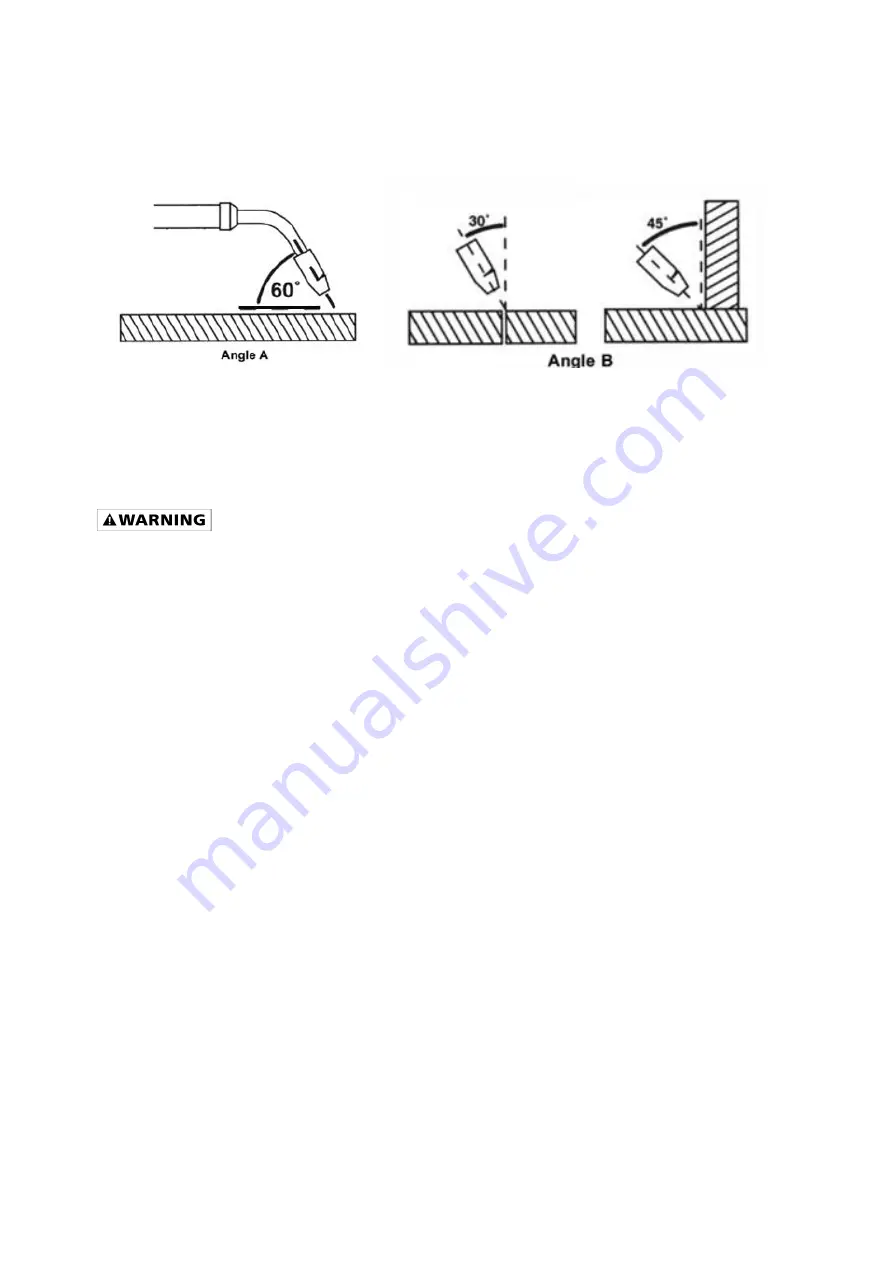
Page of 28
18
5.1. Angle a can be varied, but in most cases the optimum angle will be 60 degrees, the point at
which the torch angle is parallel to the work piece. If angle A is increased, penetration will increase.
If angle A is decreased, penetration will decrease also.
5.2. Angle B can be varied for two reasons: to improve the availability to see the arc in relation to
the weld puddle and to direct the force of the arc.
6. DISTANCE FROM THE WORK PIECE - If the nozzle is held off the work piece, the distance
between the nozzle and the work piece should be kept constant and should not exceed 1/4 inch or
the arc may begin sputtering, signaling a loss in welding performance.
7. TUNING IN THE WIRE SPEED - This is one of the most important parts of wire welder operation
and must be done before starting each welding job or whenever the voltage setting or wire diameter
is changed.
EXPOSURE TO A WELDING ARC IS EXTREMELY HARMFUL TO THE EYES AND SKIN!
Prolonged exposure to the welding arc can cause blindness and burns. Never strike an arc
or begin welding until you are adequately protected. Wear flame-proof welding gloves, a
heavy long sleeved shirt, trousers without cuffs, high topped shoes, and an ANSI approved
welding helmet.
7.1 Connect the Ground Clamp to a scrap piece of the same type of material which you will be
welding. It should be equal to or greater than the thickness of the actual work piece, and free of oil,
paint, rust, etc.
7.2 Select a heat setting.
7.3 Hold the torch in one hand. Hold the wire just off the work piece. (See HOLDING THE TORCH
section if you are uncertain of the angle at which you will be welding).
7.4 Set the wire feed speed based on the thickness of material and the set-up chart on the back
side of the wire feeder door.
7.5 Lower your welding helmet and pull the trigger on the torch and let the wire feed into the work
piece to start an arc, then begin to drag the torch toward you.
7.6 LISTEN! If the arc is sputtering, increase the wire speed slightly and try again. Continue
increasing the wire speed adjustment until you achieve a smooth buzzing sound. If the wire seems
to "pound" into the work piece, decrease wire speed slightly and try again. Use the wire speed
control to slightly increase or decrease the heat and penetration for a given voltage setting by
increasing or decreasing the wire speed slightly. Repeat this tune-in procedure if you select a new
voltage setting, a different wire diameter, or a different roll of wire.