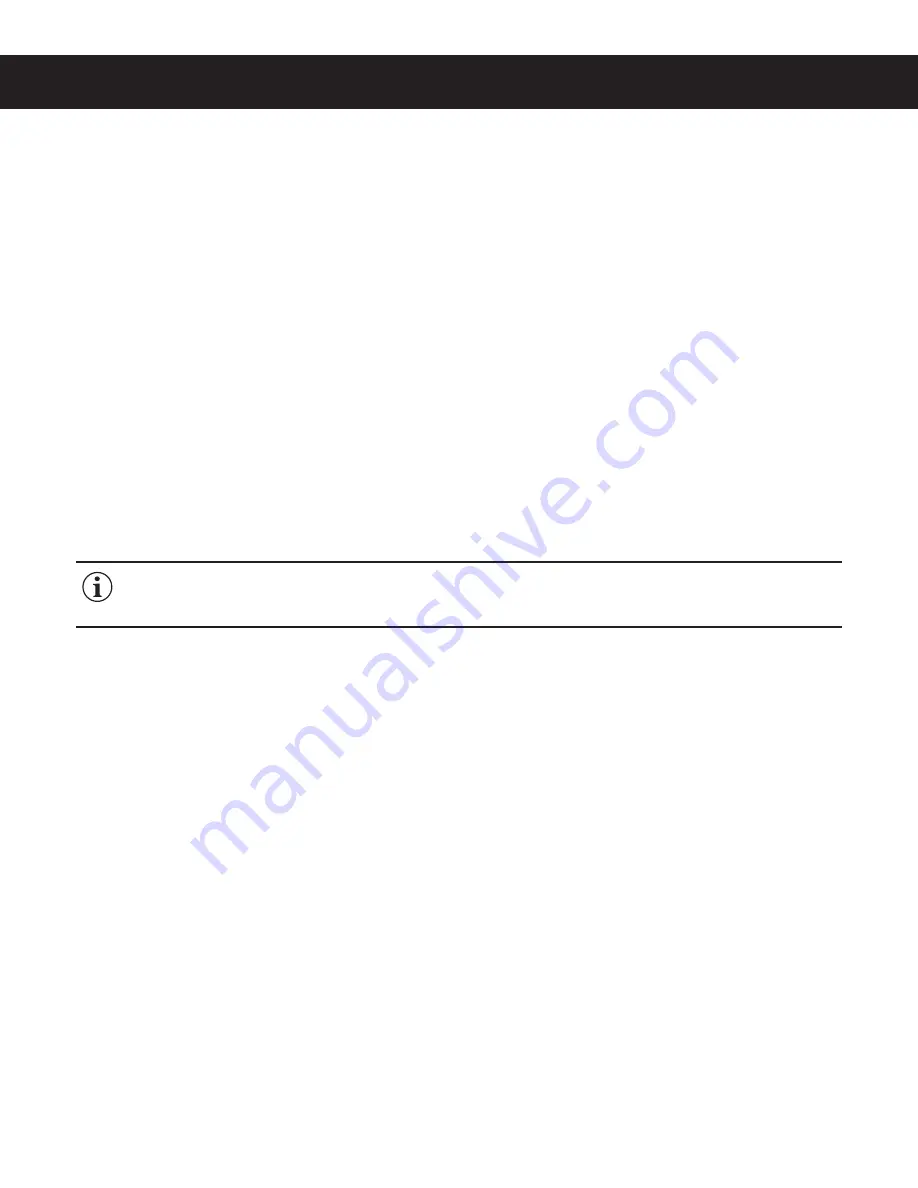
TROUBLESHOOTING GUIDE
TG9
Water Does Not Heat At All
• Check to see if the water level in the tank is in contact with the water level probe. If not, see
Tank Does Not Fill
.
The water will not heat unless it is in contact with the probe.
• If the water heats, but is not hot enough, see
Water Not Hot Enough
.
• If
Ready to brew
appears on the display, but the water is not hot, check the resistance across the leads of the
temperature sensor. If the resistance is less than 10 k and the water is not hot, replace the temperature sensor.
If the sensor resistance is above 10 k when the water is cool, replace the universal control module (UCM).
If
Heating...
appears on the display, but the water is not hot, follow the steps below. The following steps are
performed with the rear toggle switch in the ON position.
1 Check for power across the terminals of the heating element(s). If power is being supplied, remove the wires
and check for an open heating element.
2 If there is no power to the element(s), trace the circuit back (using the ELECTRICAL SCHEMATIC) to the power
DPSEUPmOEPVUXIFSFQPXFSJTMPTU*GUIFSFJTQPXFSJOUPUIFTPMJETUBUFSFMBZ T 443TCVUOPUPVUTFFUIF
following step. On units having two SSRs, be sure to check both.
3 If there is power into a SSR, but not out, check for 5 Vdc (nominal*) across the + and - pins of the SSR(s). If
there is 5 Vdc across the + and - pins of the SSR(s), but no (or low) output voltage at a SSR output terminal,
replace the SSR. If 5 Vdc is not being supplied from the UCM, but
Heating...
appears on the display, check
the wiring from the UCM to the SSR(s). If the wiring is OK, replace the UCM.
Water Too Hot (Boiling or Excessive Steaming)
1 If
Over Temp Sensor
or
Ready to Brew
appears on the display and the water is too hot, go to
Over Temp
Sensor Error Message
.
2 If the display reads
Heating
DPOTUBOUMZmSTUDIFDLUPNBLFTVSFUIBUUIFUFNQFSBUVSFTFOTPSJTBUUBDIFEUJHIUMZ
to the tank and that heat sink compound was used. A properly mounted sensor should have a resistance of
around 7 k when the water is hot. If not, replace the sensor.
3 Check to see if the universal control module (UCM) constantly has +5 Vdc output (nominal) to the solid state
relay (SSR), regardless of the resistance of the temperature sensor. If so, the UCM is probably bad.
4 If the UCM is working properly, check for a shorted SSR.
Over Temp Sensor Error Message
This error message indicates that the universal control module (UCM) has detected a water overheating problem.
The UCM is reading a water temperature in the tank above 210ºF. If the water temperature is too hot, but
Heating...
appears on the display, see
Water Too Hot
. Once the malfunction causing the error is corrected, the
error message must be cleared. To reset the brewer and return to normal operation, turn the toggle switch on the
back of the brewer to the OFF position for 5 seconds, then back on.
1 Check for 5 Vdc (nominal) across the + and - pins of the solid state relay (SSRs). If no power is applied to the
SSR and the heating elements are always on, replace the SSR. On units having two SSRs, check both.
2 Turn off power to the brewer and allow the water tank to cool. Once cool, turn power back on while monitoring
the voltage across the + and - pins of the SSR(s). During normal operation, the voltage should be 5 Vdc, until
the water is hot, then drop to below 1 Vdc. The UCM should be replaced if the voltage reads 5 Vdc constantly
even though
Ready to brew
or
Over Temp Sensor
appears on the display.
3 If the UCM is operating normally, check for a false over-temp error caused by the temperature sensor. Check
the resistance across the leads of the temperature sensor. If the resistance is less than 10 k when the water is
cool, replace the temperature sensor.
G3 BREWERS WITH SSR, TROUBLESHOOTING GUIDE
120817A
IMPORTANT:
Before proceeding, make sure that the control panel temperature is adjusted to compensate
for higher elevations. The factory setting is 200°F. Reduce the temperature setting two degrees for every
1000 feet of elevation above 4000 feet.
Summary of Contents for GEMSS10A1000
Page 27: ...ELECTRICAL SCHEMATICS ES31 GTPS 10 ELECTRICAL SCHEMATIC 061918B SINGLE DOMESTIC 220 VOLT...
Page 30: ...ELECTRICAL SCHEMATICS ES34 515 53 4 5 TWIN DOMESTIC...
Page 31: ...TWIN 3 PHASE WITH TRANSFORMER ELECTRICAL SCHEMATICS ES35 515 53 4 5...
Page 32: ...TWIN 3 PHASE WITHOUT TRANSFORMER ELECTRICAL SCHEMATICS ES36 515 53 4 5...
Page 33: ...TWIN EXPORT ELECTRICAL SCHEMATICS ES37 515 53 4 5...