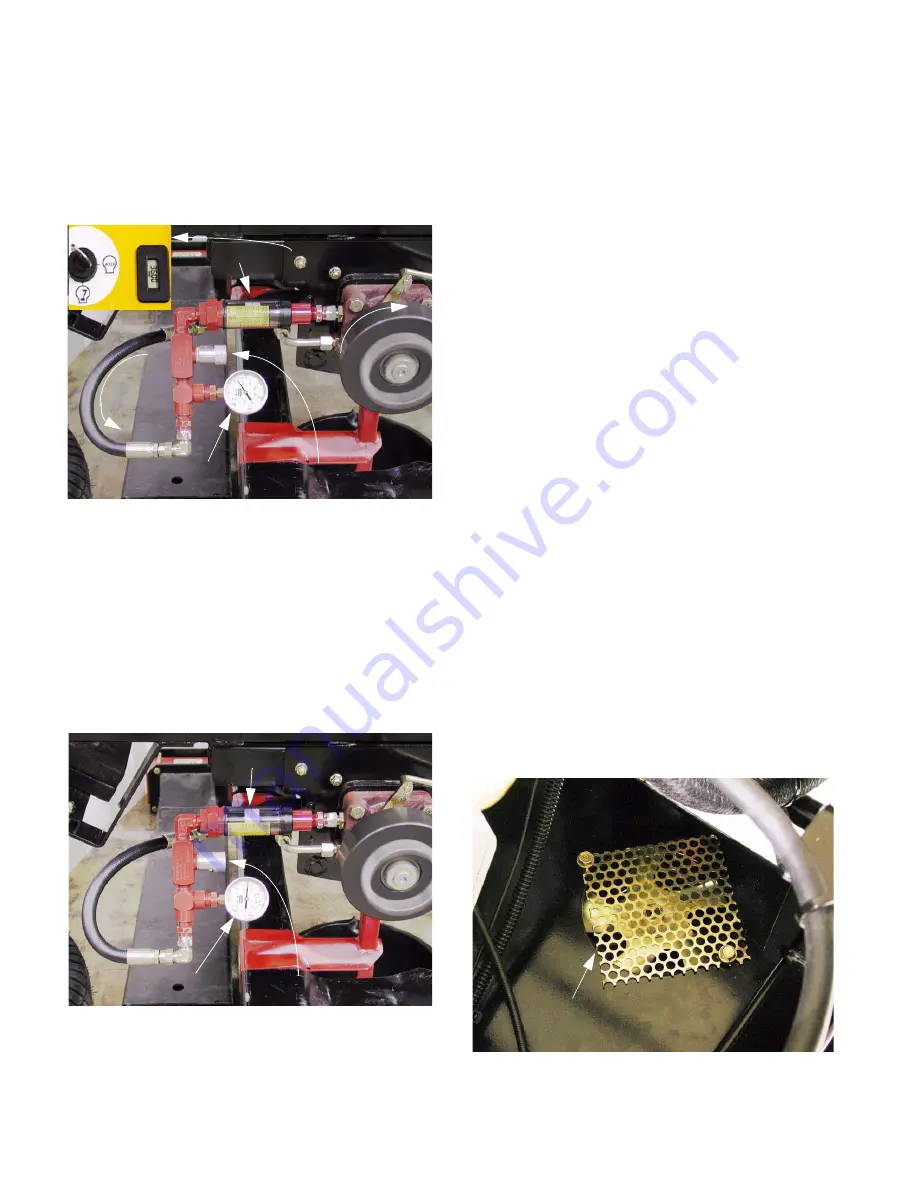
M48 Tank
6
4.23. When the fluid is between 160-210 deg. f.
(71-90 deg. c.) apply full forward drive pressure
to the lap bar with the engine running at full
speed (3600 RPM) while an assistant closes the
valve to the point where pressure reaches 300
PSI (21 Bar.). See Figure 4.23.
NOTE:
It may be necessary to over-shoot 300
PSI slightly, then open the valve to reduce pres-
sure to 300 PSI.
4.24. Take note of the reading on the flow meter por-
tion of the test kit when the pressure gauge
reads 300 PSI.
4.25. Continue closing the valve until the pressure
reading reaches 1,100 PS I (76 bar.). Take note
of the flow reading. See Figure 4.25.
4.26. Subtract the 1,100 PSI flow reading from the 300
PSI flow reading. The resulting figure is called
“
flow droop
”.
4.27. Interpretation: flow droop greater than 1.5 GPM
indicates a pump that is not performing as well
as it should.
NOTE:
A blocked filter may account for some
loss of performance.
4.28. Within the two year Cub Cadet Commercial war-
ranty period, replace the pump if it does not per-
form as specified and all other factors have been
eliminated.
4.29. If a hydro pump requires repair, refer to Hydro-
Gear publication “BLN-51337” for complete ser-
vice instructions.
4.30. If the hydro pump and all other factors are O.K.,
replace the hydro motor.
NOTE:
The hydro motor is not serviceable.
Replace it as a unit if it fails.
5.
REPLACING THE HYDRO PUMP
5.1.
If the cutting deck is currently on the unit,
remove it.
5.2.
Safely lift and support the rear of the tank.
5.3.
Remove the rear wheels using a 3/4” socket.
5.4.
Tilt the seat up, and disconnect the negative bat-
tery cable.
5.5.
Remove the screen that covers the opening over
the cooling fans on the hydro pump to be
removed using a 3/8” wrench. See Figure 5.5.
Figure 4.23
FLOW
300 PSI
10 GPM
BUILD PRESSURE
CLOSE VALVE TO
SPINNING
CONTROL
CONSOLE INSET:
3600 RPM
Figure 4.25
1100 PSI
9 GPM
VALVE CLOSED
FURTHER
Figure 5.5
REMOVE DEBRIS SCREEN