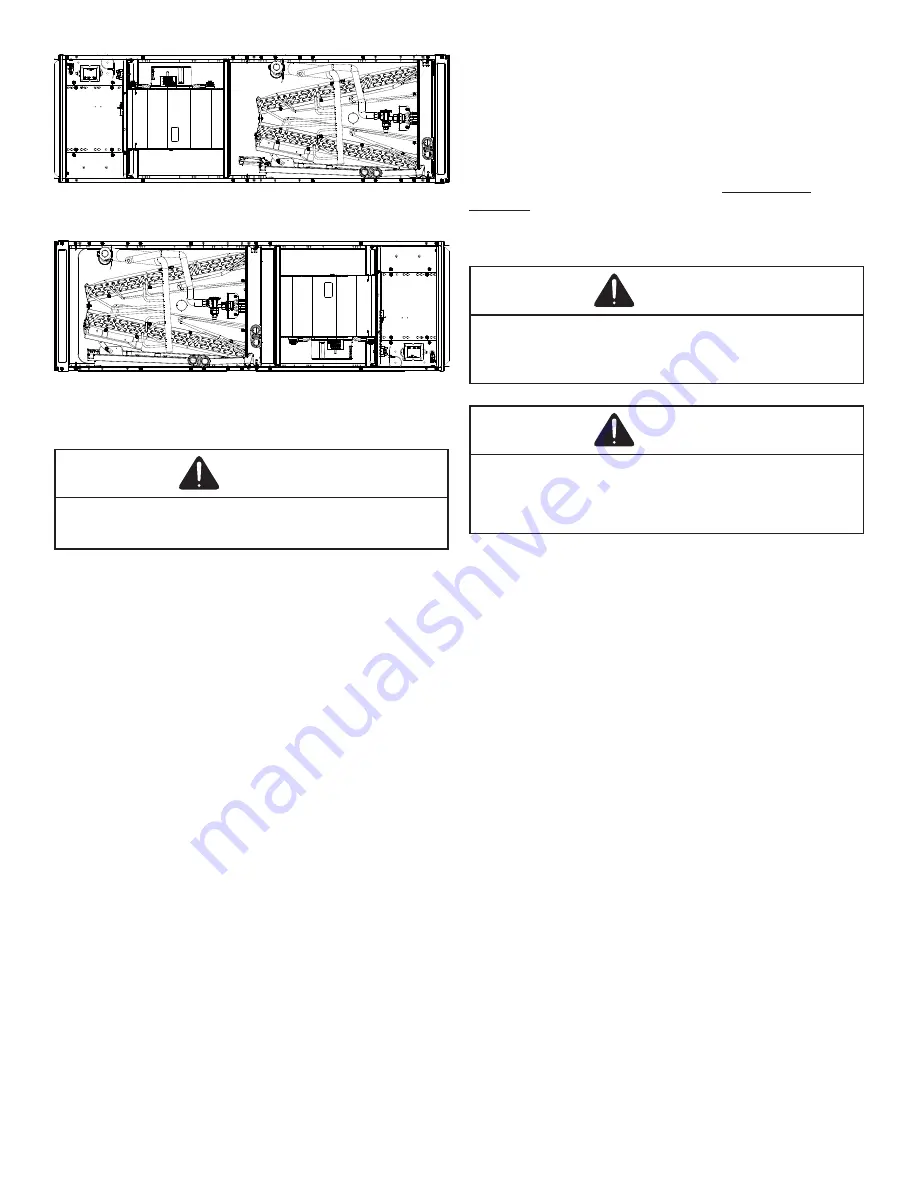
7
HORIZONTAL LEFT
Figure 5
HORIZONTAL RIGHT
Figure 6
7 Refrigerant Lines
WARNING
This product is factory-shipped with R410A and dry nitrogen
mixture gas under pressure. Use appropriate service tools
and follow these instructions to prevent injury.
NOTE: Refrigerant tubing must be routed to allow
adequate access for servicing and maintenance of the
unit.
Do not install the air handler in a location that violates
the instructions provided with the condenser. If the unit
is located in an unconditioned area with high ambient
temperature and/or high humidity, the air handler may be
subject to nuisance sweating of the air handler cabinet. On
these installations, a wrap of 2” fiberglass insulation with a
vapor barrier is recommended.
7.1 Tubing Size
For the correct tubing size, follow the specification for the
condenser/heat pump.
7.2 Tubing Preparation
All cut ends are to be round, burr free, and clean. Failure
to follow this practice increases the chances for refrigerant
leaks. The suction line is spun closed and requires tubing
cutters to remove the closed end.
NOTE: To prevent possible damage to the tubing joints,
do not handle coil assembly with manifold or flowrator
tubes. Always use clean gloves when handling coil
assemblies.
NOTE: The use of a heat shield is strongly
recommended when brazing to avoid burning the
serial plate or the finish of the unit.
Heat trap or
wet rags must be used to protect heat sensitive
components such as service valves and TXV valves
sensing bulb.
WARNING
A quenching cloth is strongly recommended to prevent
scorching or marring of the equipment finish when brazing
close to the painted surfaces. Use brazing alloy of 5%
minimum silver content.
CAUTION
Applying too much heat to any tube can melt the tube.
Torch heat required to braze tubes of various sizes must be
proportional to the size of the tube. Service personnel must
use the appropriate heat level for the size of the tube being
brazed.
7.3 Tubing Connections
An adjustable TXV with bulb is installed on the vapor tube
from the factory.
1. Remove refrigerant tubing panel or coil (lower) access
panel.
2.
Remove access valve fitting cap and depress the
valve stem in access fitting to release pressure. No
pressure indicates possible leak.
3. Replace the panel.
4. Remove the spin closure on both the liquid and
suction tubes using a tubing cutter.
5. Insert liquid line set into liquid tube expansion and
slide grommet about 18” away from braze joint.
6. Insert suction line set into suction tube expansion and
slide insulation and grommet about 18” away from
braze joint.
7. Braze joints. Quench all brazed joints with water or a
wet rag upon completion of brazing.