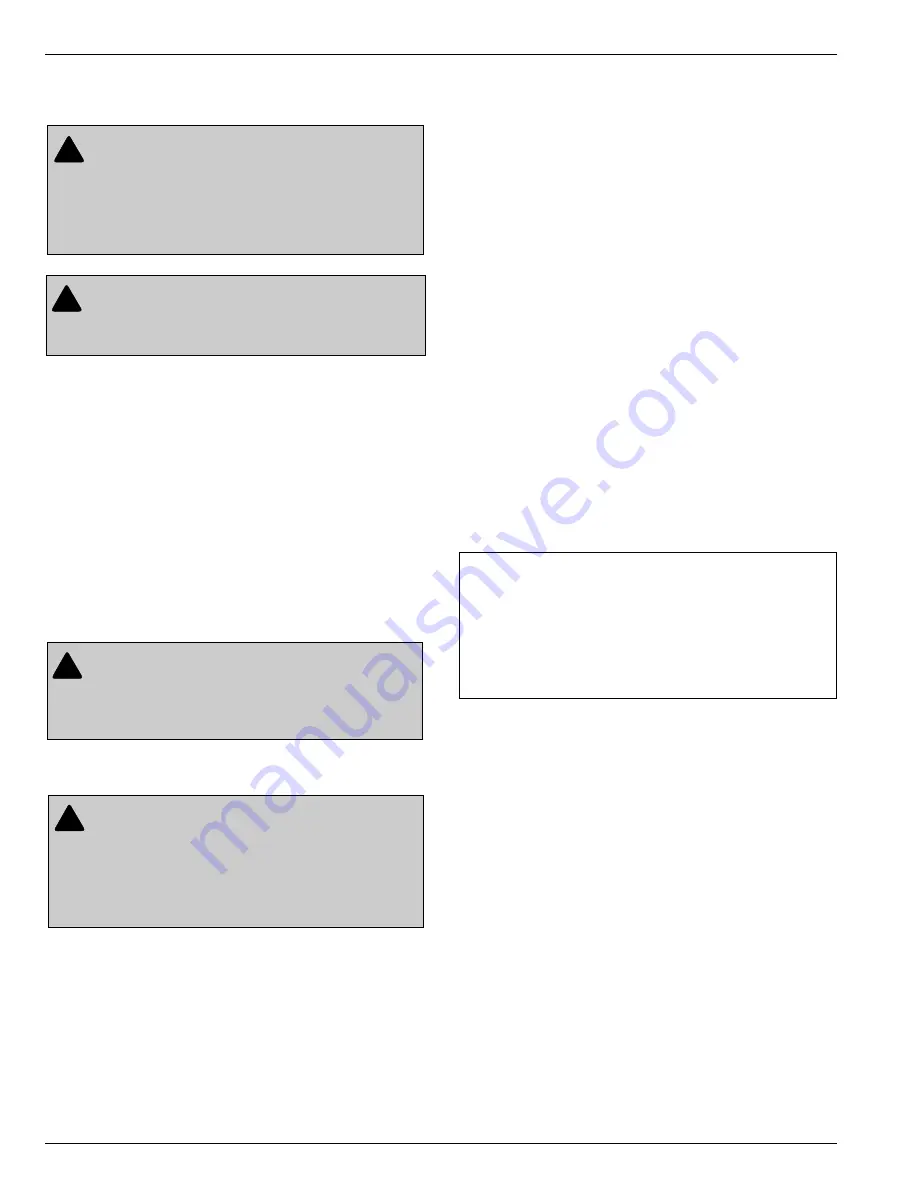
General
This troubleshooting guide is intended to assist in localiz-
ing problems that may be encountered in the operation of
the load-transfer scheme. After the problem area has
been localized, general troubleshooting and circuit tracing
techniques can be used to pinpoint the cause. A funda-
mental understanding of the basic operation is essential
in carrying out these troubleshooting procedures. (See
Theory of Operation section.)
Schematic diagrams, Figures 16 and 17, are used as
references throughout this guide. The physical location
of the various circuit components and terminals are
identified in Figure 27.
Remove the Control from Service
The following warning only applies to controls
equipped with the Fault Block Accessory:
1. De-energize Source I and Source II voltage.
2. Disconnect cables from the control.
Basic Troubleshooting
A quick check of the basic transfer operation while the con-
trol is in service can be made using the following procedure:
Source I or Source II Preferred
Operation
1. Set CONTROL MODE switch (S5) to TEST. This wilI
remove the control from service and allow it to operate
without operating the high-voltage transfer switches.
2. Check LATCH RELAY STATUS TEST terminals (T-1,
T-2) to ground (T-3). 120 Vac at T-1 indicates the con-
trol is in Source I mode; 120 Vac at T-2 indicates the
control is in Source II mode. Check if this agrees with
the SOURCE PREFERENCE switch setting.
3. Remove preferred source voltage by unscrewing one
of the phase fuses from the applicable source. The
PREFERRED TO ALTERNATE TIMER will start.
4. When the timer runs out, the latch relay (R1) will
transfer; indicated by a transfer of the 120 Vac signal
at the test terminals.
5. Replace the removed fuse to re-energize the pre-
ferred source. The ALTERNATE TO PREFERRED
TIMER will start.
6. When the timer runs out, the latch relay (R1) will
transfer back to its original operating position.
7. Return the CONTROL MODE switch (S5) to NOR-
MAL to return the control to service.
Type S Automatic Load-Transfer Control Installation, Operation, and Maintenance Instructions
20
TROUBLESHOOTING—BASIC S CONTROL
IMPORTANT: If Control Mode Switch S5 is placed in
the “Normal” position, the S-control will place the high-
voltage transfer switches into the configuration that is
currently selected by the Source Preference Switch
S4. This may result in an unintended transfer. Make
sure the desired state of the high-voltage transfer
switches match the setting of S4 before returning S5 to
the “Normal” position.
WARNING:
Hazardous voltage. Solidly ground
all equipment. Failure to comply can result in
death, severe personal injury, and equipment damage.
T223.2
!
CAUTION:
Equipment misoperation. Do not
energize this equipment until all control settings
have been properly programmed and verified. Refer to
the Control Programming and Operation section of this
manual for programming procedures. Failure to com-
ply can result in misoperation (unintended operation),
equipment damage, and personal injury.
G118.1
!
WARNING:
Hazardous Voltage. De-energize
switchgear before attempting to disconnect con-
trol cable from control. Failure to do so may result in
contact with high voltage pulse (300V peak) from the
CT protection circuit. Failure to de-energize switchgear
can result in contact with high voltage, which will cause
death or severe personal injury.
G124.0
!
DANGER:
Hazardous voltage. Contact with haz-
ardous voltage will cause death or severe per-
sonal injury. Follow all locally approved safety proce-
dures when working around high and low voltage lines
and equipment.
G103.3
!