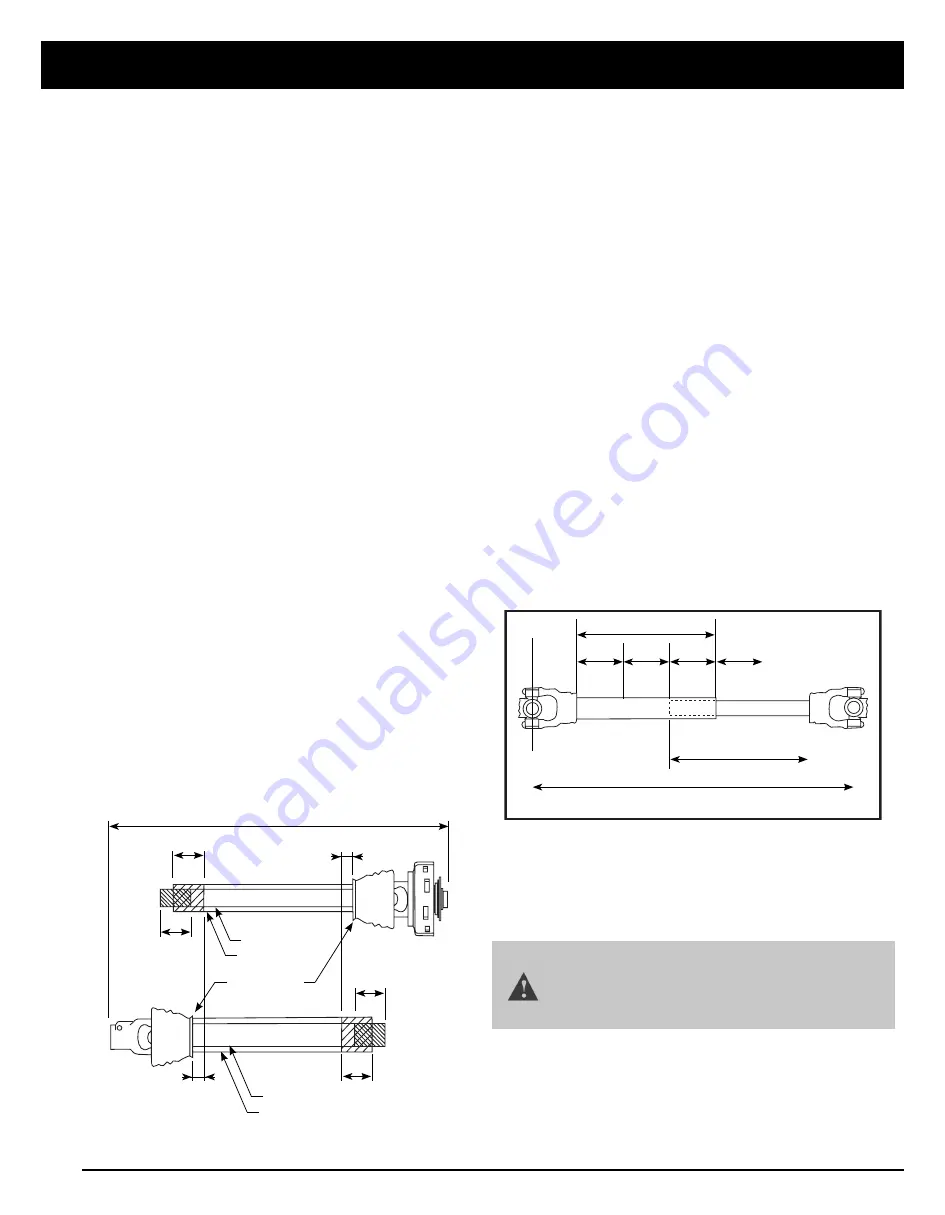
20
SIZING THE PTO SHAFT
Refer to Figure 1
1. Detach the driveline from tractor PTO shaft and
pull outer and inner drivelines apart.
2. Reattach outer driveline to tractor PTO shaft.
Pull on inner and outer drivelines to ensure
universal joints are properly secured.
3. Hold inner and outer drivelines parallel to each
other:
a. Measure 1” (“B” dimension) back from
outer driveline universal joint shield and
make a mark at this location on the inner
driveline shield.
b. Measure 1” (“B” dimension) back from
inner driveline universal joint shield and
make a mark at this location on the outer
driveline shield.
4. Remove driveline from tractor and gearbox
shafts.
5. Measure from end of inner shield to scribed
mark (“X” dimension). Cut off inner shield at the
mark. Cut same amount off the inner shaft (“X1”
dimension).
6. Measure from end of outer shield to scribed
mark (“Y” dimension). Cut off outer shield at
the mark. Cut same amount off the outer shaft
(“Y1” dimension).
7. Remove all burrs.
8. Continue with “Check Driveline Maximum
Length”.
INNER SHAFT
INNER DRIVELINE
OUTER DRIVELINE
INNER SHIELD
OUTER SHAFT
OUTER SHIELD
UNIVERSAL
JOINT SHIELD
TRACTOR END
IMPLEMENT END
Figure 1
- Driveline Shortening
A
B
B
X
Y
X1
Y1
FREE LENGTH
IMPLEMENT END
INNER PROFILE
OUTER PROFILE
1/3
1/3
1/3
1/3
1/3
OVERLAP
MAXIMUM ALLOWABLE LENGTH
Outer Shielding has been removed for clarity.
FREE LENGTH
TRACTOR END
Figure 2
- Driveline Maximum Extended Length
CHECK DRIVELINE MAXIMUM
LENGTH
Refer to Figure 2
Make sure driveline’s collapsible length is
acceptable.
The driveline maximum allowable length must,
when fully extended, have a minimum overlap
of the profile tubes by not less than 1/3 the free
length with both inner and outer profile tubes
being of equal length.
1. Apply multi-purpose grease to the inside of the
outer shaft and reassemble the driveline.
2. Assemble the two driveline profiles together
with 1/3 of the profile tubes overlapping as
shown below. Once assembled, measure and
record the maximum allowable length for future
reference.
3. Attach inner driveline yoke to the cutter’s
gearbox shaft. Attach outer driveline yoke to
the tractor’s PTO shaft.
4. Move yoke ends of driveline back and forth to
insure they are secured to the tractor and cutter
shafts. Reattach any end that is loose.
5. Hook driveline safety chain on the tractor end
of driveline to cutter frame. Re-latch safety
chain to the driveline shield.
MODIFYING PTO
IMPORTANT: Small chains are supplied with
the driveline. They must be attached to the
inner and outer driveline shields and to the
tiller and tractor to restrict shield rotation.