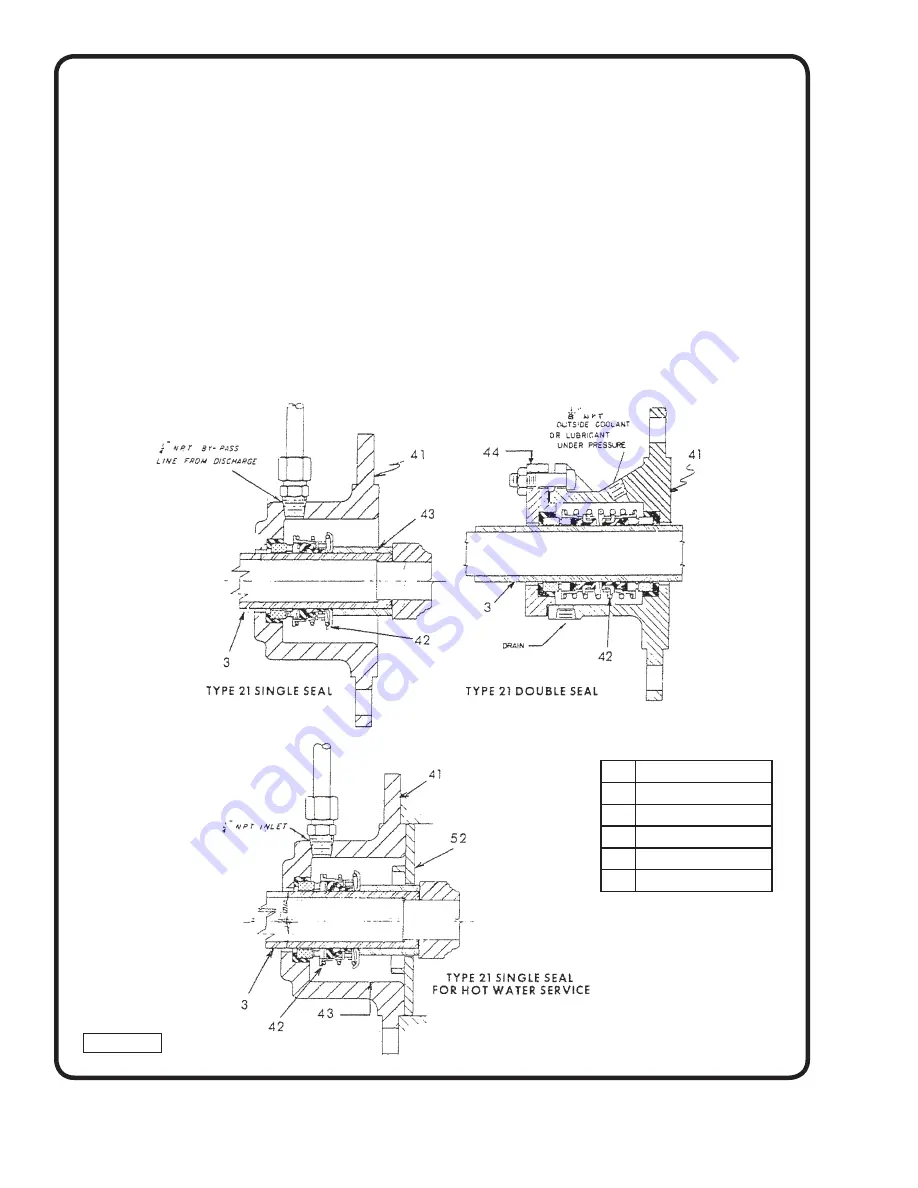
8
5. REPLACE DOUBLE MECHANICAL SEAL
- Seals are
available as a complete assembly only.
a. The double mechanical seal as shown is used
when pumping abrasives or nonlubricating liquids
or with liquids at excessive temperatures.
A sealing liquid at 15 to 20 pounds above suction
must be circulated through the seal chamber.
Clear water under pressure can be used in most
applications as a sealing liquid for lubrication and
cooling. If the pressure at the inner seal face is
under 25 pounds and the temperature is under
boiling point of the liquid being pumped, the seal
chamber can be fi lled with grease. See
“Lubrication”, a spring loaded compression type
grease cup should be installed to maintain
pressure in the seal chamber.
b. Special precautions must be observed when
handling a mechanical seal. DO NOT drop the
seal face carbons or fl oating seats nor scratch
the lapped faces for these pieces.
c. To remove the seal assembly, dismantle the
liquid end of the pump as described in
“Disassembly of Liquid End”, then unscrew gland
bolts and nuts. Remove seal head casting (41)
from the motor support, exposing the seal
assembly. Grasp the seal fi rmly by hand and
twist it on the shaft to break the seal between
the bellows and the shaft. The seal can now be
pulled from the sleeve. Also remove the seal
gland (44) from the shaft. Place gland gasket in
water. Press seal seats from the seal gland (44)
and seal head (41).
Figure 4
3
Shaft Sleeve
33
Shaft Sleeve
41
Seal Head
42
Seal Assembly
44
Seal Gland
52
Insert Choker Ring