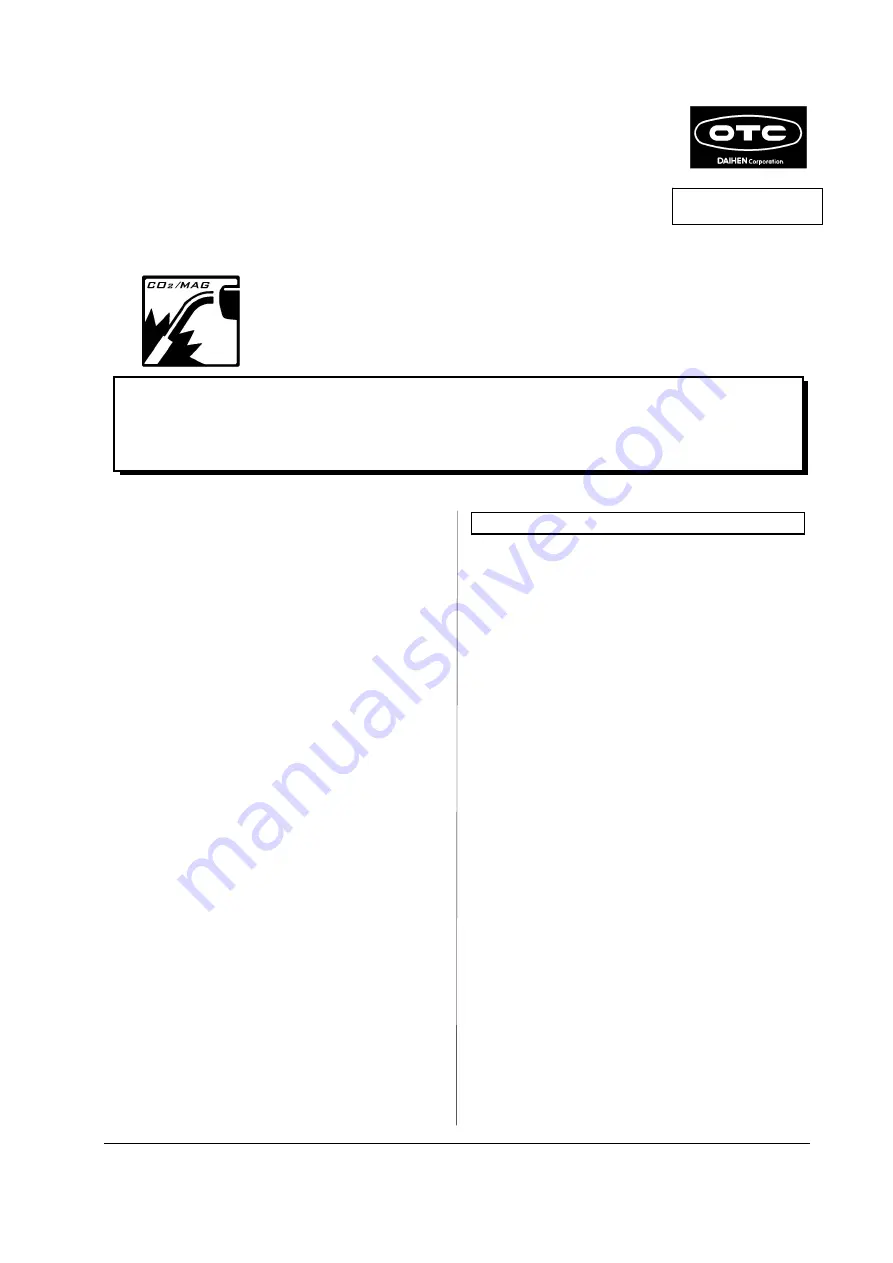
Welding Torch for Robot
Coaxial Power Cable for Robot
<Shock sensor built-in type>
RT3500S /H /L
RT5000S /H /L
RTW5000S /H /L
RZ3500S /H /L
Thoroughly read this
instruction manual to
operate the units correctly.
•
Installation, maintenance, and repair of this
welding torch shall be made by qualified
persons or persons who fully understand
welding machines to secure the safety.
•
To secure the safety, operation of this welding
torch shall be made by persons who have
knowledge and technical skill to fully
understand the contents of this manual and
handle the machine.
•
Regarding safety education, utilize courses
and classes held by head/branch offices of
the Welding Society /Association and the
related societies/associations, and qualifying
examinations for welding experts/consultant
engineers.
•
After thoroughly reading this manual, be sure
to retain it with the warranty in the place
where the persons concerned can read any
time. Read it again as occasion demands.
•
If incomprehensible, contact our offices. For
servicing, contact our local distributor or sales
representatives in your country.
Our addresses and telephone numbers are
listed in the back cover of this Instruction
Manual.
Contents
①
NOTES ON SAFETY .......................... S1
②
IMPORTANT SAFEGUARDS ............. S2
③
NOTES ON USE
.....................................
S7
1. Specifications
............................................
1
2. Checking the Contents
.............................
6
3.
Installing and Adjusting Procedure of Welding Torch
......
8
3.1 Mounting of Welding Torch on AII-V6 type
Manipulator
....................................................................
8
3.2 Mounting of Welding Torch on AII-B4 Type
Manipulator
...............................................................
14
3.3 Connecting the Water-cooled Torch
(RTW5000S/RTW5000H/RTW5000L)
..................
19
3.4
C o n n e c t i n g t h e H o s e t o A I I - B 4
......................
21
3.5 Handling Instructions for RT series Torch
............
22
3.6 Handling Instructions for RZ series Torch
............
23
4. Coaxial Power Cable for Robot
...........
25
4.1 Type of Coaxial Power Cables
...............................
25
4.2 When Using the DL Welding Power Supply
.........
26
4.3 Connecting the Coaxial Power Cable
...................
28
4.4 Cutting the Liner
........................................................
29
4.5 Liner Crump Function
..............................................
30
5. Setting the Robot Controller
.................
31
5.1 Checking the Tool Parameter
.................................
31
5.2 Checking the Shock Sensor Operation
................
33
6. Troubleshooting
.....................................
34
7.
Replacement Parts for Various Wire Diameters .....
35
7.1 Replacement Parts for Various Wire Diameters
of Torch
........................................................................
35
7.2 Replacement Parts for Various Wire Diameters
of Coaxial Power Cable
............................................
38
8. Parts List
.................................................
39
Instruction Manual
= Safety and Operation =
Instruction Manual No.
1L10603-E-2
For CO
2
/MAG
Summary of Contents for OTC RT3500S
Page 2: ......