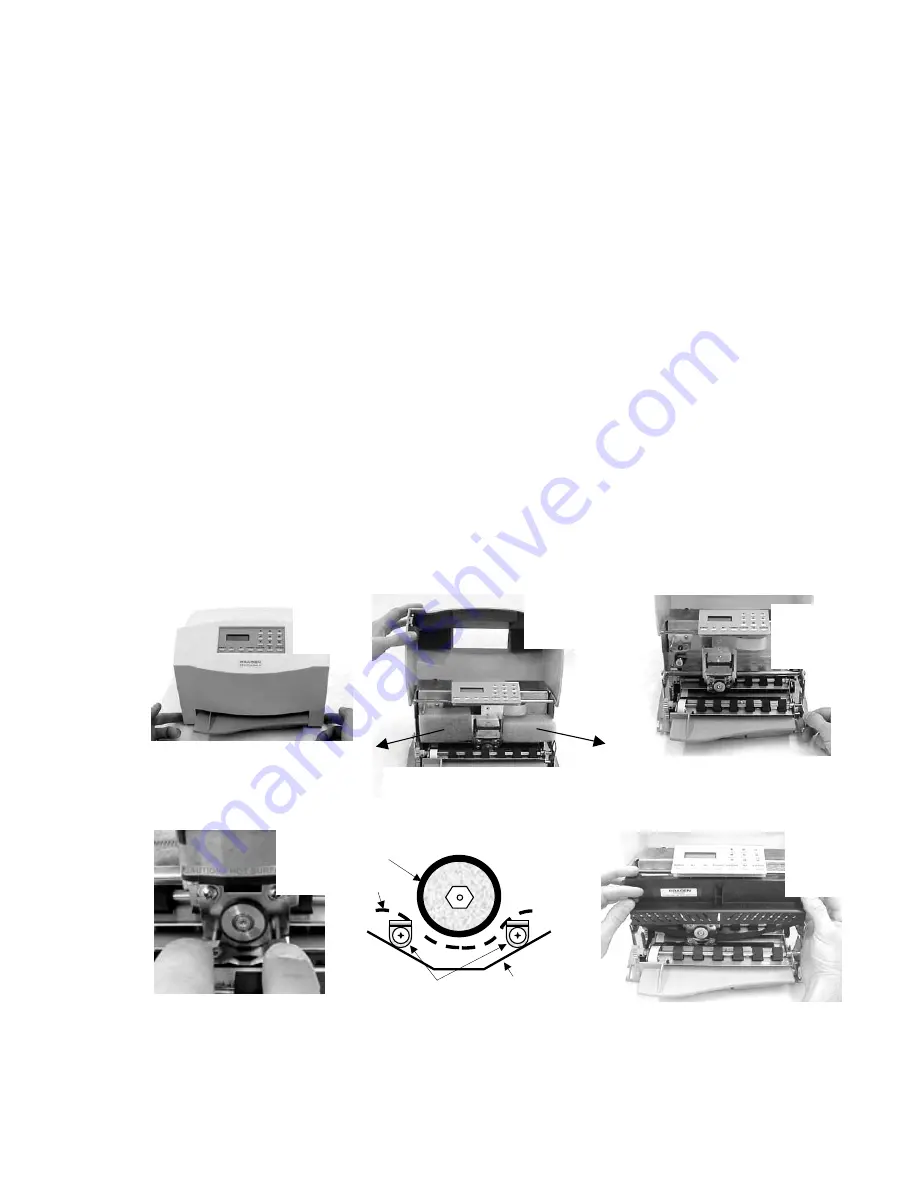
2.0 INSTALLATION
2.1 Installation Procedure
1. Read 3.1 to 3.5.2 on Operation and Configuration
.
2. Press the cabinet latches on the lower front cabinet sides and rotate the cabinet upwards.
3. Remove the foam blocks on each side of the carriage.
4. Install the ribbon cartridge (See 3.1)
5. Connect the interface cable. (See 3.11.3 for cabling information).
6. Check that the power switch on the printer rear is off (“0” side depressed). Connect the line
cord between the printer and an electrical outlet. The printer accepts 110 to 240VAC
nominal input. If a line cord was not supplied with the printer procure an IEC HAR line cord
that has an IEC 320-C13 style connector and the appropriate HAR plug for your country.
7. Turn on the power switch. READY should appear on the display. If the display is not legible
adjust the contrast knob located on top of the mechanism beneath the cabinet.
8. Configure printer and interface parameters (See 3.5-3.5.2) using 92 and 93 FUNCT.
Common variations to the default settings are a higher baud rate for better throughput,
EMULATION MODE I for Proprinter emulation and PROTOCOL = XON/XOF for software
that does not use DTR hardware handshaking. Function 94 settings are factory set for a
specific printer and should not be changed.
9. Perform a local print test (See 3.8) with 95 FUNCT.
10. If host printing is incorrect, check that 93 FUNCT Communication Parameters match the
host parameters and review all 92 FUNCT Printer Parameters.
Push in on cabinet latches
Rotate cabinet up and back.
1
Rotate lift ring forward to lift
and lock carriage.
3
Push ribbon guide plate tabs
down.
4
Rotate cartridge into place and snap in.
Rotate cartridge drive gear clockwise to
align and take up ribbon slack. Push
shield up. Lower carriage into operating
position. Close cabinet.
6
2
Remove foam shipping blocks.
5
RUBBER
WHEEL
RIBBON
SHIELD
TABS
RIBBON
PATH
Slip ribbon over and behind
guide plate tabs.
2