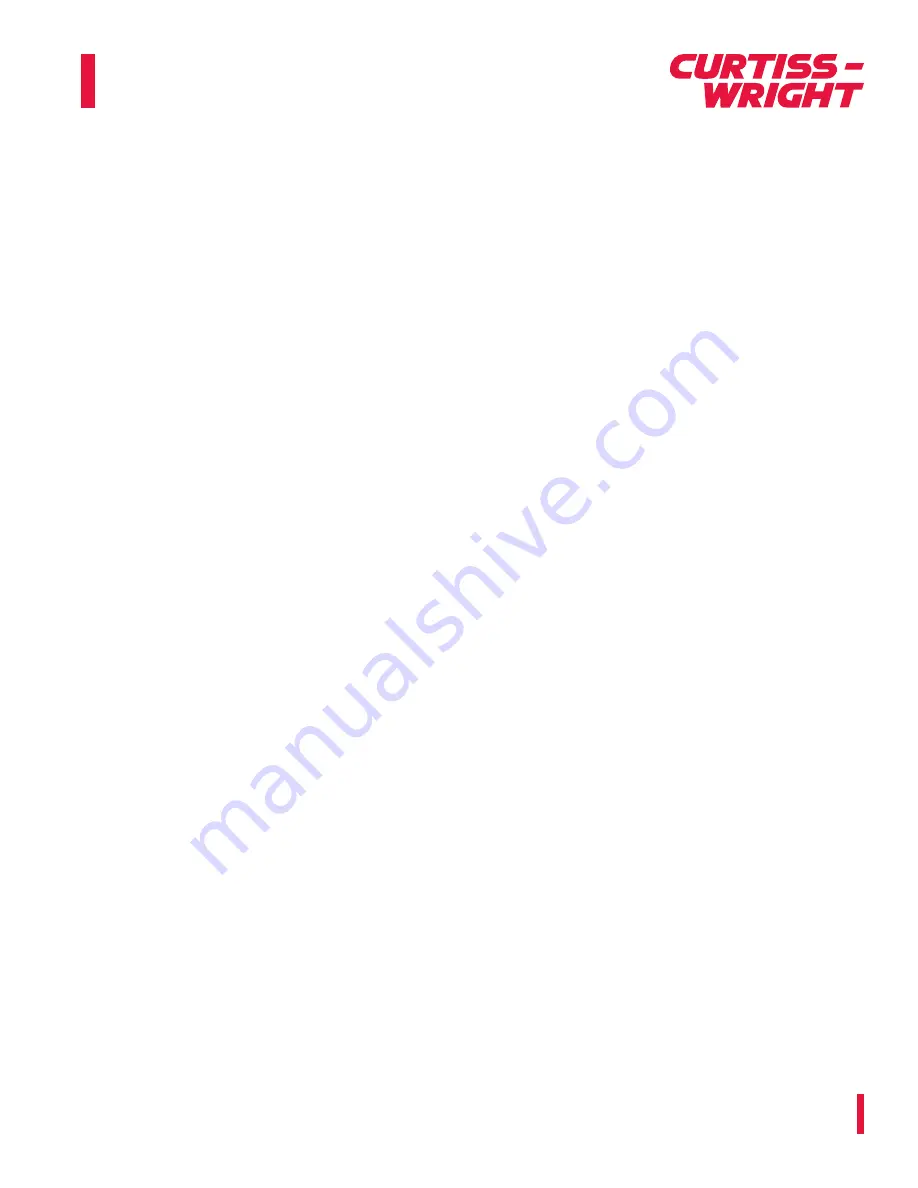
Pre-Installation Safety Information
The valves shall be installed, operated and maintained in accordance with these procedures. Always follow standard safety procedures set forth
by the law and regulations required by your employer, end-users, and jurisdiction authorities. Any transportation, unpacking, lifting, installation,
operation, and maintenance of the system shall be made by expert, trained, and qualified personnel.
Warning: When lifting a valve with an attached actuator assembly, be aware that the center of gravity may be above the lifting point.
Additional support must be provided to prevent the valve and actuator assembly from flipping or rotating. Failure to do so can cause serious
injury to personnel and/or damage to the equipment.
Installation
Verify the valve’s name plate against the packing list and applicable documents for proper identification. Use lifting devices rated for the
equipment weight and suitable for safe installation.
Valves shall be installed in a manner that will not support the weight of the line and line expansion; strain shall be isolated external to the valve.
Optimal installation requires the valve to be installed with the flow arrow marked on the valve body pointing downstream of the pump or pressure
source. Position the valve to allow access to the operator. Operator and cartridge removal must be possible for in-line service.
Flanged valves should be installed using the proper gasket and procedures specified by National and International Standards/Codes. Butt weld
ends shall be welded in accordance with proper Standard Code welding procedures. Welding shall be done on the valve body before installing the
valve cartridge.
Install the valve operator according to the manufacturer’s guidelines. Refer to pneumatic, hydraulic or electric actuators section for setting or
adjusting the open and close stops for the operator.
Fully stroke the valve through its operational range multiple times to ensure the proper operation. Note any special installation instructions
specific to the application.
Operations
Although the valve is bi-directional and can seal in either direction, ensure that the valve has been installed with designated flow direction. The
valve strokes 90° between full open and closed positions. The valve is torque seated, with the maximum closing torque applied at the end of the
close stroke. Under high differential pressures, the un-seating torque may be as high or higher than the seating torque.
Note: Do not over torque the valve into the closed position. Over torque may cause damage to the valve and void the warranty.
Pneumatic, Hydraulic or Electric Actuators
If the actuator has been installed prior to receipt, check that air, hydraulic, and electrical supply lines are connected per the manufacturer’s
specifications. Verify that the actuator mounting bolts are properly tightened.
If the actuator has not been previously installed on the valve, mount the actuator and tighten the bolting to the proper torque specification per the
provided Top Assembly drawing. Install the pneumatic, electrical, or hydraulic connections to the actuator per the manufacturer’s instructions.
Caution: Adjust the operator stops to engage at the specified stroke position. The valve does not have integral stops.
Maintenance
The valve does not require periodic lubrication to provide continuous trouble-free service. If the valve does not seal properly, or if there are
difficulties smoothly stroking the valve, it may be due to foreign object debris within the cartridge assembly. Cleaning may be required in order to
remove the debris.
Installation, Operation, and Maintenance
Enertech Ball Cartridge Valve (BCV) Manual
Nuclear
CWNUCLEAR.COM
CONTACT INFORMATION:
2950 E Birch St, Brea, CA 92821 USA
[email protected] | +1.714.528.2301
IOM - 1334 - 11.2018 - ET