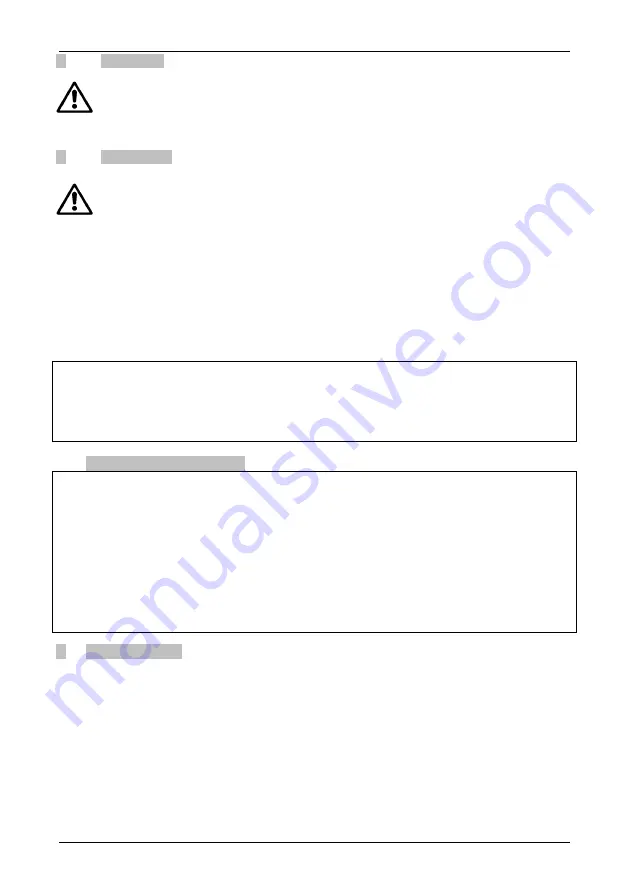
ENGLISH
39
1. GENERAL
Read this documentation carefully before installation.
Installation and functioning must comply
with the safety regulations in force in the country in which the product is installed. The entire
operation must be carried out in a workmanlike manner.
Failure to comply with the safety regulations not only causes risk to personal safety and damage to
the equipment, but invalidates every right to assistance under guarantee.
2. WARNINGS
2.1 Skilled
personnel
It is advisable that installation be carried out by competent, skilled personnel in
possession of the technical qualifications required by the specific legislation in force
.
The term
skilled personnel
means persons whose training, experience and instruction, as well as
their knowledge of the respective standards and requirements for accident prevention and working
conditions, have been approved by the person in charge of plant safety, authorizing them to perform
all the necessary activities, during which they are able to recognize and avoid all dangers. (Definition
for technical personnel IEC 60634).
2.2 Safety
Use is allowed only if the electric system is in possession of safety precautions in accordance with the
regulations in force in the country where the product is installed (for Italy, IEC 64/2).
2.3 Responsibility
The Manufacturer does not vouch for correct operation of the ACTIVE DRIVER or for any damage
that it may cause if it has been tampered with, modified and/or run outside the recommended work
range or in contrast with other indications given in this manual. The Manufacturer declines all
responsibility for possible errors in this instructions manual, if due to misprints or errors in copying.
The Manufacturer reserves the right to make any modifications to products that it may consider
necessary or useful, without affecting the essential characteristics.
2.4
PARTICULAR WARNINGS
Before working on the electrical or mechanical part of the system, always turn off the mains voltage.
Wait at least five minutes after the power supply to the machine has been switched off before opening
the appliance.
The condenser of the continuous intermediate circuit remains charged with dangerously high
voltage even after the mains voltage has been switched off.
Only firmly wired mains connections are admissible. The appliance must be earthed (IEC 536 class 1, NEC
and other relevant standards).
Mains terminals may carry dangerous voltage even when the motor is stopped.
In determined calibration conditions, after a power cut the converter may start automatically.
Pay attention: the
motor terminals U, V and W (for the Active Driver M/M 1.1 the motor terminals R
and S)
may carry dangerous voltages even when the converter is not operating.
Do not operate the appliance in direct sunlight.
This appliance may not be used as an “EMERGENCY STOP mechanism” (see EN 60204, 9.2.5.4).
3.
APPLICATIONS
The ACTIVE DRIVER is supplied already set up for installation in the following models:
ACTIVE DRIVER M/T: fed with a single-phase line, controls electropumps with a 230V standard
three-phase asynchronous motor.
ACTIVE DRIVER M/M: fed with a single-phase line, controls electropumps with a 230V standard
single-phase asynchronous motor.
ACTIVE DRIVER T/T: fed with a three-phase line, controls electropumps with a 400V standard
three-phase asynchronous motor.