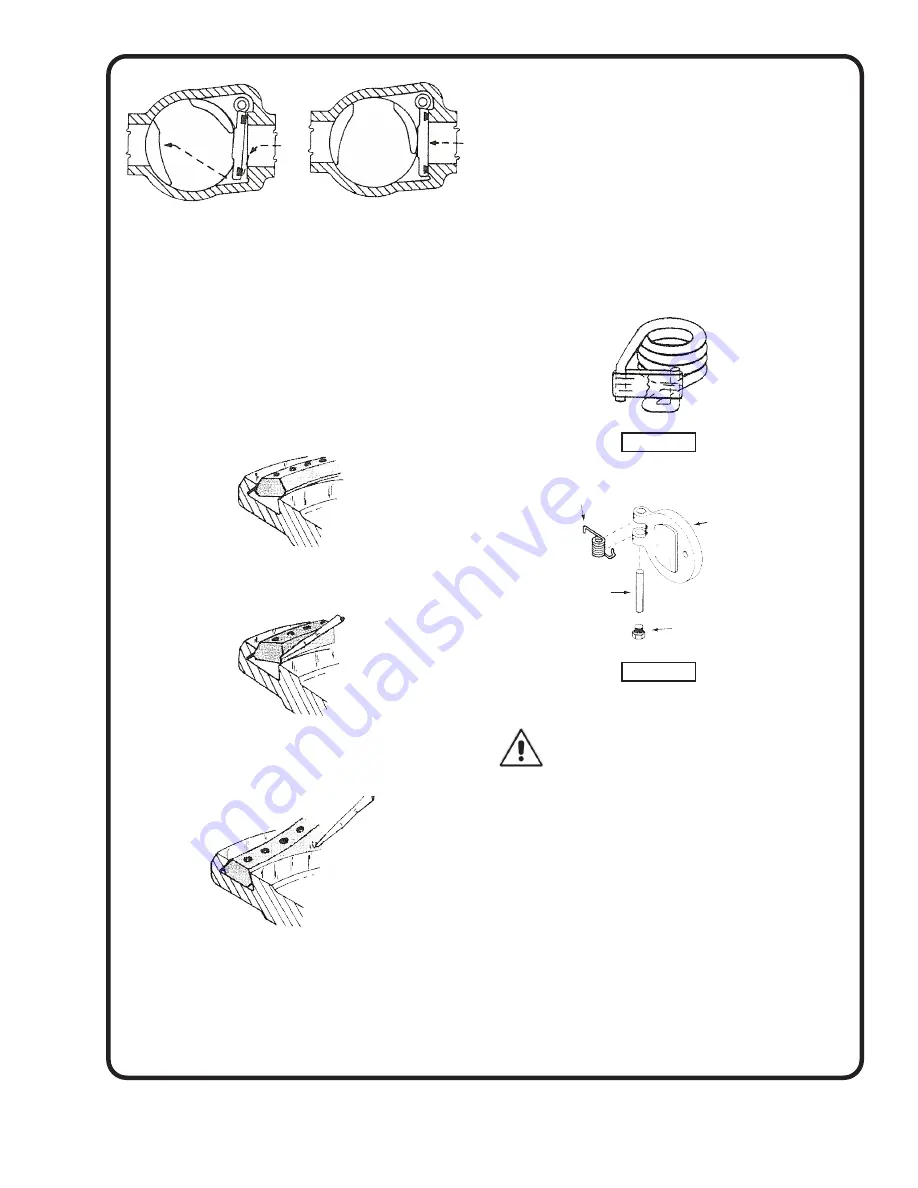
7
REPAIR CLAPPER SEAL:
HVAC TDV valves are equipped with Buna-N clapper
seals. If the clapper seal is damaged, they can be
replaced by removing the clapper and installing a new
seal (see steps 1-3 below).
Step 1
Place the outer edge of the seal into the clapper groove
as shown.
Step 2
Using a blunt screwdriver, force the inside lower edge of
the seal into the clapper groove.
Step 3
As you work the seal in, maintain force on the portion
of the seal that has been installed. This will prevent
elongation and excessive build-up of closing portion.
REPLACEMENT PROCEDURE:
1.
Position clapper firmly against the seat face.
2.
Pre-load spring and bind using filament tape (see
Figure 4a)
3. Take the clapper pin with the extension screw and
insert the pin into the spring and support hangers (see
Figure 4b)
4.
When holding the clapper firmly against the seat, the
clapper pin must move freely into position.
5. Remove the extension screw, replace the clapper pin
plug, and cut the filament tape to free the spring.
6. Check the clapper for free movement by opening and
closing the clapper by hand.
7. If movement is free, complete the valve assembly.
6. WIRING
WARNING: DO NOT START PUMP UNTIL IT
HAS BEEN FILLED WITH WATER.
1. Motor wiring should conform to national and local
electrical codes.
2. Use wire of adequate size to prevent voltage drop.
3. Pump should be on a branch or separate circuit,
fused or circuit breaker, protected, with a manual
disconnect.
4. Connect the electrical supply from the switch to the
motor terminals, following the wiring diagram on
the motor nameplate or terminal cover plate.
NOTE:
be sure that the connections to the motor
terminals correspond with the voltage to be
applied. (See Chart)
Check wiring and fuse charts before connecting wires to
service line. Make sure the voltage and frequency of the
electrical current supply agrees with that stamped on the
motor nameplate. If in doubt, check with power company.
Closed Position
As the plug is rotated
toward the closed position,
the downstream part
closes first. This equalizes
the Pressure so the
clapper closes with little
resistance.
Positive Seal Closure
Final closing is
accomplished by the plug
camming against the back
of the clapper.
Figure 4a
Spring
Figure 4b
Clapper Pin Plug
Clapper
Clapper Pin