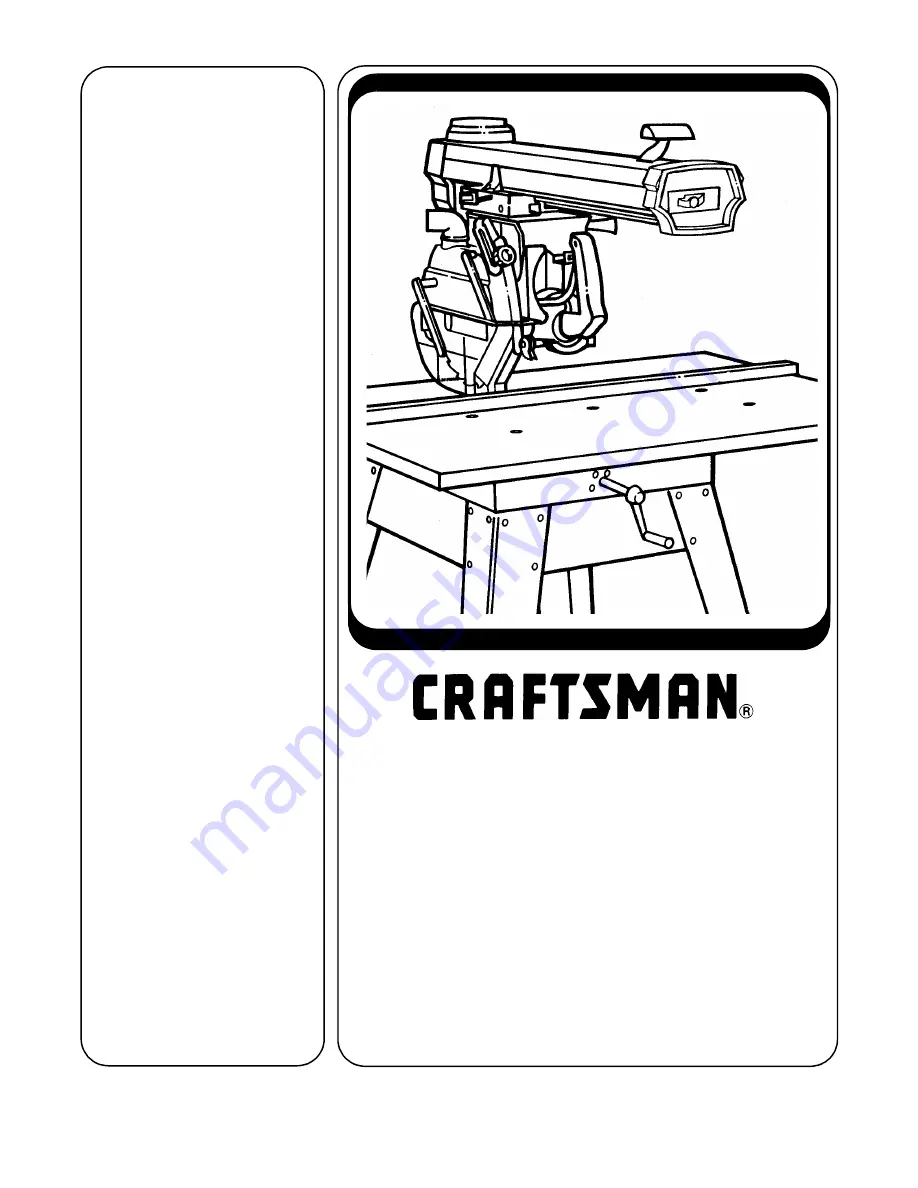
FOR YOUR
SAFETY:
READ ALL
INSTRUCTIONS
CAREFULLY
Save This Manual
For Future Reference
owner’s
manual
Part No. SP5984
Printed in U.S.A.
10-INCH RADIAL SAW
GUARD KIT
• assembly
• operating
• repair parts
MODEL NO.
509347
509347 FITS THE
FOLLOWING RADIAL
SAWS:
113.19930, 113.197731,
113.197732, 113.199350