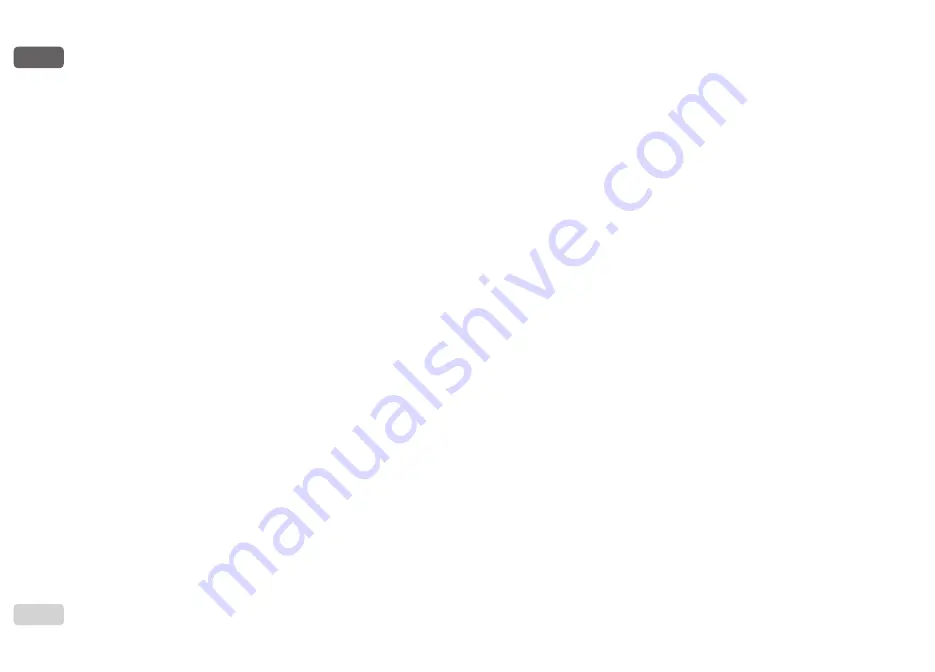
ENGLISH
GB
57
INDEX
Key
60
Warnings
60
Responsibility
61
1.
General
61
1.1
Description of the Integrated Inverter
62
1.2
Integrated expansion vessel
62
1.3
Integrated electropump
63
1.4
Technical characteristics
64
2. Installation
65
2.1
Vertical Configuration
65
2.1.1
Hydraulic connections
66
2.1.2
Loading operation – Installation above head and below head
67
2.2
Horizontal configuration
67
2.2.1
Hydraulic connections
68
2.2.2
Orientation of the interface panel
68
2.2.3
Loading operation – Installation above head and below head
69
3.
Commissioning 69
3.1
Electrical connections
69
3.2
Configuration of the integrated inverter
70
3.3
Priming
70
4.
Protection systems 71
4.1
Description of blockages
71
4.1.1
“BL”
AAnti Dry-Run (Protection against dry running)
71
4.1.2 Anti-Cycling (Protection against continuous cycles without utility request)
72
4.1.3 Anti-Freeze (Protection against freezing of water in the system)
72
4.1.4
“BP1” Blockage due to fault of the internal pressure sensor
72
4.1.5 PB” Blockage due to line voltage outside specifications
72
4.1.6
“SC” Blockage due to short circuit between the motor phases
72
4.2
Manual reset of error conditions
73
4.3
Self-reset of error conditions
73
5. Inverter electronic control and user interface 73
5.1 Operation with control unit
73
5.1.1 Functions made available by control units
74
5.1.2 Electrical connections of utility inputs and outputs
74
5.1.3 Safety mode operation
74
5.1.4 Control unit function setup
75
5.1.5 Association and disassociation of e.sybox and control unit
75
6. The keypad and the display 76
6.1
Direct access with a combination of keys
77
6.2
Access by name with a drop-down menu
80
6.3
Structure of the menu pages
81
6.4
Blocking parameter setting by Password
82
6.5
Enabling and disabling the motor
82
7.
Meaning of the individual parameters 82
7.1
User Menu
82
7.1.1
Status
82
7.1.2
RS: Rotation speed display
82
7.1.3
VP: Pressure display
82
7.1.4
VF: Flow display
82
7.1.5
PO: Absorbed power display
83
7.1.6
C1: Phase current display
83
7.1.7 Operating hours and number of starts
83
7.1.8
PI: Power histogram
83
7.1.9 Multi-pump system
83
7.1.10 Output flow meter
83
7.1.11
VE: Version display
83
7.1.12
FF: Fault log display
83
7.2
Monitor Menu
84
7.2.1
CT: Display contrast
84
7.2.2
BK: Display brightness
84
7.2.3
TK: Backlight switch-on time
84
7.2.4
LA: Language
84
7.2.5
TE: Dissipator temperature display
84
7.3
Setpoint Menu
84
7.3.1
SP: Setting the setpoint pressure
84
7.3.2
Setting the auxiliary pressures
84
7.3.2.1
P1: Setting the auxiliary setpoint 1
85
7.3.2.2
P2: Setting the auxiliary setpoint 2
85
7.3.2.3
P3: Setting the auxiliary setpoint 3
85
7.3.2.4
P4: Setting the auxiliary setpoint 4
85
7.4
Manual Menu
85
7.4.1 Status
85
7.4.2 RI: Speed setting
85
7.4.3 VP: Pressure display
86
7.4.4 VF: Flow display
86
7.4.5 PO: Absorbed power display
86
7.4.6 C1: Phase current display
86
7.4.7 RS: Rotation speed display
86
7.4.8 TE: Dissipator temperature display
86
7.5
Installer Menu
86
7.5.1 RP: Setting the pressure fall to restart
86
7.5.2 OD: Type of plant
86
7.5.3 AD: Address configuration
86
Summary of Contents for DAB E.SYBOX
Page 3: ......