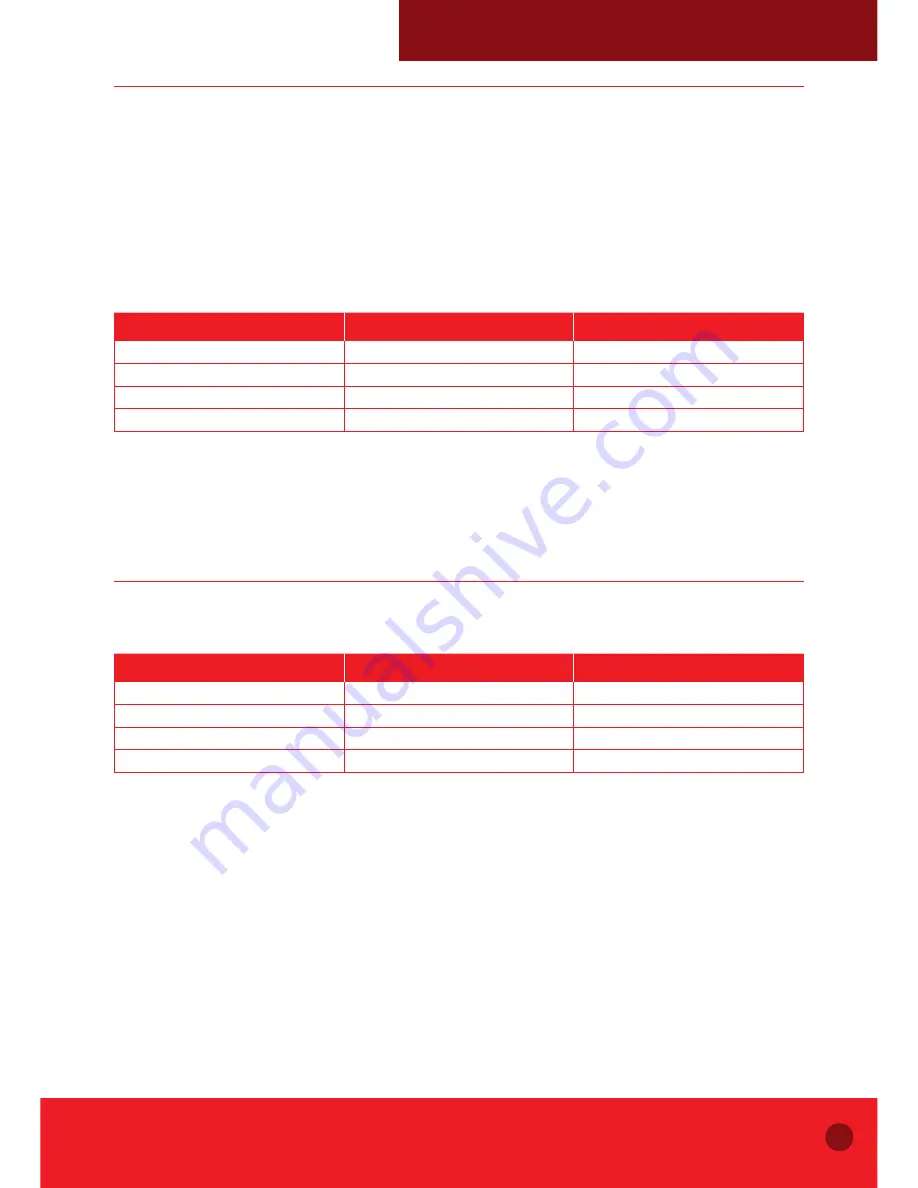
7
THERMOSTATIC MIXING VALVES: D1088 & D1089
INSTALLATION, OPERATING AND MAINTENANCE INSTRUCTIONS
TMV2
The valves covered by these instructions have been specifically designed and manufactured as
being in compliance with BS EN1287 and BS EN1111. It has been independently tested and
approved as a TYPE 2 valve under TMV2 scheme for use in domestic situations.
LIMITS OF USE
The D1088 & D1089 have been approved for use on the following designated systems.
Code
Operating Pressure
Application
HP-S, LP-S
High Pressure
Shower Temperature 41ºC
HP-W, LP-W
High Pressure
Washbasin Temperature 41ºC
HP-B, LP-B
High Pressure
Bidet Temperature 38ºC
HP-T44
High Pressure
Bath Fill Temperature 44ºC
Table 5 - Mixed Water Temperature
Note 1: HP: High Pressure LP: Low Pressure
Note 2: 46°C is the maximum permissible mixed water temperature from the bath tap. The maximum temperature
takes account of the allowable temperature tolerances inherent in thermostatic mixing valves and temperature losses
in metal baths. 46°C is not a safe bathing temperature for adults or children.
Note 3: The British Burns Association recommends 37 to 37.5°C as a comfortable bathing temperature for children.
In premises covered by the Care Standards Act 2000, the maximum mixed water outlet temperature is 43°C.
CONDITIONS OF USE
Operating Pressure Range
High Pressure
Low Pressure
Maximum Static Pressure
10 bar
10 bar
Flow Pressure - Hot & Cold
0.5 bar to 5.0 bar
0.1 bar to 1.0 bar
Hot Supply Temperature
55 to 65ºC
55 to 65ºC
Cold Supply Temperature
≤
25°C
≤
25°C
Table 6 - Normal Conditions of Use for Type 2 Valves
Note 1: Valves operating outside table 6’s conditions cannot be guarantees by the Scheme to operate as
Type 2 valves.
Note 2: Valves approved for designation of use H.P only, must state: - If a water supply is fed by gravity then the
supply pressure should be verified to ensure the conditions of use are appropriate for the valve.
Note 3: Valves approved for designation of use LP Tub applications that only achieve the minimum flow rate
requirement at a supply pressure of 0.2 bar must indicate that the minimum supply pressure for LP Tub application
is 0.2 bar.