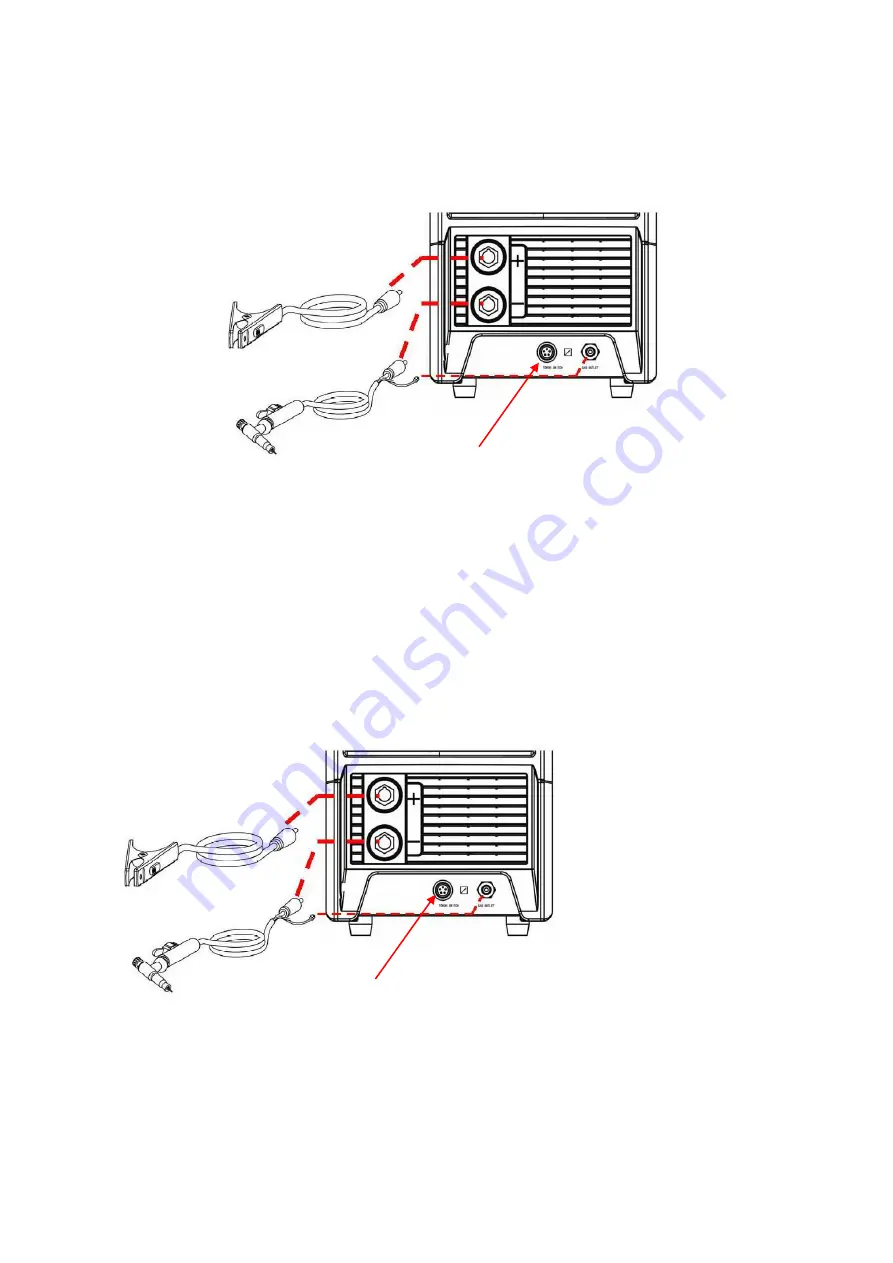
Page of 35
16
8.1.b
– Sequencer Control – Use the push button control in the TIG mode when using the
sequencer. Push the push button to initiate the arc and then push it again to advance to the
next step in the sequencer.
8.2 Remote Contactor And Amperage Control
– This unit comes standard with a remote foot pedal
control. The remote foot pedal is used to initiate the arc and then vary the amperage during your
weld. Connect the remote foot pedal control to the Foot Pedal Connection on the lower front panel.
Push Button
Connection
Foot Pedal
Connection