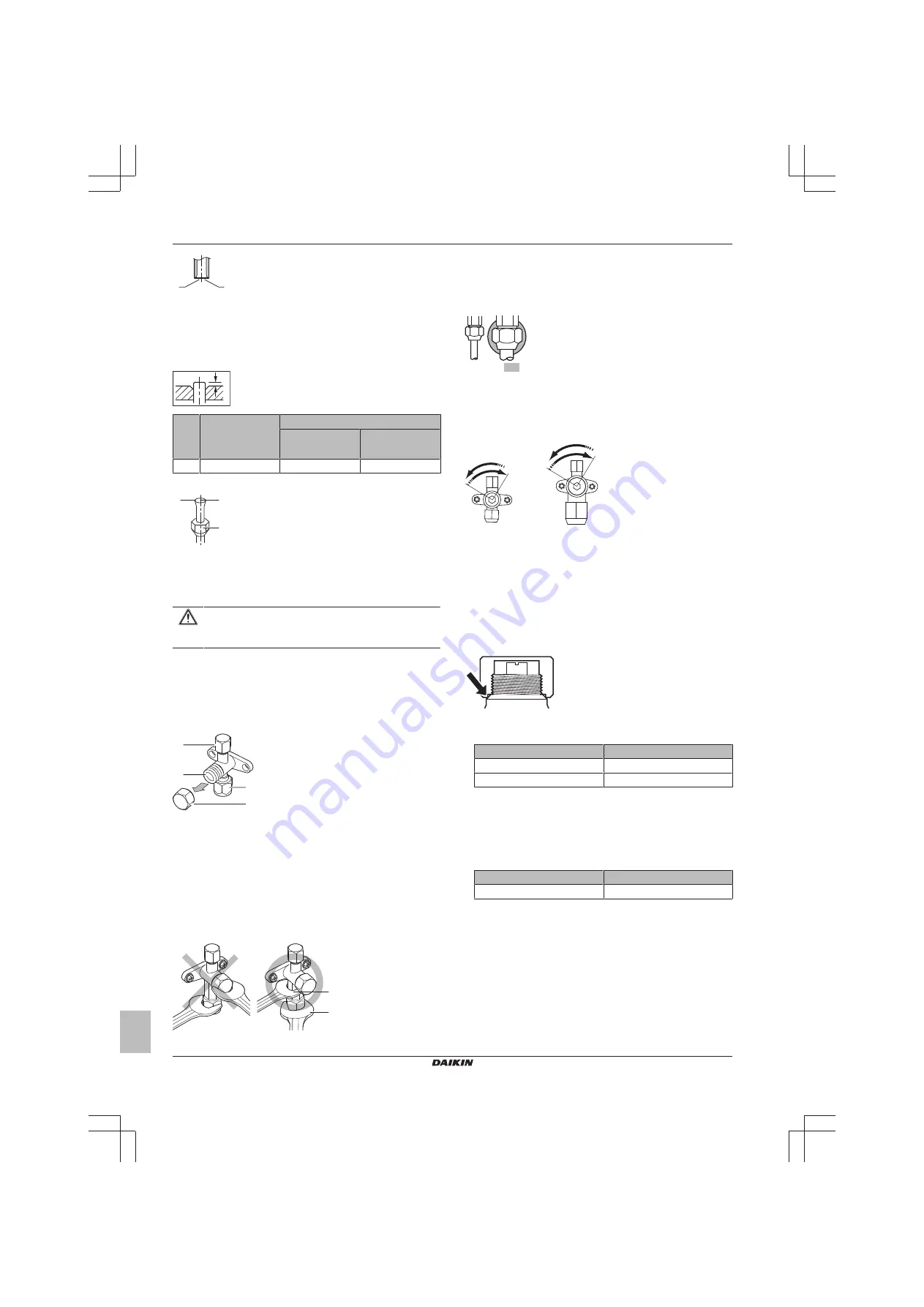
6 Installation
Installer reference guide
14
ARXM25~3RXM20~35N2V1B9
R32 split series
4P518023-5C – 2018.09
a
b
a
Cut exactly at right angles.
b
Remove burrs.
3
Remove the flare nut from the stop valve and put the flare nut
on the pipe.
4
Flare the pipe. Set exactly at the position as shown in the
following figure.
A
Flare tool for R32
(clutch type)
Conventional flare tool
Clutch type
(Ridgid-type)
Wing nut type
(Imperial-type)
A
0~0.5 mm
1.0~1.5 mm
1.5~2.0 mm
5
Check that the flaring is properly made.
a
b
c
a
Flare’s inner surface MUST be flawless.
b
The pipe end MUST be evenly flared in a perfect circle.
c
Make sure the flare nut is fitted.
6.4.6
Using the stop valve and service port
CAUTION
Do NOT open the valves before flaring is complete. This
would cause refrigerant gas leakage.
To handle the stop valve
Take the following guidelines into account:
▪ The stop valves are factory closed.
▪ The following figure shows the stop valve parts required when
handling the valve.
c
d
a
b
a
Service port and service port cap
b
Valve stem
c
Field piping connection
d
Stem cap
▪ Keep both stop valves open during operation.
▪ Do NOT apply excessive force to the valve stem. Doing so may
break the valve body.
▪ ALWAYS make sure to secure the stop valve with a spanner, then
loosen or tighten the flare nut with a torque wrench. Do NOT place
the spanner on the stem cap, as this could cause a refrigerant
leak.
a
b
a
Spanner
b
Torque wrench
▪ When it is expected that the operating pressure will be low (e.g.
when cooling will be performed while the outside air temperature
is low), sufficiently seal the flare nut in the stop valve on the gas
line with silicon sealant to prevent freezing.
Silicon sealant; make sure there is no gap.
To open/close the stop valve
1
Remove the stop valve cover.
2
Insert a hexagon wrench (liquid side: 4 mm, gas side: 4 mm)
into the valve stem and turn the valve stem:
Counterclockwise to open.
Clockwise to close.
3
When the stop valve CANNOT be turned any further, stop
turning.
4
Install the stop valve cover.
Result:
The valve is now open/closed.
To handle the stem cap
▪ The stem cap is sealed where indicated with the arrow. Do NOT
damage it.
▪ After handling the stop valve, tighten the stem cap, and check for
refrigerant leaks.
Item
Tightening torque (N∙m)
Stem cap, liquid side
14.2~17.2
Stem cap, gas side
17.1~20.9
To handle the service cap
▪ ALWAYS use a charge hose equipped with a valve depressor pin,
since the service port is a Schrader type valve.
▪ After handling the service port, tighten the service port cap, and
check for refrigerant leaks.
Item
Tightening torque (N∙m)
Service port cap
10.8~14.7
6.4.7
To connect the refrigerant piping to the
outdoor unit
▪
Piping length.
Keep field piping as short as possible.
▪
Piping protection.
Protect the field piping against physical
damage.
1
Connect the liquid refrigerant connection from the indoor unit to
the liquid stop valve of the outdoor unit.