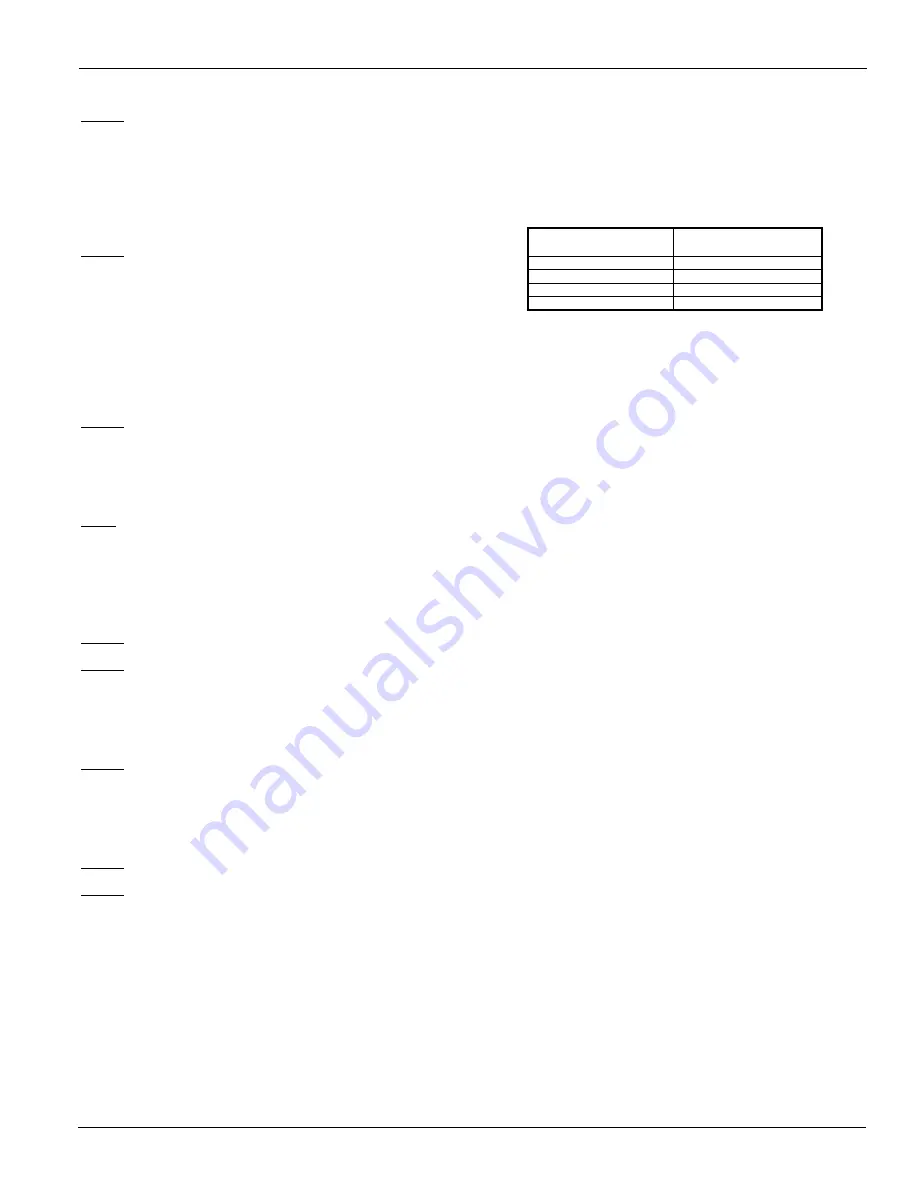
IOM 1206-1
63
Component Operation
Alert/Lockout Codes (Flashing Red LED)
Code 1 – Motor High Temperature: The module will flash the
red
Alert
LED one time indicating the motor is onerheating .
A code 1
Alert
will open the M2-M1 contacts. The
Alert
will
reset after 30 minutes. Five consecutive Code 1
Alerts
will
lockout the compressor. Once the module has locked out the
compressor, a power cycle or Modbus reset command will be
required for the lockout to be cleared.
Code 2 – Open/Shorted Motor Thermistor: The module will
flash the red
Alert
LED two times indicating the motor PTC
thermistor circuit has an open/shorted thermistor chain (see
Table 2
). A Code 2
Alert
will open the M2-M1 contacts. The
Alert
will reset after 30 minutes and the M2-M1 contacts will
close if the resistance of the motor PTC circuit is back in the
normal range. The module will lockout the compressor and a
power cycle or Modbus reset command will be required to
clear the lockout.
Code 3 – Short Cycling: The module will flash the red
Alert
LED three times indicating the compressor is locked out due to
short cycling. Once locked out the compressor, a power cycle
or Modbus reset command will be required to clear the
lockout.
Code 4 – Scroll High Temperature: The module will flash the
red
Alert
LED four times indicating the over-temperature
condition. A Code 4
Alert
will open the M2-M1 contacts.The
Alert
will reset after 30 minutes. Once the module has locked
out the compressor, a power cycle or Modbus reset command
will be required to clear the lockout.
Code 5 – Reserved for Future Use
Code 6 – Missing Phase: The module will flash the red
Alert
LED six times indicating a missing phase. The
Alert
will reset
after 5 minutes and the module will lockout the compressor
after 10 consecutive Code 6
Alerts
. Once locked out, a power
cycle or Modbus reset is required.
Code 7 – Reverse Phase: The module will flash the red
Alert
LED seven times indicating a reverse phase in two of the three
compressor leads. The modules will lockout the compressor
after one Code 7
Alert
. A power cycle or Modbus reset
command will be required to clear the lockout.
Code 8 – Reserved For Future Use
Code 9 – Module Low Voltage: The module will flash the red
Alert
LED nine times indicating low module voltage for more
than 5 seconds. The
Alert
will reset after 5 minutes and the
M2-M1 contacts will close if the T2-T1 voltage is above the
reset value.
Note:
If a compressor with CoreSense Communications fails in
the field, the CoreSense module should remain with the
failed compressor so the manufacturer’s technicians can
download the CoreSense data to assist with determining
the root cause of compressor failure.
Filter-Driers
For units with optional replaceable core filter driers, each
refrigerant circuit is furnished with a replaceable core type
filter-drier. The core assembly of the replaceable core drier
consists of a filter core held tightly in the shell in a manner that
allows full flow without bypass. Pressure drop across the filter
drier must not exceed the following values.
A condenser liquid line service valve is provided for isolating
the charge in the condenser, but also serves as the point from
which the liquid line can be pumped out. With the line free of
refrigerant, the filter-drier core(s) can be easily replaced.
System Adjustment
To maintain peak performance at full load operation, the
system superheat and liquid subcooling may require
adjustment. Read the following subsections closely to
determine if adjustment is required.
Liquid Line Sight Glass
The color of the moisture indicator is an indication of the
dryness of the system and is extremely important when the
system has been serviced. Immediately after the system has
been opened for service, the element may indicate a wet
condition. It is recommended that the equipment operate for
approximately 12 hours to allow the system to reach
equilibrium before deciding if the system requires a change of
drier cores.
Bubbles in the sight glass at constant full load indicates a
shortage of refrigerant, a plugged filter-drier, or a restriction in
the liquid line. However, it is not unusual to see bubbles in the
sight glass during changing load conditions.
Refrigerant Charging
Liquid line subcooling at the liquid shut-off valve should be
between 15 and 20 degrees F at full load. If the unit is at
steady full load operation and bubbles are visible in the sight
glass, then check liquid subcooling.
Expansion Valve
The expansion valve's function is to keep the evaporator
supplied with the proper amount of refrigerant to satisfy the
load conditions.
Before adjusting superheat, check that unit charge is correct
and liquid line sight glass is full with no bubbles and that the
circuit is operating under stable, full load conditions.
The suction superheat for the suction leaving the evaporator is
set at the factory for 10 to 12 degrees F at full load. To have
PERCENT CIRCUIT
LOADING (%)
DROP ACROSS
PSI (KPA)
100%
10 (69)
75%
8 (55.2)
50%
5 (34.5)
25%
4 (27.6)