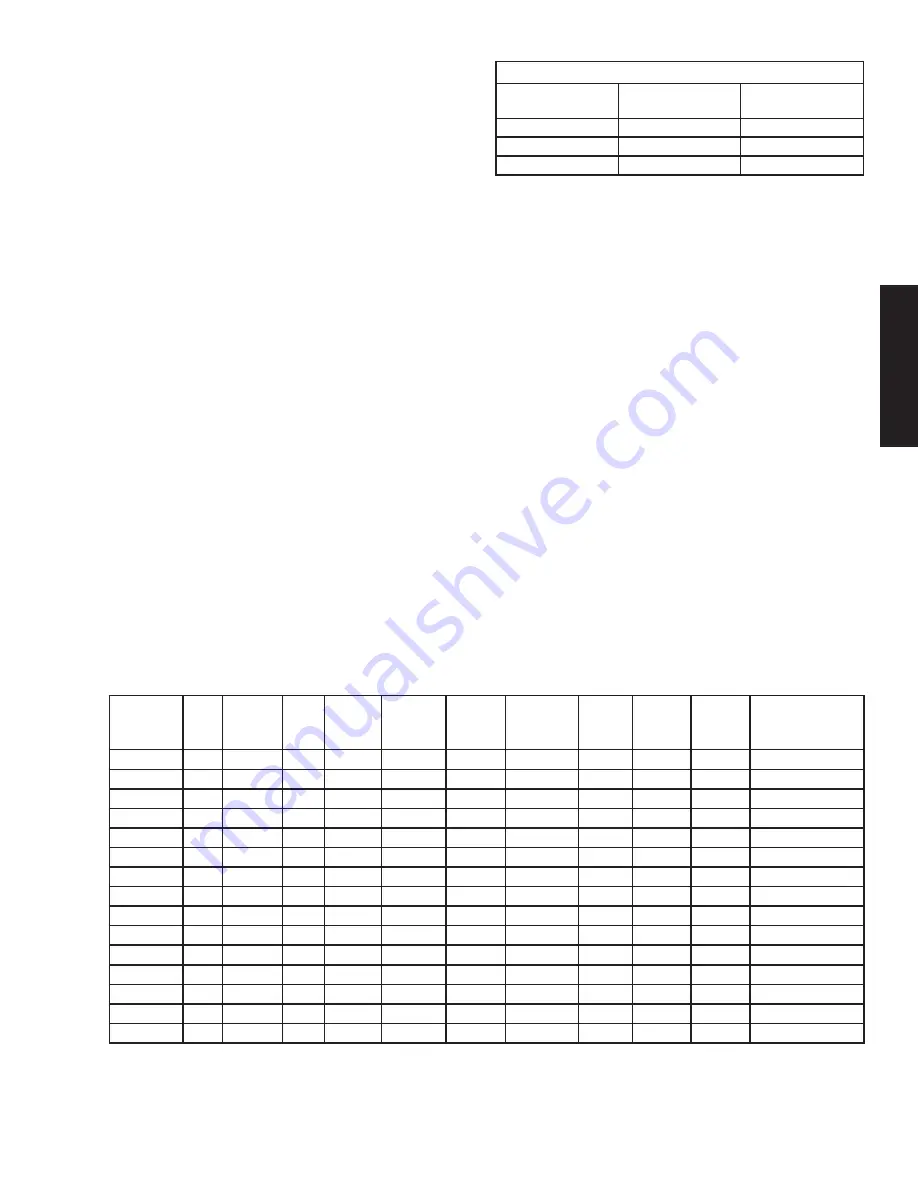
7
C-3.2) Overload Protection:
C-3.2-1) Three Phase
(optional) - The normally closed (N/C)
thermal sensor is embedded in the motor windings and will
detect excessive heat in the event an overload condition
occurs. The thermal sensor will trip when the windings
become too hot and will automatically reset itself when the
pump motor cools to a safe temperature. It is recommended
that the thermal sensor be connected in series to an alarm
device to alert the operator of an over-temperature condition
and/or the motor starter coil to stop the pump. In the event
of an over-temperature, the source of this condition should
be determined and rectifi ed immediately. Thermal protection
shall not be used as a motor overload device. A separate
motor overload device must be provided in accordance with
NEC codes.
DO NOT LET THE PUMP CYCLE OR RUN IF
AN OVERLOAD CONDITION OCCURS !
C-3.2-2) Single Phase
(standard) - The type of in-winding
overload protector used is referred to as an inherent
overheating protector and operates on the combined effect
of temperature and current. This means that the overload
protector will trip out and shut the pump off if the windings
become too hot, or the load current passing through them
becomes too high. It will then automatically reset and start
the pump after the motor cools to a safe temperature. In the
event of an overload, the source of this condition should be
determined and rectifi ed immediately.
DO NOT LET THE
PUMP CYCLE OR RUN IF AN OVERLOAD CONDITION
OCCURS !
If current through the temperature sensor exceeds the values
listed, an intermediate control circuit relay must be used to
reduce the current or the sensor will not work properly.
TEMPERATURE SENSOR ELECTRICAL RATINGS
Volts
Continuous
Amperes
Inrush
Amperes
110-120
3.00
30.0
220-240
1.50
15.0
440-480
0.75
7.5
C-3.3) Wire Size:
Consult a qualifi ed electrician for proper wire size if additional
power cable length is required. See table for electrical
information.
SECTION: D START-UP OPERATION
D-1) Check Voltage and Phase:
Before operating pump, compare the voltage and phase
information stamped on the pump identifi cation plate to the
available power.
D-2) Check Pump Rotation:
Before putting pump into service for the fi rst time, the motor
rotation must be checked. Improper motor rotation can
result in poor pump performance and can damage the motor
and/or pump. To check the rotation, suspend the pump
freely, momentarily apply power and observe the “kickback”.
“Kickback” should always be in a counter-clockwise direction
as viewed from the top of the pump motor housing.
D-2.1) Incorrect Rotation for Three-Phase Pumps:
In the event that the rotation is incorrect for a three-phase
installation, interchange any two power cable leads at the
control box.
DO NOT
change leads in the cable housing
in the motor. Recheck the “kickback” rotation again by
momentarily applying power.
MODEL
NO
HP VOLT/
Ph
Hz
RPM
(Nom)
NEMA
START
CODE
FULL
LOAD
AMPS
LOCKED
ROTOR
AMPS
CORD
SIZE
CORD
TYPE
CORD
O.D.
WINDING
RESISTANCE
MAIN--START
SED50
0.5
115/1
60
1750
D
11.6
18.4
14/3C
SO
0.560
1.44 -- 16.36
SED52
0.5
230/1
60
1750
E
5.8
10.5
14/3C
SO
0.560
2.88 -- 32.72
SED55
0.5
230/3
60
1750
G
3.4
7.8
14/4C
SO
0.600
14.20
SED56
0.5
460/3
60
1750
G
1.7
3.9
14/4C
SO
0.600
56.7
SED73
0.75
230/3
60
1750
G
4.0
11.6
14/4C
SO
0.600
9.67
SED74
0.75
460/3
60
1750
G
2.0
5.8
14/4C
SO
0.560
38.70
SED75
0.75
230/1
60
1750
C
7.0
12.5
14/3C
SO
0.560
2.08 -- 33.84
SEDH100
1.0
230/1
60
3450
B
8.2
13.8
14/3C
SO
0.600
1.93 -- 8.80
SEDH103
1.0
230/3
60
3450
K
5.4
21.2
14/3C
SO
0.600
4.57
SEDH104
1.0
460/3
60
3450
K
2.8
10.7
14/4C
SO
0.600
17.50
4NX07
0.5
115/1
60
1750
D
11.6
18.4
14/3C
SO
0.560
1.44 -- 16.36
4NX08
0.5
230/1
60
1750
E
5.8
10.5
14/3C
SO
0.560
2.08 -- 33.84
4NX09
1.0
230/1
60
3450
B
8.2
13.8
14/3C
SO
0.560
1.93 -- 8.80
4NX10
1.0
230/3
60
3450
K
5.4
21.2
14/3C
SO
0.600
4.57
Pump rated for operation at ± 10% voltage at motor.
Winding Resistance ± 5%, measured from terminal block.
Temperature sensor cord for 3 phase models is 14/2 SOW, 0.530 (13.5) ± .02 O.D.
E
N
G
L
I
S
H
Summary of Contents for PROSSER 4NX07 Series
Page 14: ...14 FIGURE 8 Series SED 4NX07 4NX08 E N G L I S H ...
Page 15: ...15 FIGURE 9 Series SEDH 4NX09 4NX10 E N G L I S H ...
Page 16: ...16 FIGURE 10 SEDH Series 4NX09 4NX10 SED Series 4NX07 4NX08 Series SED SEDH 4NX E N G L I S H ...
Page 35: ...15 SP E S P A Ñ O L FIGURA 8 Serie SED 4NX07 4NX08 ...
Page 36: ...16 SP E S P A Ñ O L FIGURA 9 Serie SEDH 4NX09 4NX10 ...
Page 42: ...E S P A Ñ O L ...