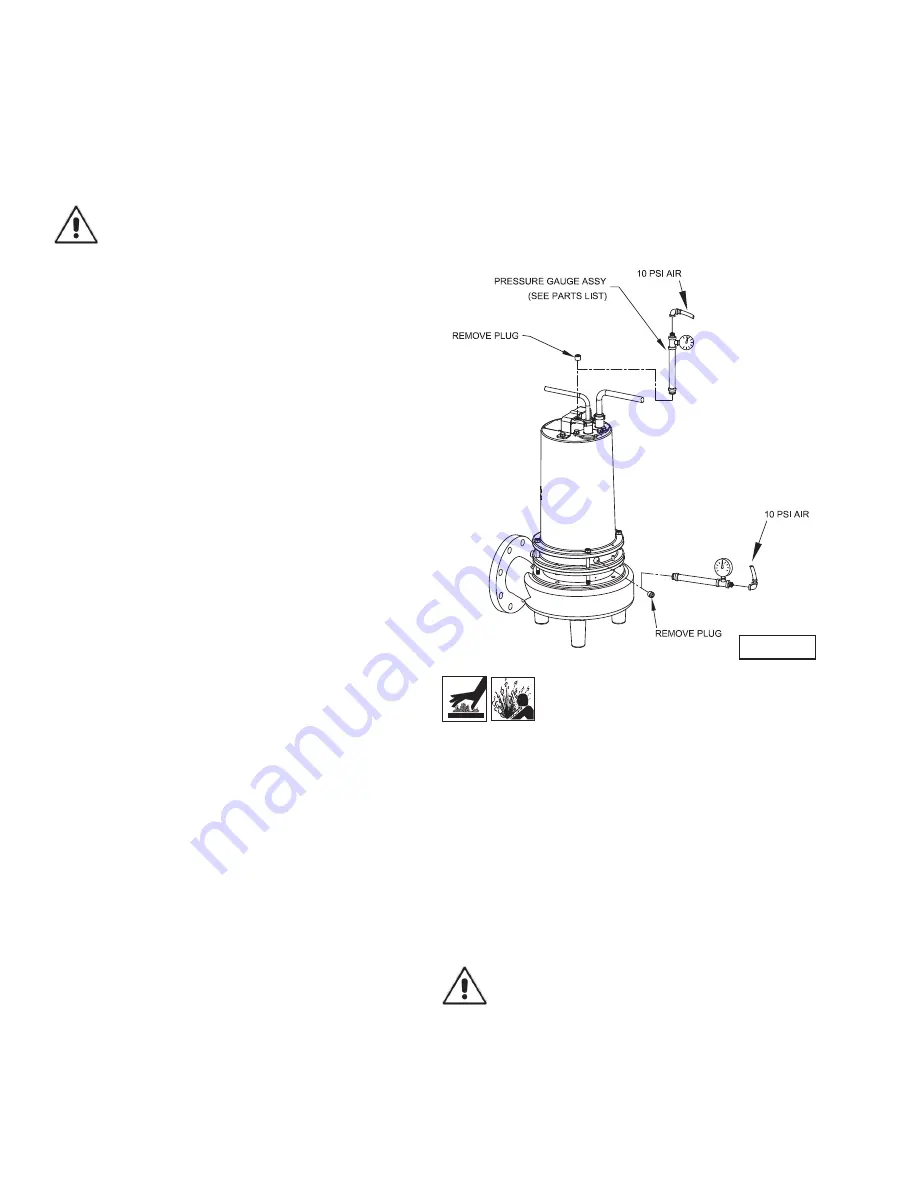
8
SECTION E: PREVENTATIVE MAINTENANCE
As the motor is oil filled, no lubrication or other maintenance
is required, and generally CP&S pumps will give very reliable
service and can be expected to operate for years on normal
sewage pumping without failing. However as with any
mechanical piece of equipment a preventive maintenance
program is recommended and suggested to include the
following checks:
WARNING ! - Pressure builds up due to heat.
1) Inspect motor chamber for oil level and contamination and
repair as required per section F-1.
2) Inspect impeller and body for excessive build-up or clogging
and repair as required per section F-2.
3) Inspect motor and bearings and replace as required per
section F-3.
4) Inspect seal for wear or leakage and repair as required per
section F-4.
SECTION F: SERVICE AND REPAIR
NOTE: All item numbers in ( ) refer to Figures 12, 13, 14
& 15.
F-1) Lubrication:
Anytime the pump is removed from operation, the cooling oil
in the motor housing (2) should be checked visually for oil
level and contamination.
F-1.1) Checking Oil:
Motor Housing -
To check oil, set unit upright. Remove pipe
plug (5) from motor housing (2). With a flashlight, visually
inspect the oil in the motor housing (2) to make sure it is
clean and clear, light amber in color and free from suspended
particles. Milky white oil indicates the presence of water. Oil
level should be just above the motor when pump is in a vertical
position.
F-1.2) Testing Oil:
1. Place pump on it’s side, remove pipe plug (5), from motor
housing (2) and drain oil into a clean, dry container.
2. Check oil for contamination using an oil tester with a range
to 30 Kilovolts breakdown.
3. If oil is found to be clean and uncontaminated (measure
above 15 KV. breakdown), refill the motor housing as per
section F-1.4.
4. If oil is found to be dirty or contaminated (or measures
below 15 KV. breakdown), the the pump must be carefully
inspected for leaks at the shaft seal (46), cable assemblies
(52) and (53), square ring (42) and pipe plug (5)
before refilling with oil. To locate the leak, perform
a pressure test as per section F-1.3. After leak is repaired,
refill with new oil as per section F-1.4.
F-1.3) Pressure Test:
Pumps that have had the oil drained from the Motor
Housing -
Apply pipe sealant to pressure gauge assembly
and tighten into pipe plug hole (See Figure 2). Pressurize
motor housing to 10 P.S.I. Use soap solution around the
sealed areas and inspect joints for “air bubbles”. If, after
five minutes, the pressure is still holding constant, and no
“bubbles” are observed, slowly bleed the pressure and
remove the gauge assembly. Replace oil as described in
section F-1.4. If the pressure does not hold, then the leak
must be located and repaired.
Pumps that have NOT had the oil drained from the Motor
Housing -
The pressure test may be done with the oil at its
normal level. Remove pipe plug (5) from motor housing (2).
Apply pipe sealant to pressure gauge assembly and tighten
into hole (see Figure 2). Pressurize motor housing to 10 P.S.I.
Use soap solution around the sealed areas above the oil level
and inspect joints for “air bubbles”. For sealed areas below
the oil level, leaks will seep oil.
If, after five minutes, the pressure is still holding constant,
and no “bubbles”/oil seepage is observed, slowly bleed the
pressure and remove the gauge assembly. If the pressure
does not hold, then the leak must be located and repaired.
CAUTION ! - Pressure builds up extremely
fast, increase pressure by “TAPPING” air
nozzle. Too much pressure will damage
seal. DO NOT exceed 10 P.S.I.
Seal Chamber -
Set unit on its side with fill plug (5)
downward, remove plug (5) and drain all oil from seal
chamber. Apply pipe sealant to pressure gauge assembly
and tighten into hole in bearing bracket (21). Pressurize seal
chamber to 10 P.S.I. and check for leaks as outlined above.
F-1.4) Replacing Oil:
Motor Housing-
Set unit upright and refill with new cooling
oil as per Table 1 (see parts list for amount). Fill to just above
motor as an air space must remain in the top of the motor
housing to compensate for oil expansion (see Figure 2, 12 or
14). Apply pipe thread compound to threads of pipe plug (5)
then assemble to motor housing (2).
IMPORTANT! - For single phase units, oil level
should be below capacitor.
Seal Chamber -
Set unit on its side, with plug (5) upward,
and refill with new oil as per Table 1 (see parts list for
amount). Apply pipe thread compound to threads of pipe plug
(5) and assemble to bearing bracket (21).
FIGURE 2