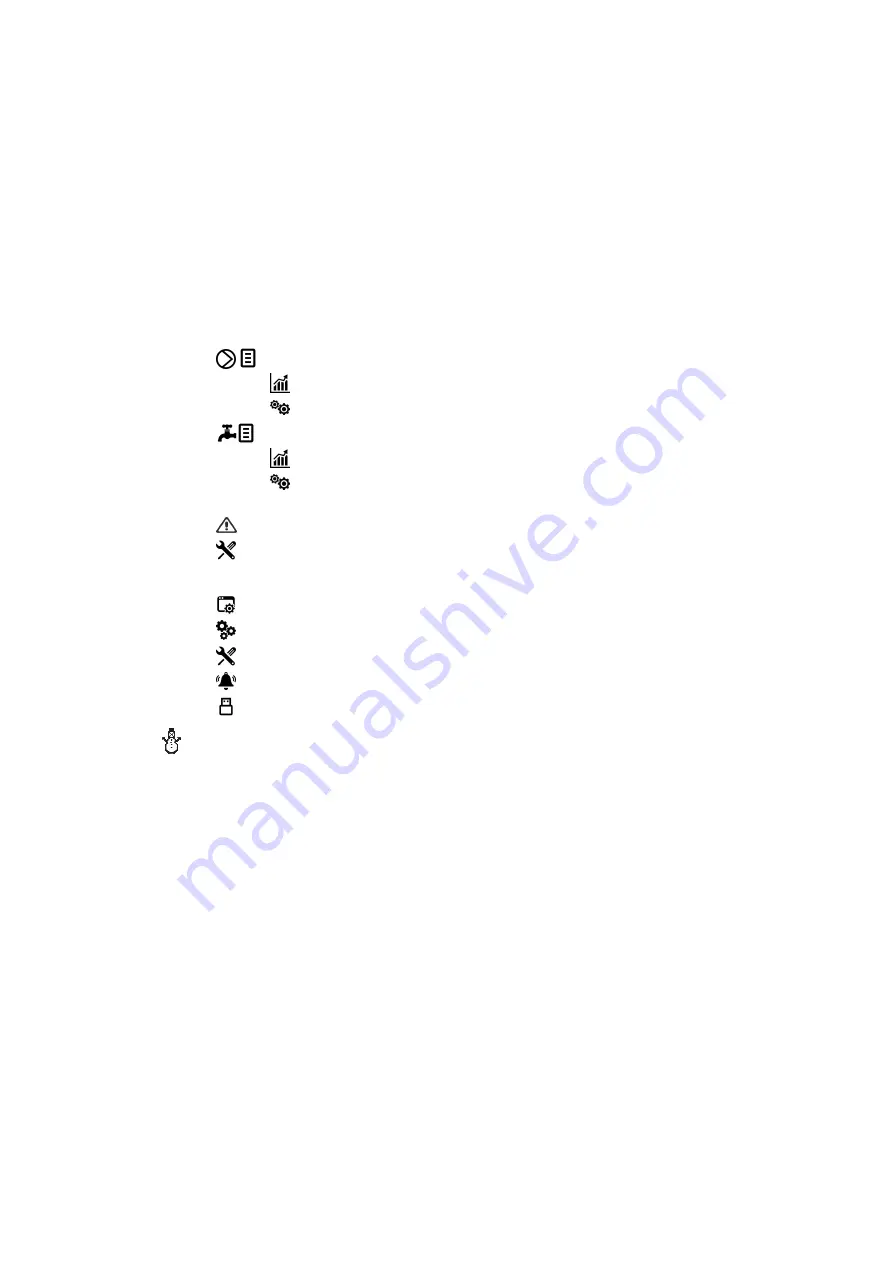
Operating Instructions (GB)
900 191 - V1.0
_________________________________________________________________________________
Page 2
9.
Fuse protection and optional accessories
24
9.1
Power unit
24
9.2
Fuse protection provided by customer
24
9.3
24 VAC transformer
24
9.4
Circuit breaker, emergency off
24
9.5
Residual current circuit breaker (RCCB)
24
9.6
Overvoltage protection
24
9.7
Battery module*
24
10.
Main display
25
10.1
Main display overview
25
10.2
Pump-out
29
10.2.1
Pump-out function operating data
29
10.2.2
General pump-out settings
30
10.3
Infeed
31
10.3.1
Infeed function operating data
31
10.3.2
General infeed settings
32
10.4
Level monitoring – 4…20mA
33
10.5
Error messages
34
10.6
Maintenance
35
11.
Main menu
36
11.1
Main menu overview
36
11.2
Setup submenu
37
11.3
Maintenance submenu
40
11.4
Alarms submenu
41
11.5
USB submenu
43
12.
Functional description winter operation
44
12.1
Manual control
45
12.1
Automatic control
45
13.
Commissioning / recommissioning
46
14.
Decommissioning
46
15.
Servicing
46
16.
Technical data
47
17.
List of faults and declaration
48
18.
Declaration of conformity
49
19.
Notes
50