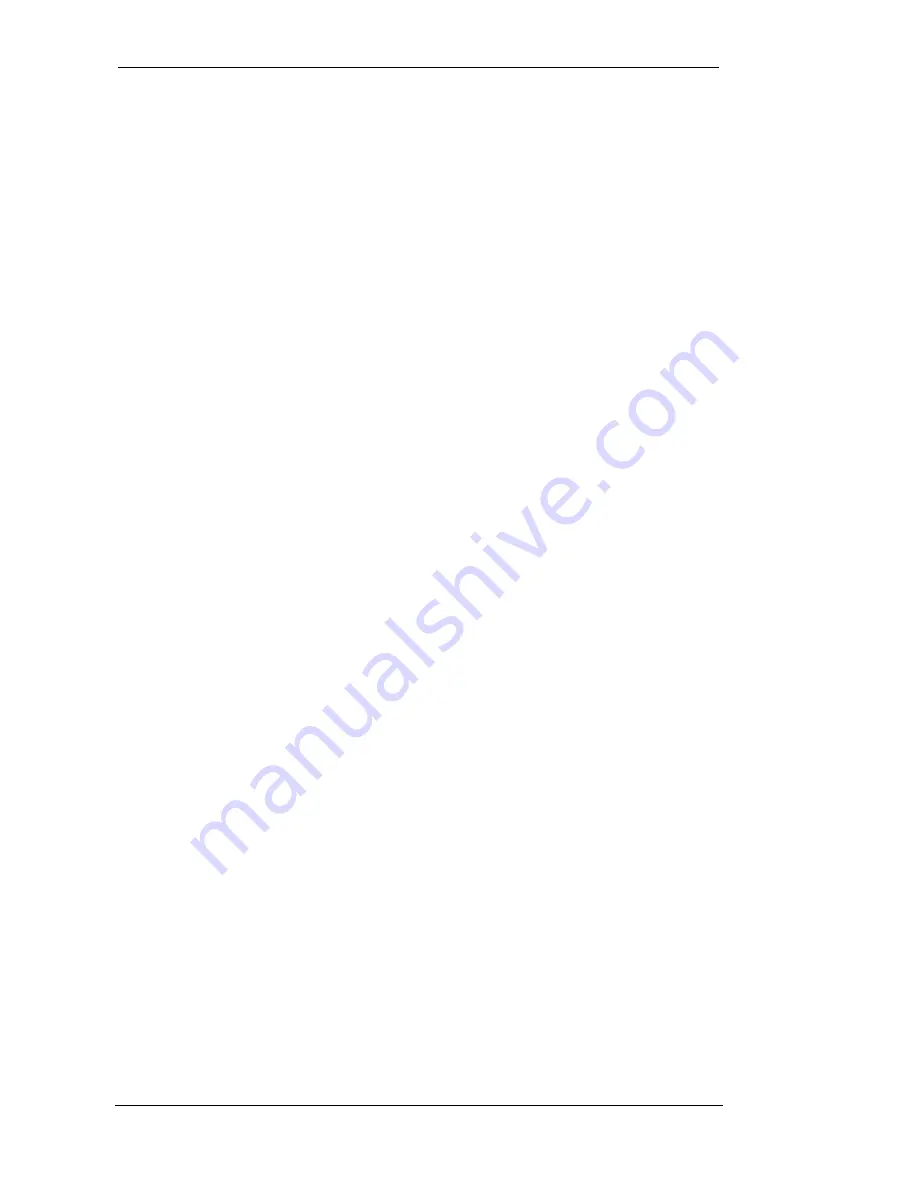
Q200 User Manual
THE Q200 IN USE
10-4
200120/Revision 10
•
The operating configuration of the instrument should be chosen so that, so far as is
possible, the readings of greatest interest (usually around the pass/fail level of the
component under test) are in the middle of the configured operating range. This will
not be possible in all cases, especially if the maximum sensitivity is required from
the instrument, but it is good practise to try to operate the instrument in such a
manner as to allow measurements both above and below those of most interest to
be made.
The operational range of the instrument can be varied over wide limits by
appropriate choice of inlet configuration and trace gas concentration. Appendix A
gives a list of the operating ranges of the instrument with the various inlet
configurations at a range of trace gas concentrations.
By and large it is better to modify the operating range of the instrument by changing
the trace gas concentration rather than by changing the inlet. The H sinter is the
first choice inlet with the M and L sinters being second and third choices
respectively. Note that the L sinter, although offering the ability to detect high level
leaks, has a comparatively poor response and clear-down time and should only be
used with caution.
•
In some applications a total integrated leak rate is required from a component
under test. This type of test is performed when the pass/fail criterion is that the total
leak rate from all the potential leak sites in the component under test does exceed
a specified figure.
In outline, the component to be tested is placed inside a chamber that is purged
with clean air to remove any SF
6
background and is then sealed. The sealed
chamber is allowed to stand for a specified period of time to allow the concentration
of SF
6
to build up in the space within the chamber surrounding the item under test.
The concentration of SF
6
in this space is measured using the Q200 and a
calculation may be performed to convert this concentration into leak rate units. If the
incubation time is kept constant, the pass/fail level can be defined in terms of
concentration units, rather than calculating the equivalent leak rate.
Although this is a commonly used technique, some care is required to ensure that
the test is carried out in a manner that will ensure that reliable results are obtained.
The majority of difficulties that are encountered when this technique is used are
related to background levels of SF
6
and the operator not taking the appropriate
steps to minimise their effects.
In order to minimise the time that is required to produce a measurable
concentration build up within the chamber, it is important to purge the chamber
efficiently to minimise any SF
6
background in the chamber prior to sealing the
chamber at the start of the test. The chamber background can result from a
significant SF
6
background in the ambient air or from SF
6
left in the chamber from
the previous test. The air supply that is used for this purging phase must be clean. If
the air supply is derived from a compressor, it will be necessary to have oil and
water traps in the supply line. This will ensure that there are no contaminants
introduced into the test chamber that will have either an immediate or cumulative
deleterious effect on the performance of the Q200.
When a measurement of concentration is to be made, the way that the instrument is
zeroed prior to making the measurement must be considered. It is important that
the instrument is zeroed in an air sample that is representative of the composition of
the air that was used to purge the chamber at the start of the incubation time. This
Summary of Contents for Q200
Page 1: ...Uson Q200 User Manual Revison 10 Updated September 2018...
Page 3: ......
Page 7: ......
Page 11: ......
Page 19: ......
Page 21: ......
Page 33: ......
Page 47: ......
Page 59: ......
Page 63: ......
Page 67: ......
Page 75: ......
Page 79: ......
Page 81: ......
Page 83: ......
Page 89: ......
Page 91: ......