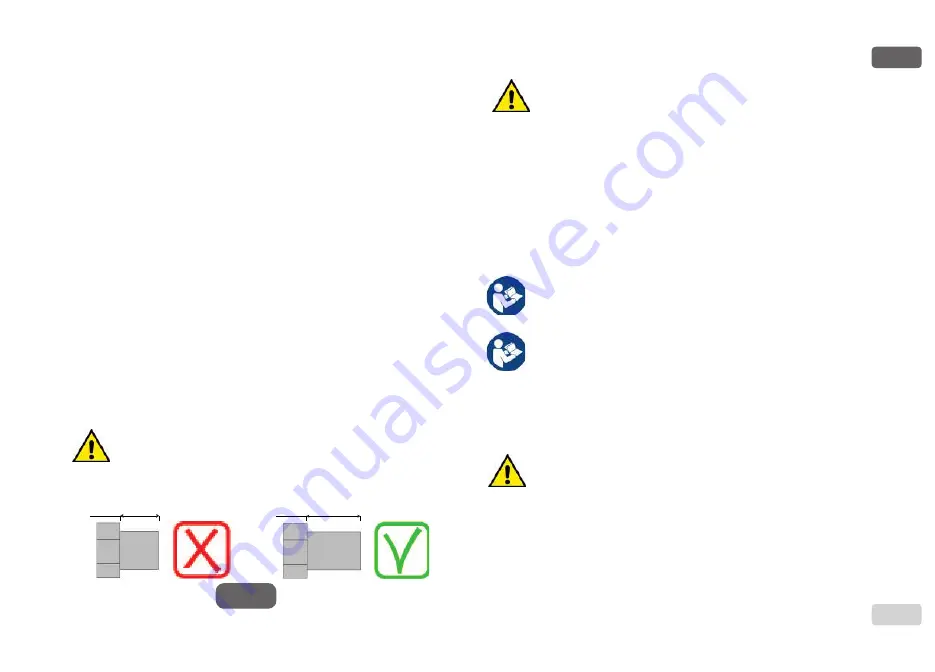
ENGLISH
EN
46
•
The distance of at least 10mm between Face E of the system and any
wall is obligatory to ensure ventilation through the grids provided • I f
you expect to have to drain the system from its discharge door and
not from the system, leave a further distance sufficient to manoeuvre
the drainage cap.
•
The distance of at least 10mm between Face B of the system and
an obstruction is obligatory to let out the power supply cable to the
mains socket.
•
The distance of at least 200mm between Face A of the system and an
obstruction is recommended so as to be able to remove the door and
gain access to the technical compartment.
If the surface is not flat, unscrew the foot that is not touching and adjust
its height until it contacts the surface so as to ensure the stability of the
system. The system must in fact be placed in a safe and stable position,
ensuring that its axis is vertical: it must not be in an inclined position.
2.1.1 Hydraulic connections
Make the connection at input to the system through the mouth on Face F
marked “IN” in Fig.6 (suction connection). Then remove the cap using a
screwdriver. Make the connection at output from the system through the
mouth on Face F marked “OUT” in Fig.6 (delivery connection). Then re
-
move the cap using a screwdriver.
All the hydraulic connections of the system to the plant to which it can be
connected are of the threaded female type 1” GAS, made of brass.
I
f you intend to connect the product to the plant with fittings that
have a diameter larger than the normal 1” pipe (for example the
ring nut in the case of fittings in 3 pieces), make sure that the 1”
Gas male thread of the coupling protrudes at least 25mm from
the above diameter (see Fig.7).
Figure 7
< 25
mm
> 25
mm
The brass threads are housed in technopolymer seats. When
making the connection watertight by adding material (e.g. Teflon,
hemp,...) ensure that the gasket is not too thick: under the action
of an adequate tightening torque (e.g. long handled pipe wrench),
the excess material could exert abnormal force on the technop
-
olymer seat, damaging it irremediably.
With reference to its position with respect to the water to be pumped, the
installation of the system may be defined “above head” or “below head”. In
particular the installation is defined “above head” when the pump is placed
at a level higher than the water to be pumped (e.g. pump on the surface
and water in a well); vice versa it is “below head” when the pump is placed
at a level lower than the water to be pumped (e.g. overhead cistern and
pump below).
If the vertical installation of the system is of the “over head” type,
it is recommended to fit a non-return valve in the suction section
of the system; this is to allow the operation of loading the system
(par. 2.1.2).
If the installation is of the “over head” type, install the suction pipe
from the water source to the pump in such a way as to avoid the
formation of goosenecks or siphons. Do not place the suction
pipe above the pump level (to avoid the formation of air bubbles
in the suction pipe). The suction pipe must draw at its entrance
at a depth of at least 30cm below the water level and must be
watertight along its whole length, as far as the entrance to the
electropump.
The suction and delivery pipes must be fitted so that they do not
exert any mechanical pressure on the pump.
2.1.2.Loading Operation
Installation above head and below head
Installation “above head” (par. 2.1.1): access the technical compartment
and, using a screwdriver, remove the filling cap (Fig.3_point 6). Fill the
system with clean water through the loading door, taking care to let the air
out. If the non-return valve on the suction pipe (recommended in paragraph