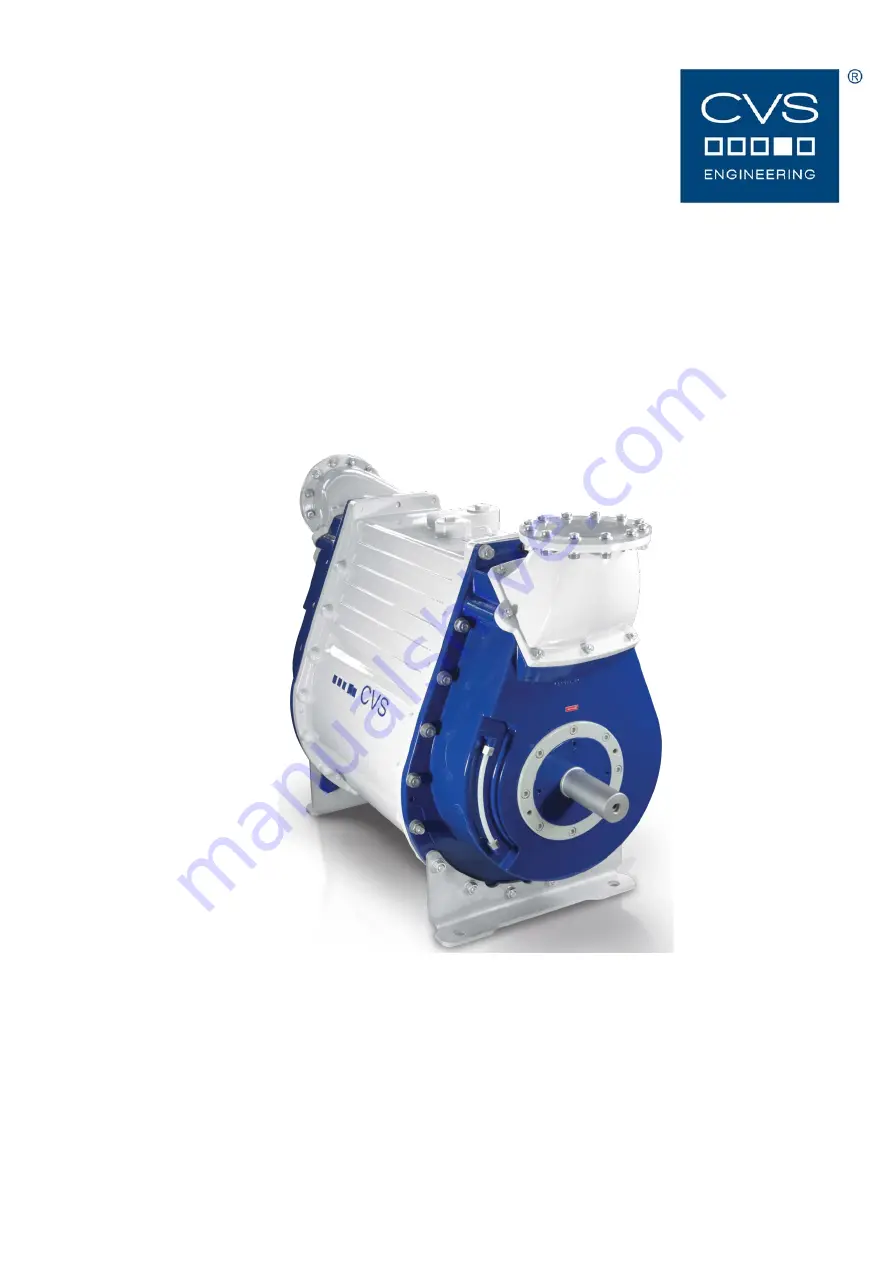
Contents
Mounting instructions
VacuStar WR 2500 / WR 3100 / WR 4000
Doc-ID: 5040 / MA / EN
Release: Rev. 03 / 13/09/2017
Prior to installing the VacuStar WR and putting it into operation you must have read and understood
these instructions. These instructions are only valid together with the operating instructions, they do
not replace them!