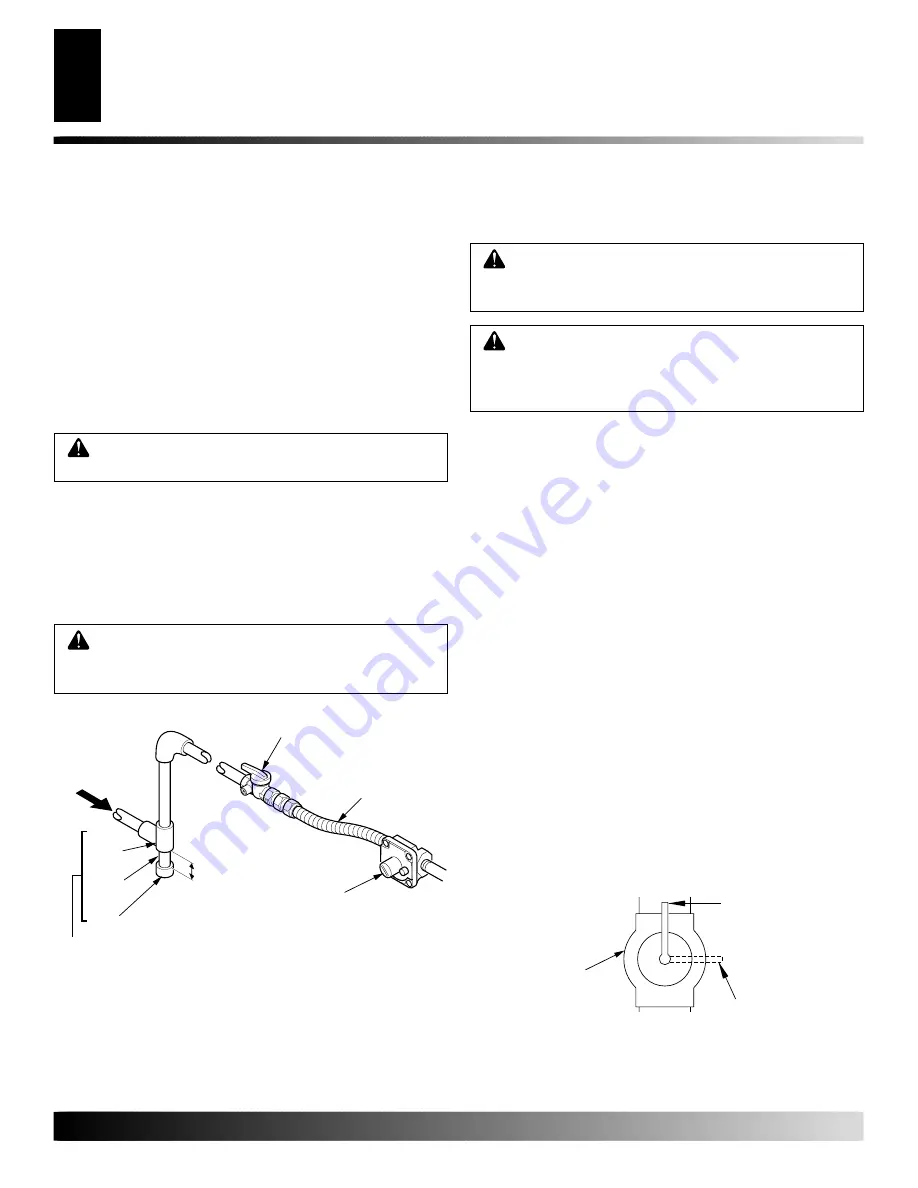
107123-01F
For more information, visit www.desatech.com
For more information, visit www.desatech.com
12
INSTALLATION
Connecting To Gas Supply (Cont.)
Checking Gas Connections
CAUTION: Avoid damage to regulator. Hold gas
regulator with wrench when connecting it to gas
piping and/or fittings.
WARNING: Use pipe joint sealant that is resistant
to liquid petroleum (LP) gas.
Figure 15 - Gas Connection
* Purchase the optional CSA design-certified equipment shutoff
valve from your dealer. See Accessories, page 36.
** Minimum inlet pressure for purpose of input adjustment.
INSTALLATION
Continued
Tee
Joint
Pipe
Nipple
Cap
3" Minimum
Sediment Trap
Gas
Regulator
From Gas Meter
(5" W.C.** to
10.5" W.C.
Pressure)
CSA Design-Certified Equipment
Shutoff Valve With 1/8" NPT Tap*
Approved Flexible
Gas Hose (if allowed
by local codes)
We recommend that you install a sediment trap in supply line as
shown in Figure 15. Locate sediment trap where it is within reach for
cleaning. Install in piping system between fuel supply and heater.
Locate sediment trap where trapped matter is not likely to freeze. A
sediment trap traps moisture and contaminants. This keeps them
from going into heater controls. If sediment trap is not installed or
is installed wrong, heater may not run properly.
WARNING: Never use an open flame to check for
a leak. Apply a noncorrosive leak detection fluid to all
joints. Bubbles forming show a leak. Correct all leaks
at once.
WARNING: Test all gas piping and connections
for leaks after installing or servicing. Correct all leaks
at once.
CHECKING GAS CONNECTIONS
Pressure Testing Gas Supply Piping system
Test Pressures In Excess Of 1/2 PSIG
(3.5 kPa)
1.
Disconnect appliance with its appliance main gas valve (control
valve) and equipment shutoff valve from gas supply piping sys-
tem. Pressures in excess of 1/2 psig will damage heater regulator.
2.
Cap off open end of gas pipe where equipment shutoff valve
was connected.
3.
Pressurize supply piping system by either using compressed
air or opening main gas valve located on or near gas meter.
4.
Check all joints of gas supply piping system. Apply a noncor-
rosive leak detection fluid to gas joints. Bubbles forming show
a leak.
5.
Correct all leaks at once.
6.
Reconnect heater and equipment shutoff valve to gas supply.
Check reconnected fittings for leaks.
Test Pressures Equal To or Less Than 1/2 PSIG (3.5 kPa)
1.
Close equipment shutoff valve (see Figure 16).
2.
Pressurize supply piping system by either using compressed
air or opening main gas valve located on or near gas meter.
3.
Check all joints from gas meter to equipment shutoff valve
(see Figure 17, page 13). Apply a noncorrosive leak detection
fluid to gas joints. Bubbles forming show a leak.
4.
Correct all leaks at once.
Figure 16 - Equipment Shutoff Valve
O
POS
PO
Open
Closed
Equipment
Shutoff Valve
Installation must include an equipment shutoff valve, union, and
plugged 1/8" NPT tap. Locate NPT tap within reach for test gauge
hook up. NPT tap must be upstream from heater (see Figure 15).
IMPORTANT:
Install equipment shutoff valve in an accessible
location. The equipment valve is for turning on or shutting off the
gas to the appliance.
Check your building codes for any special requirements for locating
equipment shutoff valve to fireplaces.
Apply pipe joint sealant lightly to male NPT threads. This will
prevent excess sealant from going into pipe. Excess sealant in pipe
could result in clogged heater valves.