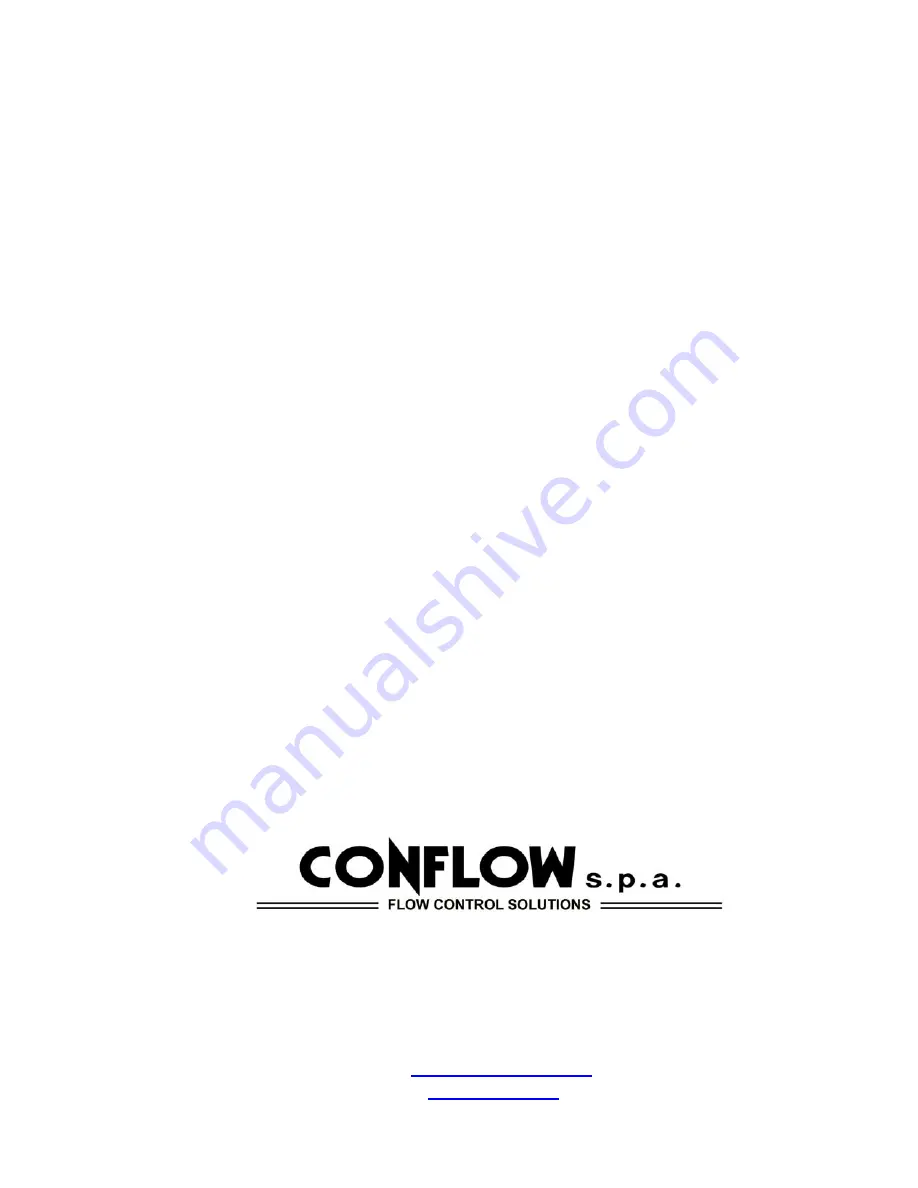
Servizio Assistenza
– Servicing Department
Via Lecco, 69/71
20864 AGRATE BRIANZA (MB)
– ITALY
Tel: +39 - (0)39 - 651705 / 650397
Fax: +39 - (0)39
– 654018
www.conflow.it
Servizio Assistenza
– Servicing Department
Via Lecco, 69/71
20864 AGRATE BRIANZA (MB)
– ITALY
Tel: +39 - (0)39 - 651705 / 650397
Fax: +39 - (0)39
– 654018
www.conflow.it