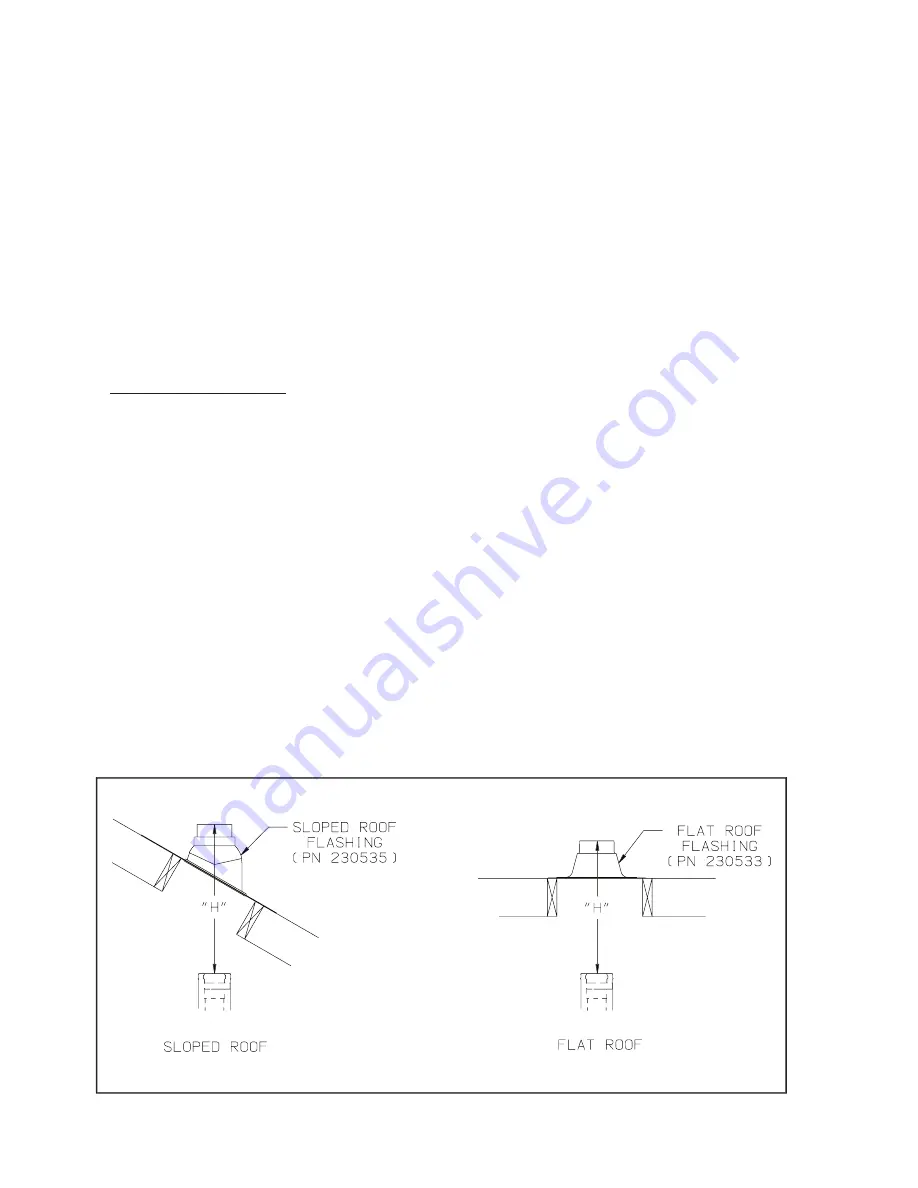
d) Complete the vent system inside the structure. The support elbow sits on the M10 x 35 screw as shown in Figure
7.34. Cut the Wall Penetration Section to the length required to connect the interior vent system to the Support Elbow
following the instructions on Page 26.
e) Remove the Support Elbow from the Lower Support Bracket and attach it to the Wall Penetration Section. Slip this
assembly through the Lower Support Bracket. Connect to the interior vent system.
f) Slide an Outer Joint Gasket over the male end of the Air Intake Section with the tapered edge of the gasket pointing
up. Attach the Air Intake Section to the Support Elbow. If necessary, the Air Intake Section can be shortened by
cutting the male end as described on page 26. After attaching the Air Intake Section to the Support Elbow, slide the
Outer Joint Gasket down over the joint between the two fi ttings to prevent rain infi ltration.
g) Attach the Wall bracket to the wall 0”-6” from the bottom edge of the intake bell (Figure 7.34). Use 1/4” screws (not
provided) to mount this bracket.
h) Slide the remaining Outer Joint Gasket over the male end of the Terminal Elbow. Attach the Terminal Elbow to the Air
Intake Section, pointing it away from the wall. Secure the Terminal Elbow to the Air Intake section with a single #10
x 1/2” sheet metal screw (Figure 7.34). Drill a 1/8 hole through both outer pipes to start this screw.
Use a drill stop
or other means to ensure that the drill bit does not penetrate more than 3/8” into the outer pipe. Do not use a
sheet metal screw longer than 1/2”.
Slide the Outer Joint Gasket down over the joint between the Terminal Elbow
and the Air Intake Section to prevent rain infi ltration.
i) Attach the Exhaust Terminal to the Terminal Elbow (Figure 7.34).
6) Vertical Terminal Installation - In addition to the vertical terminal, either a Flat Roof Flashing (PN 230533) or Sloped
Roof Flashing (PN 230535) is required for this installation.
a) Determine the center line of the terminal location on the roof. If the roof is fl at, cut a 5-1/2” diameter hole for the
terminal. If the roof is sloped, cut a hole large enough for the terminal to pass through the roof while remaining
plumb.
Caution: If the boiler is installed directly under the hole, cover it while cutting the hole to prevent saw
dust and other debris from falling into the boiler.
b) Install the roof fl ashing using standard practice for the roofi ng system on the structure.
c) If not already done, assemble the venting system inside the building. The last section of pipe needs to be on the same
center line as the terminal and within 19-1/4” of the top edge of the roof fl ashing (Figure 7.35a).
d) Measure distance “H” from the top edge of the storm collar to the end of the last fi tting as shown in Figure 7.35a.
e) Add 1” to distance “H”. Carefully mark this length on the pipe as shown in Figure 7.35b.
f) Cut the
outer pipe only
at the point marked in Step (e) using aviation shears, a hacksaw, or an abrasive wheel cutter.
Be careful to cut the pipe square. De-burr the cut end with a fi le or emery cloth.
g) Place a mark on the aluminum inner pipe 3/8” beyond the end of the outer pipe (Figure 7.35b). Use a fi ne tooth
hacksaw to cut the aluminum pipe and be careful to cut the pipe square. De-burr the cut edge of the aluminum pipe
with a fi le or emery cloth.
h) Make a mark on the terminal section 1” from the cut end of the outer pipe as shown in Figure 7.35b.
i) Slip the terminal section through the roof from the outside. Push into the last section of vent pipe until the mark
made in Step (h) is not longer visible. Secure the terminal to the last piece of pipe with three #10 x 1/2” sheet metal
screws. Drill a 1/8” hole through both outer pipes to start these screws.
Use a drill stop or other means to ensure
that the drill bit does not penetrate more than 3/8” into the outer pipe. Do not use a sheet metal screw longer
than 1/2”.
j) Secure the terminal section to the inside of the roof structure using the mounting bracket provided with the terminal
(Figure 7.35c).
FIGURE 7.35a: DIMENSION “H”
32