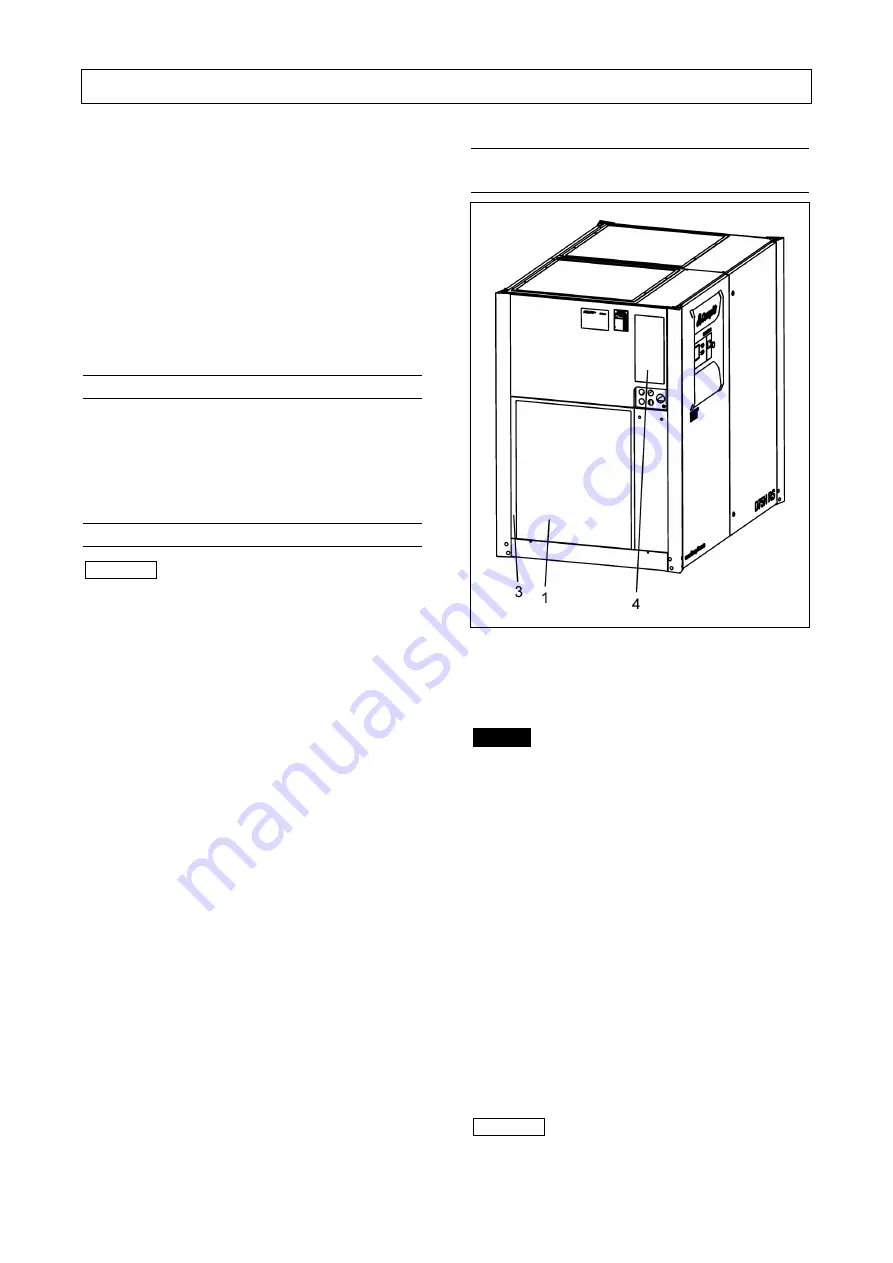
9. Service and maintenance
45
Change the control transformer setting as follows if
the output voltage is not correct:
•
Set the main power switch to "O" (OFF) and secure
it from being switched on again.
•
Please wait another 10 minutes. The power
condensers require this time in order to discharge!
•
Change the control transformer setting accordingly.
Fig. 24 illustrates an example.
•
Then check the setting again.
9.10
Fittings
The fittings of the air and water circuits have to be
checked and, if required, re-tightened according to the
maintenance schedule.
Check the hose and piping for unsealed areas.
9.11
General maintenance and cleaning
Important
Blow off the screw compressor unit with
compressed air at the specified intervals (never
direct compressed air towards persons) paying
particular attention to:
•
Regulating elements
•
Fittings
•
Compressor block
•
Cooler
•
Electric motor
•
Remove and clean the dirt trap strainer
(W-version only)
9.12
Clean / change filter with cooling air
inlet and control cabinet inlet
Fig. 25
1 Filter mat cooling air inlet
3 Sound-proofing element
4 Inlet filter
Danger
Only perform checks and carry out work on the
screw compressor when the unit is out of
operation, depressurized, and secured from being
switched on again!
a) Filter mat cooling air inlet (-1- Fig. 25)
Perform filter mat change as follows:
•
Remove fixing bolts.
•
Take out the filter mat (-1- Fig. 25) and clean it,
replace it if damaged.
•
Return the filter mat to the silencer chamber
(-3- Fig. 25).
•
Secure the filter mat using the fixing bolts.
Cleaning:
Clean the filter mat by brushing or washing.
Important
Never install the filter mat in a wet or moist state!
Summary of Contents for D110H RS
Page 2: ......
Page 58: ...11 Annex 56 11 2 Layout plan 11 2 1 Layout plan D110H RS Fig 32 all dimensions in mm...
Page 59: ...11 Annex 57 Fig 33 all dimensions in mm...
Page 61: ...11 Annex 59 Fig 35 all dimensions in mm...
Page 63: ......