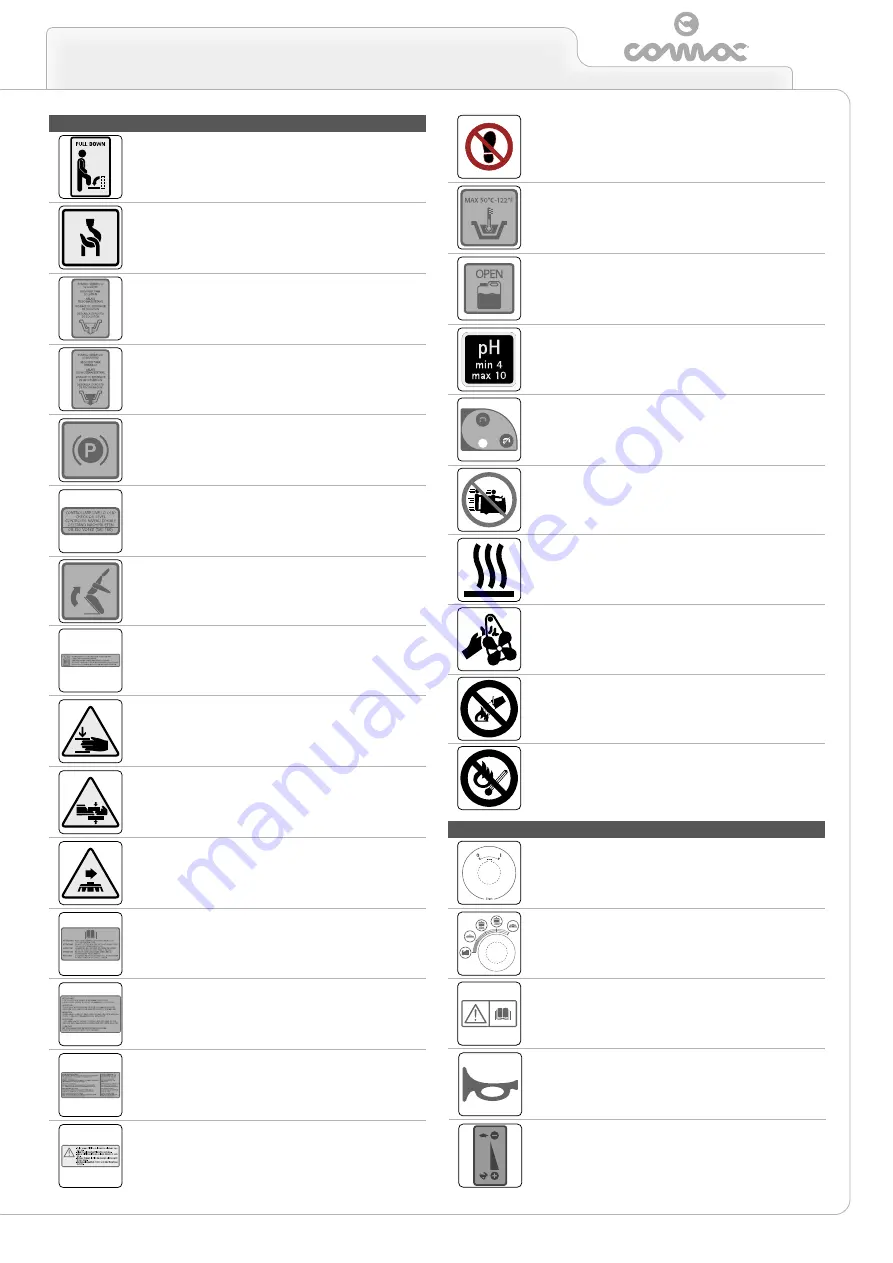
Inspection ramp label:
Used on the back of the machine to indicate the position of the inspection and
recovery tank maintenance footboard.
Lifting hook label:
Used to indicate where to screw in the eye bolts for safely lifting the machine.
Solution tank drainage tube label:
Located on the rear part of the machine, to identify the solution tank drainage
tube.
Recovery tank drainage tube label:
Located on the rear part of the machine, to identify the recovery tank drainage
tube.
Parking brake lever label:
Located near the operator seat, to identify the command lever of the parking
brake.
SYMBOLS USED ON THE MACHINE
Braking system oil level check label:
Located near the braking system oil basin, to remind the operator to check the
level of oil in the basin.
The bottom part of the label shows the recommended oil for the braking system.
Vacuum motor filter label:
Applied inside the vacuum cover to identify the vacuum motor intake air filter,
and also serves to remind the operator to clean the filter after each machine use.
Seat lifting handle label:
Located near the operator's seat to indicated the handle to be used for lifting the
seat support plate.
Label warning about the risk of crushed hands:
Indicates danger to hands due to crushing between two surfaces.
Label warning about the risk of crushed limbs:
Indicates danger to limbs due to crushing between two surfaces.
Label warning about sideways brush head movement:
Located on the right-hand side of the machine, to warn that the scrubbing brush
head can be shifted sideways.
Treading ban label:
Located on the machine, to identify the surfaces that must not be trodden on (risk
of personal injury or damage to the machine).
Label indicating the need to read the Use and Maintenance Manual:
Located near the steering column, to remind the operator to read the Use and
Maintenance Manual before using the machine.
Label indicating that flammable/explosive dusts and/or liquids must not be
vacuumed:
Located near the steering column, to indicate that it is forbidden to vacuum
flammable or explosive dusts or liquids with the machine.
Battery recharging and daily care label:
Located near the steering column, indicating how to recharge the batteries. On
the side, it reminds the operator of the need to clean the squeegee body and all
the machine filters every day.
Label about detergent solution filter cleaning:
Located on the front left-hand side of the machine, to identify the position of the
detergent solution filter and remind the operator to clean it after every machine
use.
Symbol of maximum temperature for filling the solution tank:
Located on the upper part of the solution tank, to indicate the maximum
temperature of the water for filling the solution tank safely.
Detergent solution pH label (CDS versions):
Located on the detergent tank cap to indicate the maximum and minimum pH
values of the detergent used with the CDS system.
Label for detergent solution tap control:
Located near the operator seat, to identify the command lever for the detergent
solution tap.
Label forbidding the use of the machine as a means of transport:
Located on the back of the machine to indicate that the inspection footboard
should not be used to transport people.
Label warning about the risk of burns:
Used in the vicinity of the endothermic engine to indicate the risk of burns if
certain surfaces are touched.
Label warning about the hazard posed by the moving belt and fan:
Used in the vicinity of the endothermic engine's radiator to indicate that the fan
and fan belt on the endothermic engine's radiator are in movement, and could
pose a serious risk of injury to the limbs.
Label indicating the prohibition to extinguish fires with water:
Used in the vicinity of the endothermic engine's fuel tank to indicate the prohibition
to extinguish fires using water.
Label indicating the prohibition to approach with open flames:
Used in the vicinity of the endothermic engine's fuel tank to indicate the prohibition
to approach with any type of open flame.
Detergent canister location label (CDS versions):
Used on the back right of the machine to indicate the chemical detergent canister
hatch.
Main switch symbol:
Applied to the control panel, positioned on the front of the machine, to indicate
the main switch.
i-drive selector symbol:
Indicates the command knob for the i-drive program selector.
Open book caution symbol:
Used in the control panel to tell the operator to read the manual before using
the machine.
SYMBOLS USED ON THE CONTROL PANEL
Buzzer symbol:
Indicates the buzzer command button.
Endothermic engine speed adjustment command symbol:
Used on the control panel to indicate the endothermic engine's speed adjustment
lever.
15