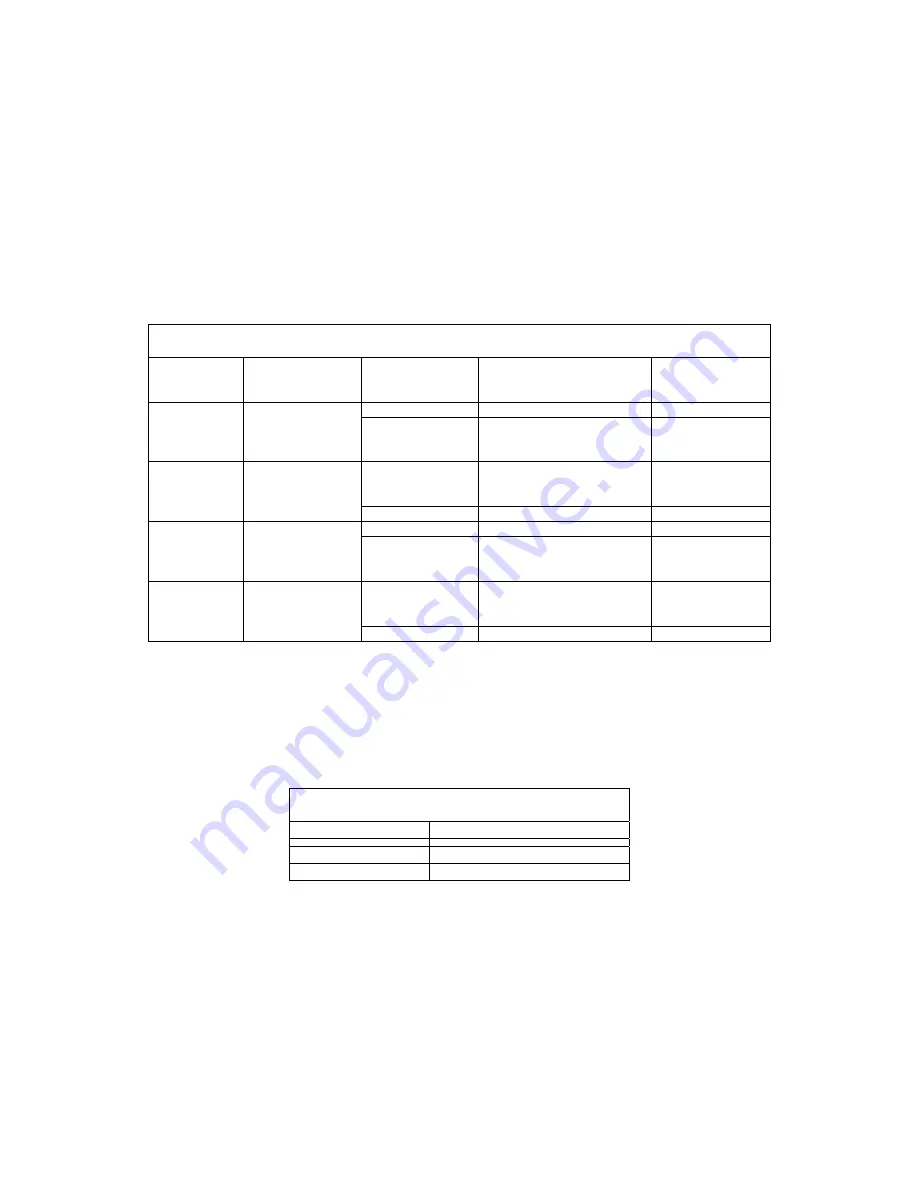
ENGLISH
86
6.6.15.5 Setting low pressure detection (KIWA)
The minimum pressure switch that detects low pressure can be connected to any input (for electrical connections,
refer to paragraph 2.3.3).
The low pressure detecting function is obtained by setting the parameter Ix, for the input to which the enabling signal
has been connected, on one of the values in Tabella 26.
Activation of the low pressure detection function generate a system block after time T1 (see T1: Tempo di
spegnimento dopo il segnale bassa pressione par. 6.6.2). This function is envisaged to connect the input to a signal
from a pressure switch that indicates excessively low pressure on pump intake.
When this function is enabled, the symbol F4 is shown on the STATUS line of the main page.
When in the F4 error condition, the input must be deactivated for at least 2 seconds before the system unblocks. The
function behaviour is summarised in Table 26.
When several low pressure detection functions are configured at the same time on different inputs, the system
indicates F4 when at least one function is activated and clears the alarm when none are activated.
Response of system enable and fault reset function according to setting of INx and input
Parameter
value
INx
Input
configuration
Input status
Operation
Display
10
Active with high
signal on input
(NO)
Absent Normal None
Present
System block due to low
pressure on intake;
aut manual reset
F4
11
Active with low
signal on input
(NC)
Absent
System block due to low
pressure on intake;
aut manual reset
F4
Present Normal None
12
Active with high
signal on input
(NO)
Absent Normal None
Present
System block due to low
pressure on intake.
Manual reset
F4
13
Active with low
signal on input
(NC)
Absent
System block due to low
pressure on intake.
Manual reset
F4
Present Normal None
Table 26: Low pressure signal detection (KIWA)
6.6.16 Setup of outputs OUT1, OUT2
This section illustrates the functions and possible configurations of the outputs OUT1 and OUT2 via parameters O1
and O2.
For electrical connections, see par. 2.3.4.
The default settings are those in Table 27.
Default output settings
Output Value
OUT 1
2 (fault NO closes)
OUT 2
2 (Pump running NO closes)
Table 27: Default output settings
6.6.16.1 O1: Output 1 function setting
Output 1 notifies of an active alarm (i.e. that there is a system block). The output enables use of a normally closed or
normally open voltage-free contact.
Parameter O1 is associated with the values and functions specified in Table 28.
6.6.16.2 O2: Output 2 function setting
Output 2 notifies of electric pump running status (pump on/off). The output enables use of a normally closed or
normally open voltage-free contact.
Parameter O2 is associated with the values and functions specified in Table 28.