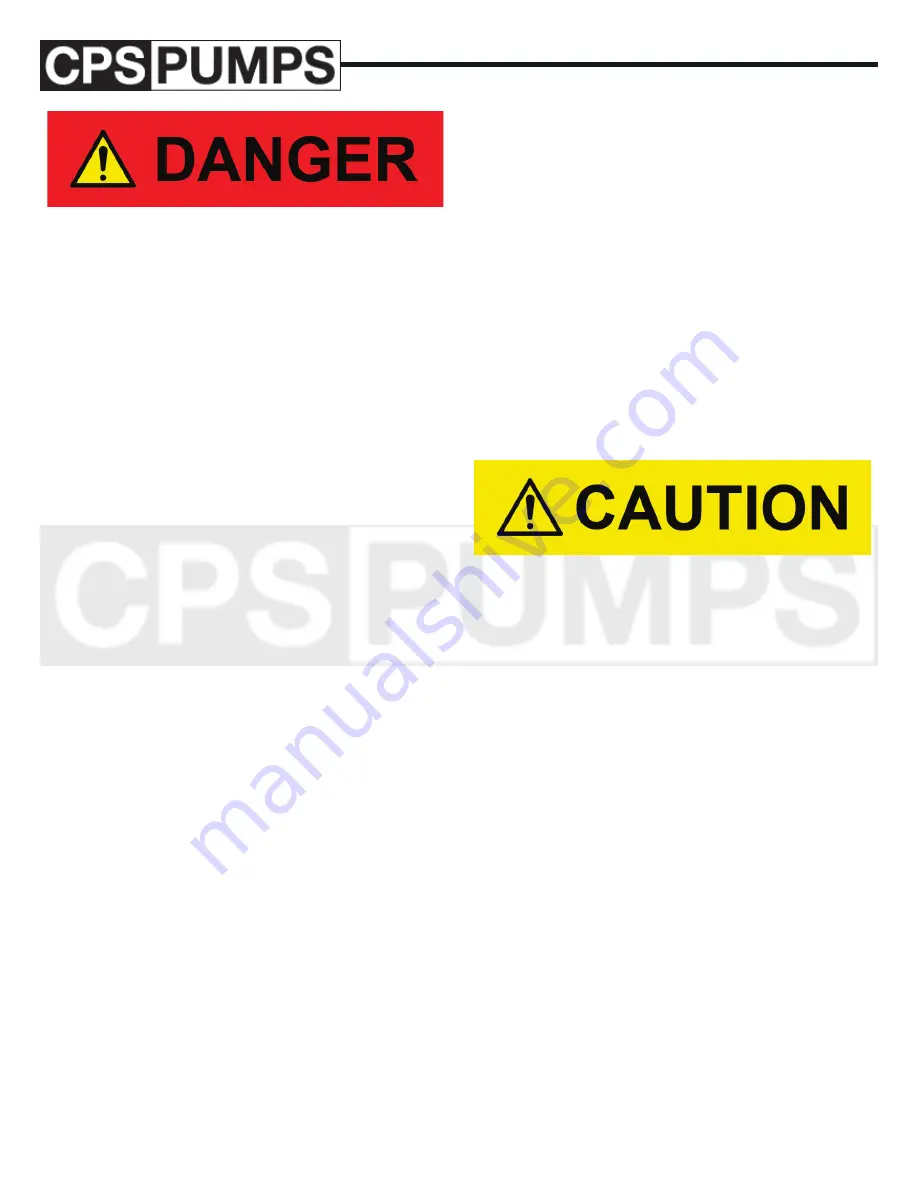
12
www.cps-pumps.com
IOM Manual: IOM-0000-CST
Series CST: Submersible Turbine
01/01/2018 - Edition 1A
Failure to ground the unit can result in serious or fatal shock. Refer
to electrical code requirements.
Slowly lower the unit into the well (or sump) adding joints of
column pipe as the unit is lowered. Tighten each joint securely.
See note above. Remove slack from the drop cable and attach
a cable clamp approximately every 10 feet. For units with large
heavy drop cable, additional cable support can be obtained by
installing a clamp immediately above each pipe coupling. Line
up the cable on one side of the pump and maintain as much
clearance as possible on that side when lowering the pump in
the well.
Be extremely careful not to scrape or damage the drop cable,
drop cable splice or grounding system when lowering the pump.
Hold the drop cable up away from the well casing as the pump is
being lowered. Never force the pump into the casing.
After the last piece of column pipe has been installed, install the
discharge elbow. Install a cable clamp between the last column
pipe coupling and the discharge elbow surface plate. Route the
drop cable and grounding system thru the large threaded hole
in the surface plate. Route the air line (if used) thru one of the
smaller threaded holes in the surface plate. The remaining small
threaded hole is for connection of a well vent or other acces-
sories. All of these holes are threaded with standard NPT pipe
threads. If a gasket is required between the discharge elbow and
its mounting surface, the gasket should be placed on the foun-
dation prior to installing the discharge elbow.
After the discharge elbow has been properly tightened, carefully
rotate the entire unit in the well until the discharge flange is
facing in the desired direction. Push the unit to one side of the
well, providing the maximum clearance for the drop cable when
rotating the unit.
Slowly lower the discharge elbow onto its mounting surface.
BE CAREFUL NOT TO DAMAGE THE GROUNDING
SYSTEM OR PINCH THE DROP CABLE BETWEEN
THE SURFACE PLATE AND THE WELL CASING. If a
gasket or other sealing device is used, be sure that it is aligned
properly and that it is not damaged. Install the discharge elbow
mounting bolts.
Before connecting the drop cable to the control panel:
• Take a resistance reading between the drop cable
conductors and ground to assure that the insulation on
the cable or splice was not damaged during installation.
See ELECTRICAL TESTS on page 18.
• Measure the resistance of the drop cable and motor
circuit. See ELECTRICAL TESTS on page 22. Com-
pare these readings with those taken in PRE-INSTAL-
LATION MOTOR AND DROP CABLE CHECKS
AND PREPARATION on page 10 to assure that the
splice is still intact.
Make the electrical connection between the drop cable and
the control panel. It may be desirable to use a terminal box at
the discharge to simplify the electrical work required when
the pump is pulled. See FIGURE 3. Be sure that the unit is
grounded properly.
Be sure to connect the leads as they were marked previously in
the procedure.
STARTING THE PUMP
Initial start-up and testing may require starting and stopping
the pump several times. BE SURE TO ALLOW ADEQUATE
COOLING OFF PERIOD BETWEEN STARTS. Consult the
motor manual. If no information is given, a good rule-of-thumb is
to allow a minimum of 15 minutes between starts.
For initial start-up allow the water to be pumped out onto the
ground. A throttle valve in the discharge line is recommended.
Position the throttle valve approximately one-fourth open for
start-up of the pump. This will prevent surging the well or the
pump during start-up.
If the pump has been in the well for several days before the
start-up, check the resistance between the cable conductor and
ground to assure that water has not penetrated the splice or the
cable insulation. See ELECTRICAL TESTS on page 18.
Clamp the tongs of a clamp-on type ammeter around one power
lead to the pump. Set the ammeter on the maximum scale.
After the motor starts, it can be reset to a lower scale as desired.
Refer to the motor manual and determine the normal operating
amps for the installed motor.
Start the pump and observe and record the current readings on
each conductor of the power lead. If the current exceeds the
normal value determined in the motor manual, stop the pump
immediately. A high current reading indicates that something
is wrong. Among the potential problems are: