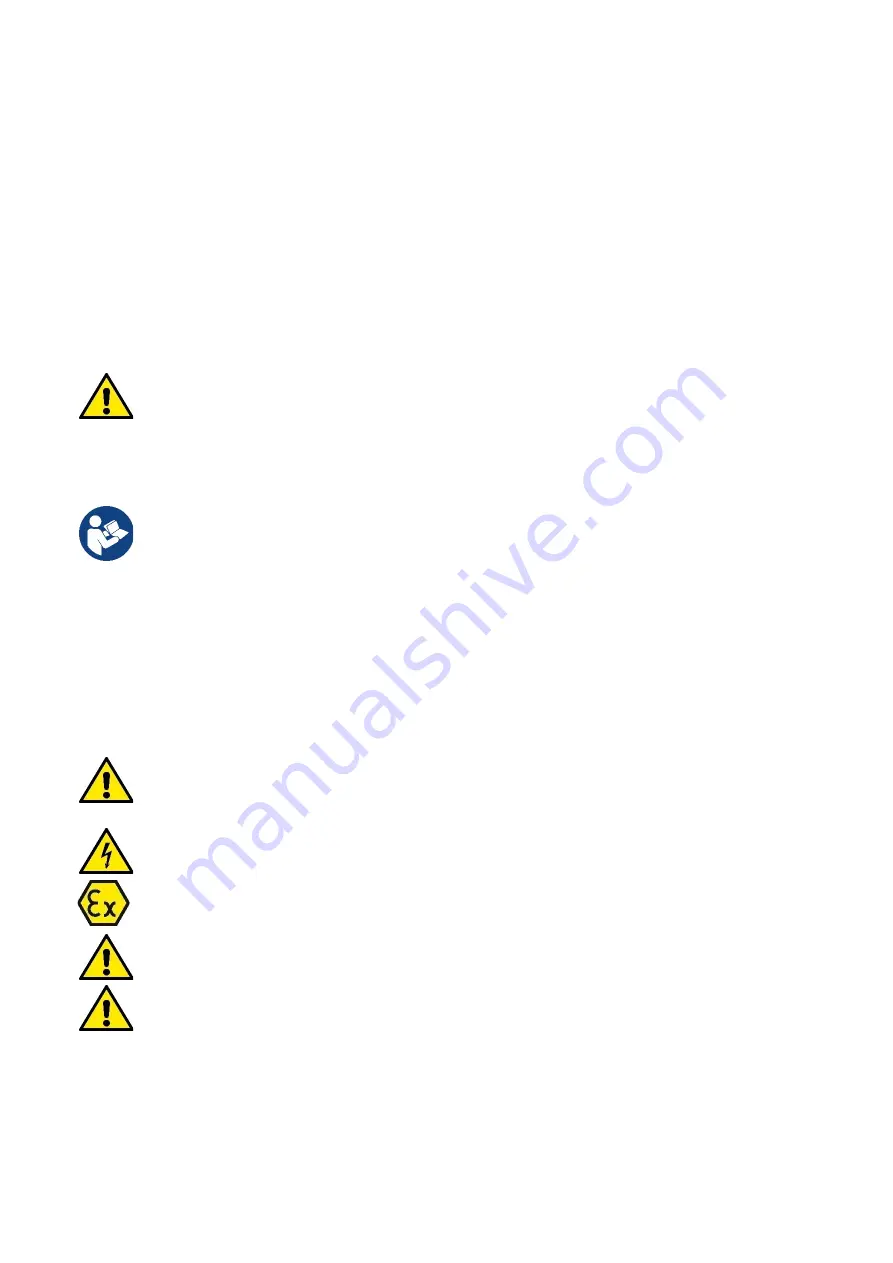
ENGLISH
15
7.1
General start-up procedure
This procedure applies to new installations as well as after service inspections if start-up takes place some time after the pump was placed
in the tank.
-
After long periods of storage, check the conditions of the oil in the oil chamber. See also section 8.1 Routine maintenance.
-
Check that the system, bolts, gaskets, pipework and valves etc. are in correct condition.
-
Mount the pump in the system.
-
Switch on the power supply.
-
Check whether the monitoring units, if used, are operating satisfactorily.
-
Check the setting of the float switches or of the level sensors.
-
Check that the impeller can turn freely by briefly starting the motor.
-
Check the direction of rotation. See section 7.2 Direction of rotation.
-
Open the isolating valves, if fitted.
-
Check that the liquid level is above the pump motor.
-
Start the pump and let the pump run briefly, and check if the liquid level is falling.
-
Observe if the discharge pressure and input current are normal. If not there might be air trapped inside the pump (See section 5
Installation).
In case of abnormal noise or vibrations from the pump, other pump failure or power supply failure or water supply
failure, stop the pump immediately. Do not attempt to restart the pump until the cause of the fault has been found and
the fault corrected.
After one week of operation or after replacement of the shaft seal, check the condition of the oil in the chamber. For pumps without sensor,
this is done by taking a sample of the oil. See section 8. Maintenance and service for procedure. Every time the pump has been removed
from the tank, go through the above procedure when starting up again.
7.2
Direction of rotation (for three-phase pumps)
The pump may be started for a very short period without being submerged to check the direction of rotation.
Check the direction of rotation before starting up the pump. An arrow on the motor housing indicates the correct direction of rotation.
Correct direction of rotation is clockwise when viewed from above.
Checking the direction of rotation
The direction of rotation should be checked in the following way every time the pump is connected to a new installation.
Procedure
1.
Let the pump hang from a lifting device, e.g. the hoist used for lowering the pump into the tank.
2.
Start and stop the pump while observing the movement (jerk) of the pump. If connected correctly, the pump will rotate clockwise,
i.e. it will jerk counter-clockwise. See fig.7 If the direction of rotation is wrong, interchange any two of the phases in the power
supply cable.
8. MAINTENANCE AND SERVICE
Routine maintenance work, limited to checking, cleaning or replacing limited parts, may be carried out only by expert and
qualified personnel, provided with suitable equipment, who know the safety regulations for the working environment and have
read and carefully checked the content of this manual and of any other documentation attached to the product.
Special maintenance or repairs must be entrusted to authorised Dab Pumps service centres.
Before starting any work on the system or troubleshooting, ensure that the main switch is off and that the power
supply cannot be switched on again accidentally. Check that all the protection systems are correctly connected and
that all the rotating parts are stopped.
Maintenance work on explosion-proof pumps must be carried out by DAB Pumps or a service workshop authorized
by DAB Pumps.
However, this does not refer to hydraulic components such as the pump body, the impeller and the mechanical seal.
The replacement of the cable must be carried out exclusively by the manufacturer’s service centre or by another
qualified person.
The pump may have been used for pumping liquid that is harmful to health, contaminated or toxic. Take all the
precautions concerning health and safety before carrying out maintenance or repairs.
Use genuine spare parts only for repairs.
Select the spare parts to be ordered, consulting the exploded drawings available on the DAB Pumps site or the DNA selection software.
The manufacturer declines any responsibility for eventual damages to persons, animals or things for maintenance and repair interventions
carried out by unauthorized personnel or with no genuine spare parts.
Specify the following information when ordering spare parts:
1. The type of electric pump.
2. Serial number and manufacturing year.
Summary of Contents for FX Series
Page 66: ...60 5 2 3a 4 4a 6 EN 60079 14 4mm2 10 10 10 m DAB pumps 6 1 15 15 6 2 FX RANGE k1 k2 6 1 150 C...
Page 67: ...61 7 7 1 8 1 7 2 5 8 7 2 1 2 7 8 Dab Pumps...
Page 71: ...65 5 5 6 6 DAB 7 7 DAB 1 1 7 2 2 2 DAB 3 3 4 4 5 5 6 6 DAB...
Page 86: ...80 6 1 15a 15b 6 2 FX RANGE k1 k2 6 1 150 C 7 7 1 8 1 7 2 5 8 7 2...
Page 195: ...189 7 7 1 8 1 7 2 5 8 7 2 1 2 7 8 Dab Pumps...
Page 199: ...193 2 2 DAB 3 3 4 4 5 5 6 6 DAB...
Page 224: ...218 5 2 3a 4 4a 6 EN 60079 14 4mm2 10 10 10...
Page 225: ...219 6 1 15a 15b 2 6 FX RANGE 150 C Restart Restart 7 1 7 8 1 S1...
Page 226: ...220 S2 Restart 8 2 7 1 2 7 8...
Page 227: ...221 DNA 1 2 3 4 1 8 3000 20 3000 150 C 40 C 8 3000 1...
Page 229: ...223 3 8 www Dabpumps com 9 1 1 2 2 3 4 4 5 5 6 7 7 8 8 9 9 1 1 2 2 3 3...
Page 236: ...230 EN 60079 14 4mm2 10 10 10 DAB pumps 6 1 15a 15b 6 2 FX RANGE k1 k2 6 1 150 7...
Page 237: ...231 7 1 8 1 7 2 5 8 7 2 1 2 7 8 Dab Pumps DAB pumps DAB pumps...
Page 238: ...232 DAB Pumps DNA 1 2 3 4 8 1 3000 20 3000 DAB Pumps 40 150 Ex 10 000 8 3000 1 2 1 3 4 20...
Page 241: ...DRAWINGS 235 Fig 3 Fig 3a Fig 4 Fig 4a...
Page 242: ...DRAWINGS 236 Fig 5 Fig 6 Fig 7 Fig 8 Fig 9 Fig 10...
Page 243: ...DRAWINGS 237 Fig 11 Fig 12...
Page 244: ...DRAWINGS 238 Fig 13 Fig 14...
Page 245: ...DRAWINGS 239 Fig 15a Wiring Diagram...
Page 246: ...DRAWINGS 240 CB Booster for Grinder FX Fig 15b Wiring Diagram...