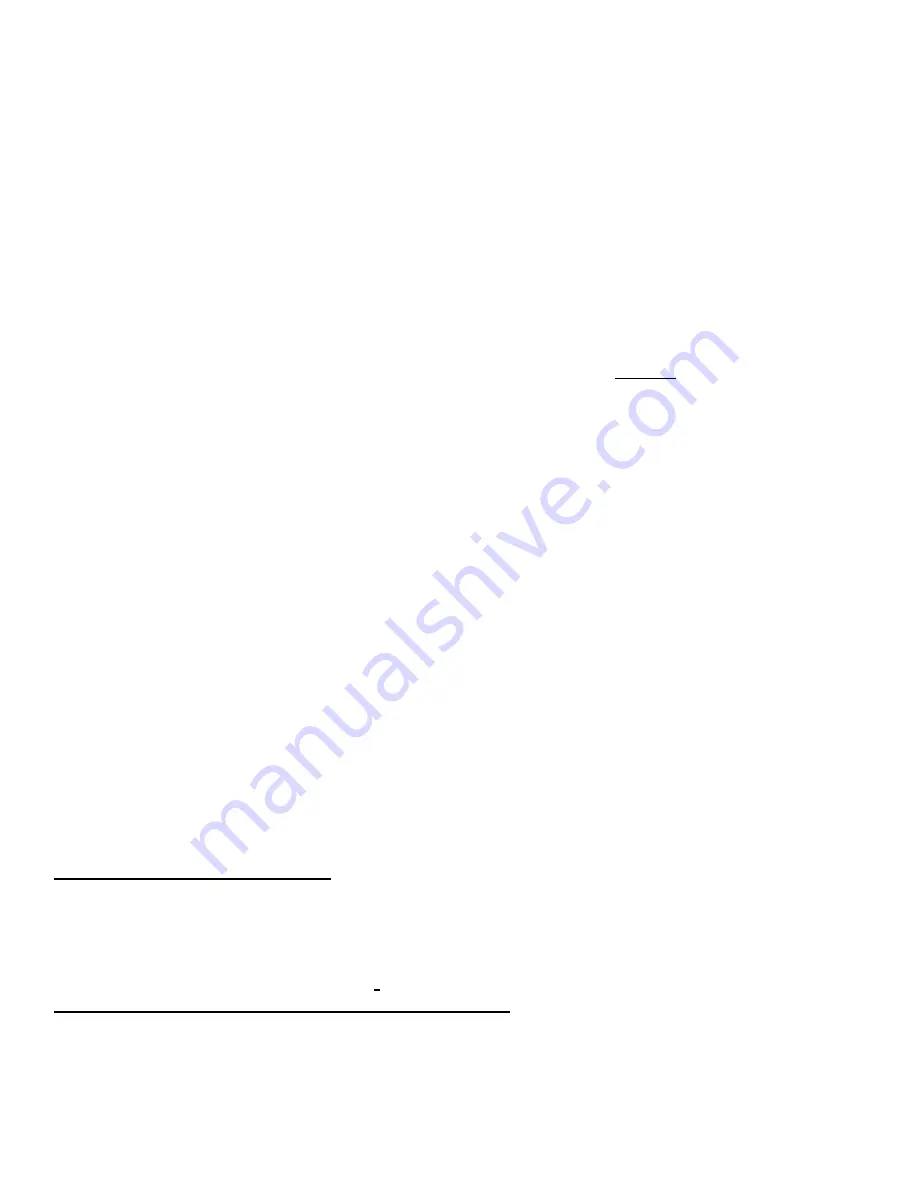
-15-
Cutting Wide Materials:
Wider mouldings can easily be cut on the D45’s because of our unique above-table saw head design. This
design allows for use of the bottom of the blade to cut, as well as the front of the blade. Of course, the blade
must be stopped before the flange (holding the blade on) makes contact with the moulding or material to be cut.
To stop the blade before it reaches the table (refer to Diagram”D” on Page No. 8);
1. Shut off air supply and disconnect power when making any adjustment to the machine.
2. Adjust Downstroke Bumper so that the blades will stop before the flange contacts material.
See “LENGTH OF STROKE ADJUSTMENT” on Page No. 10 for more details.
Cutting Smaller Materials:
When cutting larger production runs of smaller height and width materials, you will want to limit the upstroke
and downstroke of the machine to save time and motion.
1. Shut off air supply and disconnect power.
2. Lower saw heads so that saw blades are 1/2” above the material to be cut,
NEVER
cut below the height of
main blade guard, so the blades are exposed.
3. Adjust Upstop Clamp, No. 5 to contact Accessory Valve (3-Way Normally Open). This clamp limits the
upstroke of the cylinder on the piston rod. The saw heads will now return to this position every time when
completing a cycle.
4. Always provide a safe distance between the blade and the work to be cut. Re-adjust the finger guards
whenever the upstop clamp is changed. Make sure the blades are completely enclosed. See “LENGTH OF
STROKE ADJUSTMENT” on Page No. 10 for additional details.
Scrap:
The D45’s operate by making two 45
°
mitres at the same time. A “V” shaped piece is removed and falls into
the scrap chute located on the right hand side of the machine. A scrap box should be supplied to collect the scrap
pieces. To minimize scrap, make sure blades are set close together as shown in Diagram “C“ on Page No. 4. Also
see “BLADE INSTALLATION” on Page No. 4. Generally, you will loose between 3/8” (9mm) to ½” (13mm)
of scrap material.
Preventative Maintenance:
The D45AX and D45FX are relatively easy machines to operate and maintain. Below is a weekly check list of
general maintenance items. The best preventative maintenance advise is to
CLEAN THE MACHINE DAILY,
especially around the pivot points on the machine.
Lubrication and Adjustments of Bearings:
NO LUBRICATION OR ADJUSTMENTS ARE REQUIRED.
All CTD cut-off saws are assembled using
sealed, prelubricated ball bearings. The spindle and pivot assemblies are constructed using preloaded belleville
springs. These springs eliminate the need for adjustments of bearings and also greatly increase the life of
these bearings. All air cylinders are “lubed for life”.
Sound Levels:
During normal running of the machine without cutting the typical sound range will be between 60-85 db.
Due to the wide variety of blades available, CTD cannot warrant that maximum allowable OSHA sound limits
can be met--particularly during the cutting cycle.
Summary of Contents for D45AX
Page 20: ...20 D45AX D45FX SAW HEAD ASSEMBLIES...
Page 21: ...21 D45AX D45FX SAW HEAD ASSEMBLY PARTS LIST...
Page 22: ...D45AX BASE AND AIR SYSTEM ASSEMBLY 22...
Page 23: ...D45AX BLADE GUARD AND STAND ASSEMBLY 23...
Page 24: ...New Style D45AX Pivot Assy Used After March 2007 25...
Page 25: ...Air Stop Exploded View D45 Chip Breaker Exploded View 27...