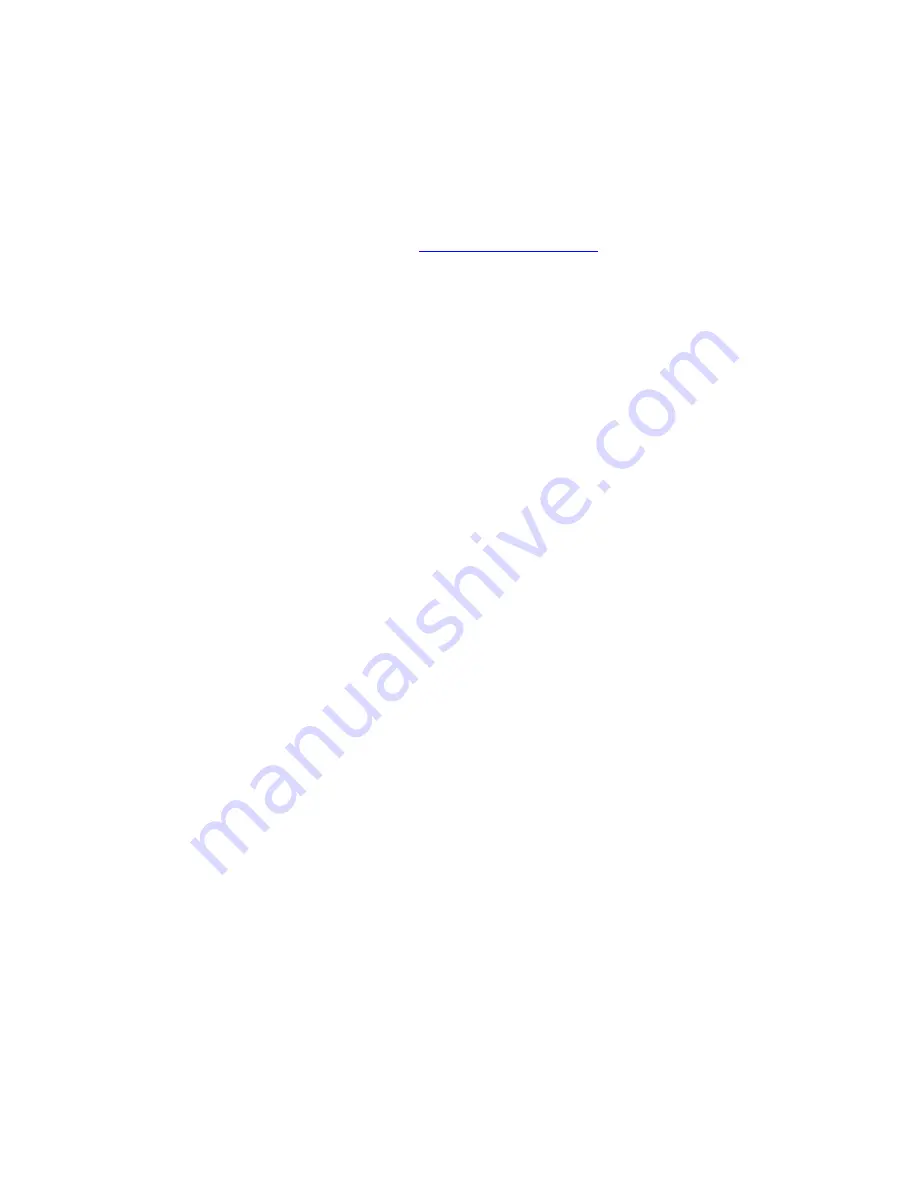
Building instructions
Please be aware, that these instructions are only temporary, as we took the former FiberClassics
instructions and just copied and modified them slightly. As Composite-ARF feels strongly in charge of
improving the Kangaroo instructions to the level of other Composite-ARF instructions, we will keep you
updated on our homepage, when the new instruction book will be finished. But you should not worry,
building the Kangaroo is so easy, that even with the instructions in front of you you will be able to
complete the task with no major problems. If you experience any problems, please contact your Rep, he
will happy to help you out. Please email us at
when you face any problems,
which should be adressed in the new instructions with priority.
As already described in the Introduction, you will find that the kit contains very highly pre-fabricated airframe
components of excellent quality moulded in GRP, some of them with sandwich reinforcement, with a virtually
faultless white/red pigmented surface. The wings are ready-made at the factory, leaving only the installation of
the servo mounts (included in the kit), and the elevon linkages to be completed. The same also applies to the
rudder linkages. The model can be completed, ready to fly, in a very short time - typically 25 to 40 hours -
although this does depend on your experience and technical expertise. The fact that the model is supplied in a
two-colour finish and features virtually spotless surfaces means that the time-consuming tasks of painting and
other surface treatment are eliminated. Your own markings can be applied (self-adhesive film or painted) to give
your model an impressive and unique appearance.
The most difficult process in building the model is the installation of the retract units. The model features
marked guide lines which are designed for the pneumatically operated and braked retract units, Graupner Order
No. 175, which we recommend for this model, but the wells are not pre-cut.
It would certainly be possible for the factory to prepare pre-cut wells for the retract units, but there are
drawbacks to this: there are countless different types of retract unit on the market, and many modellers are strict
adherents to one or other make; in some cases the builder will have a set of retracts on the workshop shelf which
are to be used, and for all these reasons we decided to leave it up to the builder to cut out and trim the retract unit
openings to suit the undercarriage you intend to install, even if you do settle on the recommended units (Order
No. 175). The undercarriage mounts are pre-installed and bonded into the airframe at the factory, and the mounts
are designed to suit the retract units, Order No. 175, as we have already mentioned. Slight trimming and
adjustment may well be required for these mounts due to manufacturing tolerances, even if you use the retract
units we recommend.
If you decide to install our suggested retract units, you can follow the dimensions stated in the stage photos and
the building instructions when cutting the openings for the wheels and mechanical units. These dimensions
may
also be used as the starting point for other makes of retract unit,
but - as already stated - even the dimensions
in these instructions are only approximate values; they were measured from our existing prototype
models
. The basic aim should be to keep the openings as small as possible, i.e. only as large as necessary, but
large enough to allow the retracts to function correctly even if the wheel legs are slightly bent.
If you decide to install the airbrake / speed brake as suggested, we recommend that you mark and cut out the
opening at the same time as you cut the openings for the retract units, so that the experience you gain initially
can be exploited for the remaining work.
When you are marking out the position of the speed brake take care to locate it centrally and symmetrically, and
cut it to the exact size stated. When cutting out the speed brake be aware that the brake flap you cut out is the
brake flap you will use; the kit does not include a replacement panel or separate flap! With this in mind, aim at
the narrowest possible gap when cutting, i.e. the tool which you use to separate the flap should be around the
width of a balsa knife blade or a miniature sawblade. Cut very carefully!
Although the surface of the fuselage is hard GRP, in practice we find that it is best to use a reasonably rigid balsa
knife or craft knife to cut the openings in the fuselage.
For accurate straight cuts use a steel straight edge or ruler. Curves can be cut free-hand, or - better - using a
template which you prepare yourself.
The first step in cutting out the retract unit wells is to mark the dimensions on the fuselage (1) as shown in Figs.
1, 2 and 3 (note: dimensions are approximate). Next you have to check whether the marked lines coincide
reasonably well with the factory-installed retract unit mounts. This is done by holding the fuselage against a very
bright light: the bonded-in mounts will show up as shadows, and you can check their position with fair accuracy