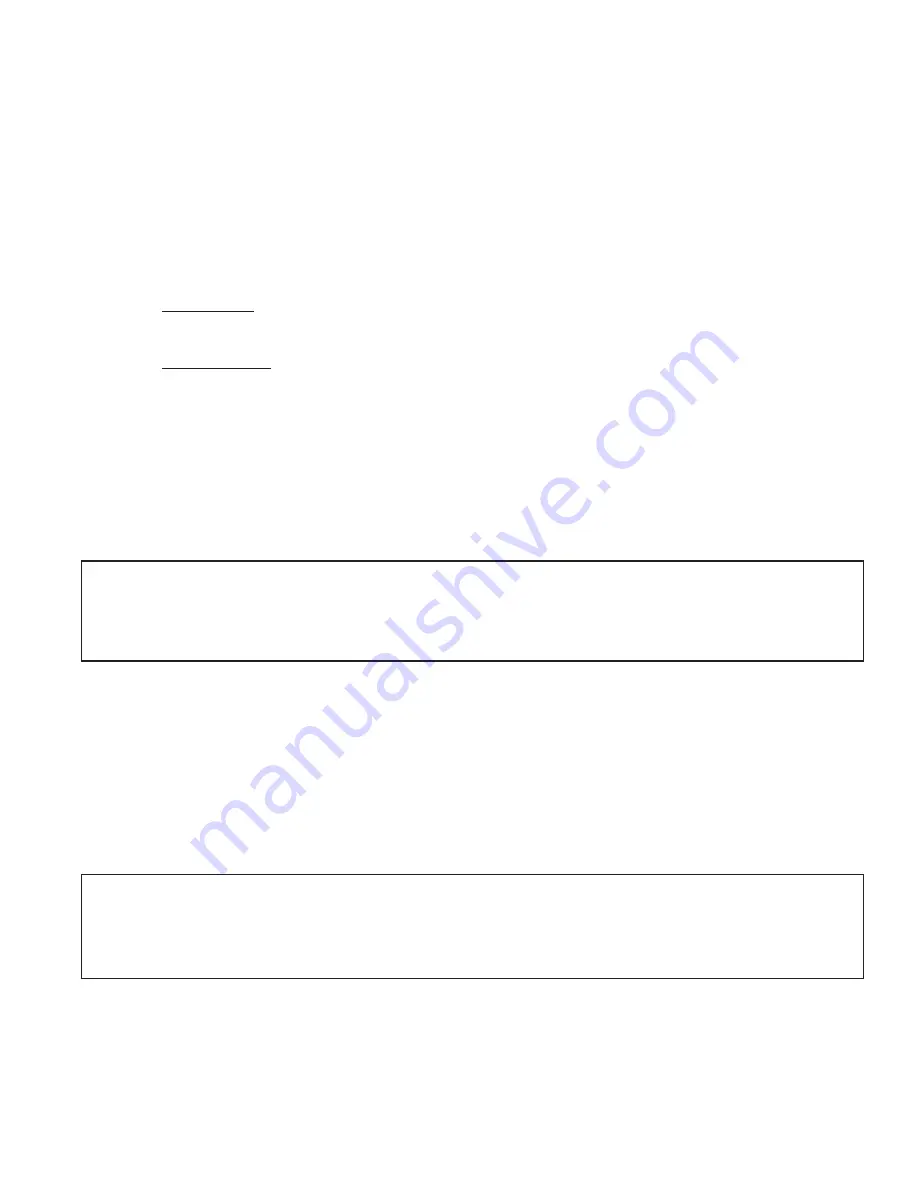
29
XI Service and Maintenance
The following routine maintenance should be performed on an annual basis:
1)
Turn off electrical power and gas supply to the boiler
2)
Inspect the flue passages for signs of blockage. If there is any carbon in the combustion chamber or the flue passages,
clean the heat exchanger before proceeding further. See the cleaning procedure below.
3)
Remove any debris found in the combustion chamber, being careful not to disturb combustion chamber insulation.
4)
Remove all burners, noting the location of the pilot main burner. If burners show signs of deterioration, they should be
replaced (some discoloration around the burner ports is normal). Clean the burners by first brushing the ports with a soft
bristle brush and then vacuuming out any debris through the venturi opening.
5)
Inspect the pilot assembly:
•
Standing Pilots - Check the thermocouple for deterioration (some discoloration of the thermocouple is normal). If
any deterioration is present, replace the thermocouple. Inspect the pilot assembly for deposits and deterioration.
Clean or replace the pilot assembly as necessary.
•
Intermittent Pilots - Clean any deposits found on the electrode and grounding strap. The ideal gap between the
electrode and the ground strap is 1/8”. Inspect the porcelain for cracks or other deterioration. Replace pilot
assembly if deterioration is found.
6)
Inspect the combustion chamber insulation for deterioration.
7)
(Intermittent Pilot Boilers) - Inspect the ignition cable insulation for cracks or other deterioration. If deterioration is
found, replace cable.
8)
Reinstall burners, being careful to put the pilot main burner in its original location.
9)
Inspect all boiler wiring for loose connections or deterioration.
10) Inspect the vent system:
•
Make sure that both the vent system is free of obstructions.
•
Make sure that all vent system supports are intact.
•
Inspect joints for signs of condensate or flue gas leakage.
•
Inspect venting components for corrosion or other deterioration. Replace any defective vent components.
11) Inspect the boiler and hydronic system for leaks.
12) Place the boiler back in operation using the procedure outlined in “Start-up”. Check the pilot line and any other gas
piping disturbed during the inspection process for leaks.
CAUTION
LABEL ALL WIRES PRIOR TO DISCONNECTION WHEN SERVICING CONTROLS. WIRING ERRORS CAN
CAUSE IMPROPER AND DANGEROUS OPERATION. VERIFY PROPER OPERATION AFTER SERVICING
CAUTION
WATER LEAKS CAN CAUSE SEVERE CORROSION DAMAGE TO THE BOILER OR OTHER SYSTEM COMPO-
NENTS. REPAIR ANY LEAKS FOUND IMMEDIATELY
27
Summary of Contents for AWI037
Page 2: ...2 INSIDE FRONT COVER LEAVE BLANK ...
Page 4: ...4 2 FIGURE1B LEFTPIPED CONFIGURATION FIGURE1C TOPPIPED T AWIORT TWI CONFIGURATION ...
Page 28: ...28 FIGURE24 GASVALVEDETAIL STANDINGPILOT FIGURE25 GASVALVEDETAIL INTERMITTENTIGNITION 26 ...
Page 37: ...37 35 Base Block Hood ...
Page 39: ...39 37 50mm BURNER COMPONENTS 1 BURNER COMPONENTS ...
Page 41: ...41 39 Jacket Components ...