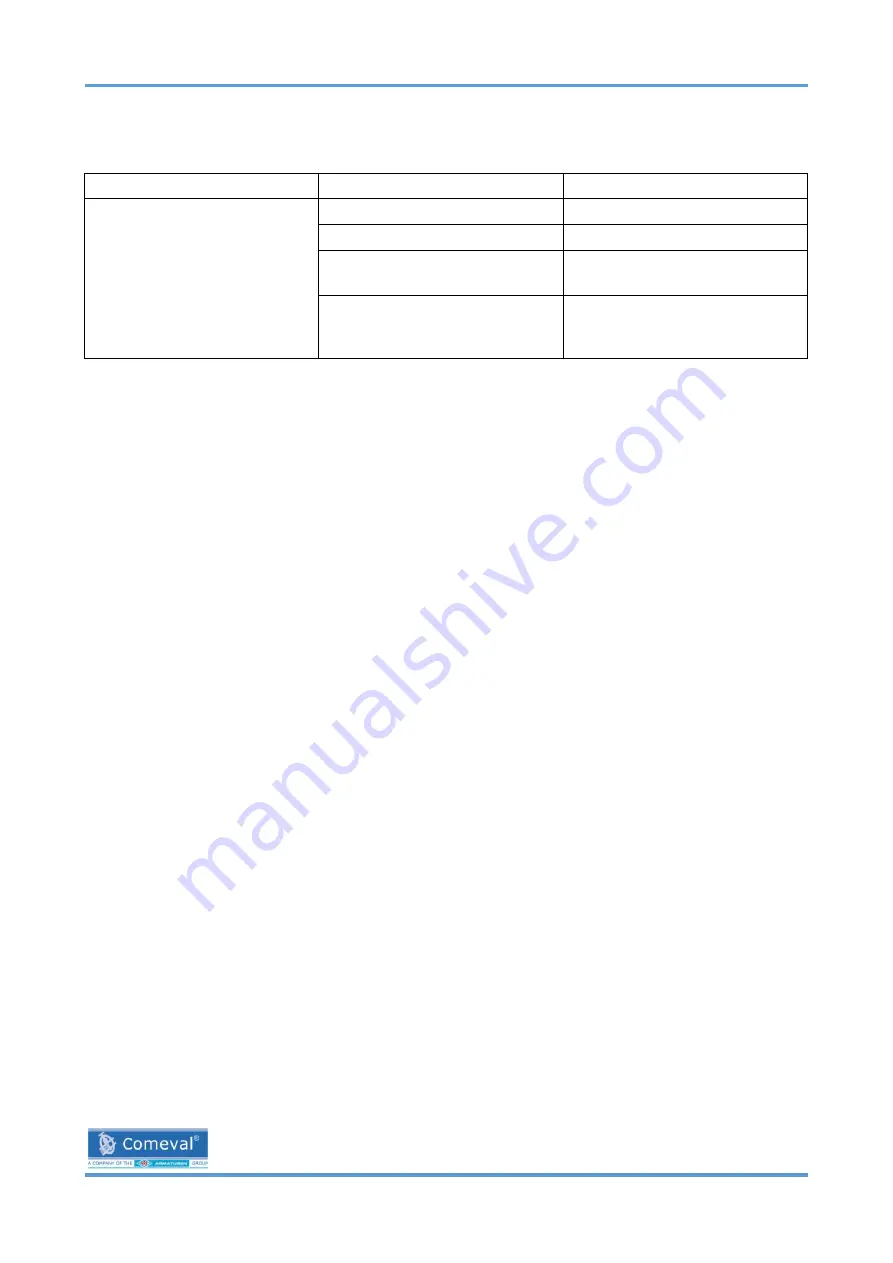
Direct acting PRV Mod. VRCD
9
For further information please consult us at: www.comeval.es
Troubleshooting
Condition
Possible Cause
Corrective Action
Valve leaks at flange joint.
Loose flange bolting.
Tighten flange bolting.
Blown flange gasket.
Replace flange gasket.
Miss-alignment or damage
to field piping and supports.
Adjust miss-alignment or
repair piping or supports.
Damaged flange face/s or
improper flange
connections.
Repair flange, replace
valve body or adjust flange
connections.