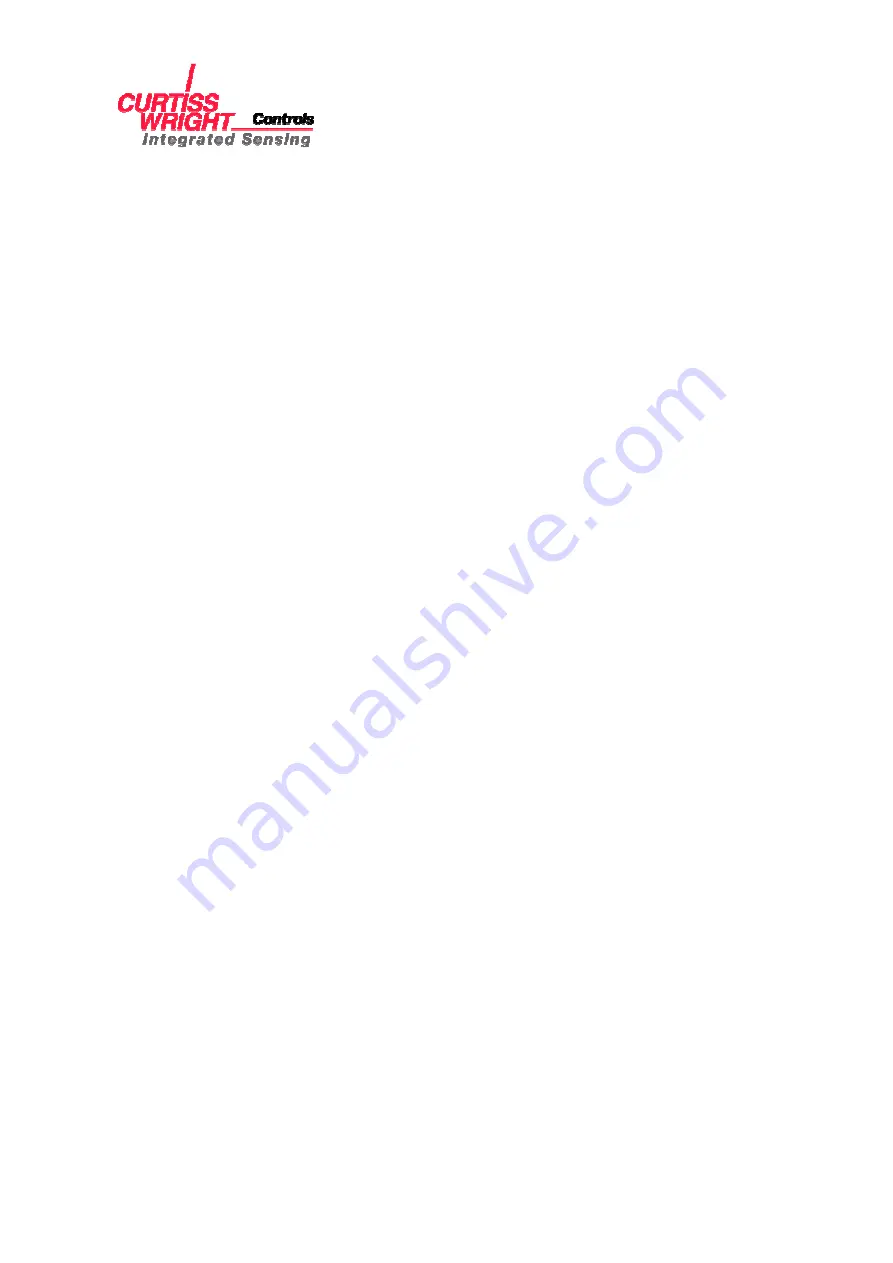
PIM 417-O
PITOT-STATIC LEAK TESTER TYPE D51600
Issue 5
November 2009
Page 9
The front cover to the battery compartment is removeable and is fitted with a polypropylene retaining
strap, or lanyard. Sealing is provided by a neoprene foam seal and the cover is secured to the case
using two 90 degree, or % turn, slotted Dzus fasteners. The battery compartment covers are
manufactured from nickel-plated aluminium alloy and when the batteries are sealed within the
compartment, they are fully protected against the environment.
During operation, the system monitors power usage and provides a front panel indication when the
energy levels drop below 15 minutes (approximately) of available power.
7. PNEUMATIC ASSEMBLY
The pump, pressure sensor, and valves are mounted on a pneumatic block which is attached to a
metal baseplate to form a single pneumatic assembly; eliminating the need for unnecessary pipework
and connectors. The block, which is manufactured out of aluminium alloy, is hollowed out to form a
180ml. volume reservoir which dampens out pressure pulses and aids control stability. Galleries are
machined in the block to interconnect the pump, pressure sensor, valves and outlet ports.
The baseplate of the pneumatic assembly is secured to one half of the case. There are three
pneumatic ports: the output port for connection to the aircraft, a breather port, and the reference port
for the transducer. The output port, which projects externally from the case, is sealed against leaks and
is protected by a blanking cap which is attached to it by lanyard to minimise loose object hazards.
The pump is of oil-free diaphragm construction, sealed against normal operating environmental
conditions. It is driven by d.c. motor and is capable of delivering up to ± 500 mbar to the output port at
a rate of 4 litres/minute at atmospheric pressure.
Within the PSLT are four miniature d.c. solenoid valves operated from four Pulse Width Modulated
(PWM) ports. Two 3/2 changeover valves control the direction of air flow. The third valve (normally-
closed) is used to vent the controlled pressure to atmosphere during a Vent Cycle. The fourth valve is
a normally-open vent valve with restricted orifice. This provides a slow vent to safely reduce the
system pressure to atmosphere in the event of either a power failure or an overpressure condition.
Pressure measurements are made by a differential silicon transducer connected on one side to
atmosphere (via the reference port), and the other to the controlled pressure source (aircraft pneumatic
systems) via the output port. The transducer interfaces wi1th the microcontroller via an Analogue-to-
Digital Converter (ADC). The transducer has integral signal conditioning and temperature
compensation. The operating range is -340 mbar to 340 mbar and typical compensated accuracy is ±
0.3% Full Scale Output (FSO).