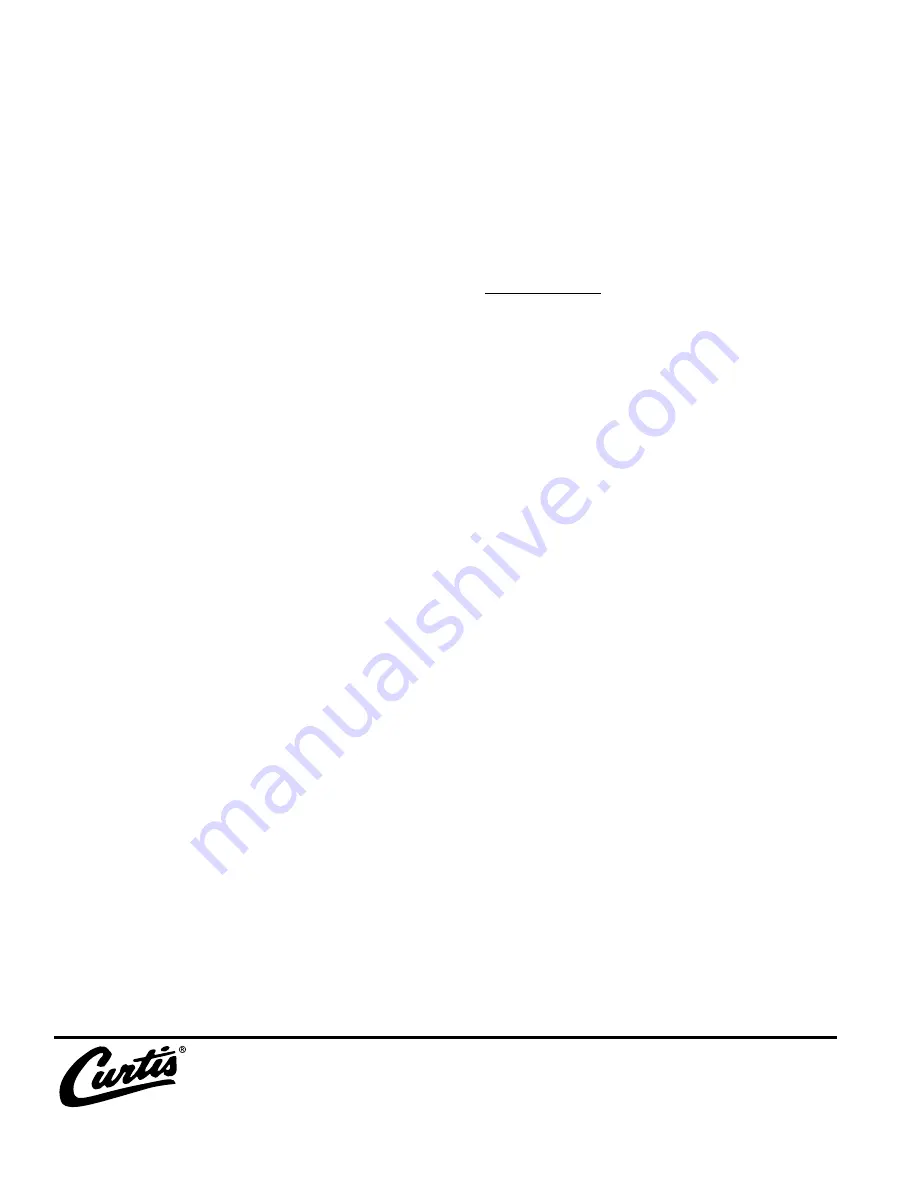
ECN 16604 11/02/15 @ 9.8 revF
Product Warranty Information
Wilbur Curtis Co., Inc. certifies that its products are free from defects in material and workmanship under normal use. The following limited war
-
ranties and conditions apply:
3 years, parts and labor, from original date of purchase on digital control boards.
2
years, parts, from original date of purchase on all other electrical components, fittings and tubing.
1
year, labor, from original date of purchase on all electrical components, fittings and tubing.
Additionally, Wilbur Curtis Co., Inc. warrants its grinding burrs for forty (40) months from date of purchase or 40,000 pounds of coffee, whichever
comes first. Stainless steel components are warranted for two (2) years from date of purchase against leaking or pitting and replacement parts are
warranted for ninety (90) days from date of purchase or for the remainder of the limited warranty period of the equipment in which the component
is installed. All in-warranty service calls must have prior authorization. For authorization, call the Technical Support Department at 1-800-995-0417.
Effective date of this policy is April 1, 2003.
Additional conditions may apply. Go to
www.wilburcurtis.com to view the full product warranty information.
CONDITIONS & EXCEPTIONS
The warranty covers original equipment at time of purchase only. Wilbur Curtis Co., Inc., assumes no responsibility for substitute replacement parts
installed on Curtis equipment that have not been purchased from Wilbur Curtis Co., Inc. Wilbur Curtis Co., Inc. will not accept any responsibility if
the following conditions are not met. The warranty does not cover and is void under the following circumstances:
1) Improper operation of equipment: The equipment must be used for its designed and intended purpose and function.
2) Improper installation of equipment: This equipment must be installed by a professional technician and must comply with all local electrical,
mechanical and plumbing codes.
3) Improper voltage: Equipment must be installed at the voltage stated on the serial plate supplied with this equipment.
4) Improper water supply: This includes, but is not limited to, excessive or low water pressure and inadequate or fluctuating water flow rate.
5) Adjustments and cleaning: The resetting of safety thermostats and circuit breakers, programming and temperature adjustments are the
responsibility of the equipment owner. The owner is responsible for proper cleaning and regular maintenance of this equipment.
6) Damaged in transit: Equipment damaged in transit is the responsibility of the freight company and a claim should be made with the carrier.
7) Abuse or neglect (including failure to periodically clean or remove lime accumulations): Manufacturer is not responsible for variation
in equipment operation due to excessive lime or local water conditions. The equipment must be maintained according to the manufacturer’s
recommendations.
8) Replacement of items subject to normal use and wear: This shall include, but is not limited to, light bulbs, shear disks, “0” rings, gaskets,
silicone tube, canister assemblies, whipper chambers and plates, mixing bowls, agitation assemblies and whipper propellers.
9) Repairs and/or Replacements are subject to our decision that the workmanship or parts were faulty and the defects showed up under normal
use. All labor shall be performed during regular working hours. Overtime charges are the responsibility of the owner. Charges incurred by
delays, waiting time, or operating restrictions that hinder the service technician’s ability to perform service is the responsibility of the owner of
the equipment. This includes institutional and correctional facilities. Wilbur Curtis Co., Inc. will allow up to 100 miles, round trip, per in-warranty
service call.
RETURN MERCHANDISE AUTHORIZATION: All claims under this warranty must be submitted to the Wilbur Curtis Company Technical
Support Department prior to performing any repair work or return of this equipment to the factory. All returned equipment must be repackaged
properly in the original carton. No units will be accepted if they are damaged in transit due to improper packaging. NO UNITS OR PARTS WILL
BE ACCEPTED WITHOUT A RETURN MERCHANDISE AUTHORIZATION (RMA). RMA NUMBER MUST BE MARKED ON THE CARTON
OR SHIPPING LABEL. All in-warranty service calls must be performed by an authorized service agent. Call the Wilbur Curtis Technical Support
Department to find an agent near you.
11/2015 F-3842 rev F
WILBUR CURTIS CO., INC.
6913 Acco St., Montebello, CA 90640-5403 USA | Phone: 800-421-6150 | Fax: 323-837-2410
Technical Support Phone: 800-995-0417 (M-F 5:30
a
.
m
.
- 4:00
p
.
m
.
PST)
Email: [email protected] | Web: www.wilburcurtis.com
Summary of Contents for G4GEMS
Page 5: ...5 Menu Features ...
Page 9: ...9 Brew Access Code ...
Page 13: ...13 Electrical Schematic G4GEMS 10 ...
Page 17: ...17 ...
Page 18: ...18 Page Intentionally Left Blank ...