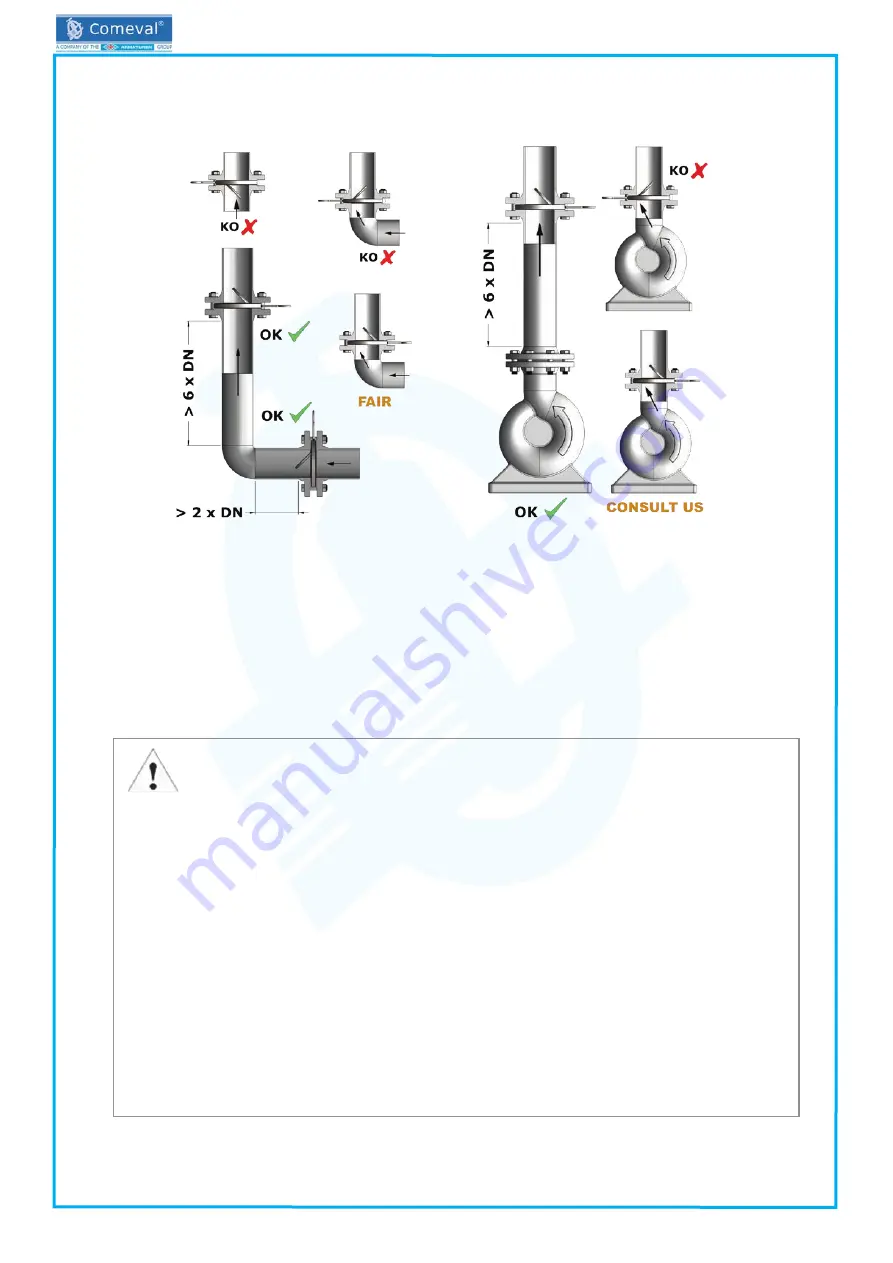
IOM - WAFER SWING CHECK VALVES, UNIWAT® CV
©COMEV
AL
V
AL
VE SYSTEMS
Technical Dept. Ref. IOM - W
AFER SWING CHECK V
AL
VES, UNIW
AT® CV - Ed.20/06
Comeval V
alve Systems reserves the right to alter any technical data contained in this Manual without prior notice. Regularly updated data on www
.comeval.es
5.2 Requirements at the place of installation
- Downstream from a disruptive element (pump, valve, elbow, pipe reduction) leave as much distance as possible; mini
-
mum distance recommended: 6 times the valve diameter (6xDN).
- Upstream from a disruptive element leave at least a distance of 2xDN.
- Aggressive environmental conditions may reduce the life span of the product. Consider special construction/protective
measures in such a case.
- Consider the interaction between the system and the equipment. Foresee elements to absorb vibrations, pipe dilata-
tions, guides, anchoring and proper support according to the weight of the components.
- The system and operation protocol should be conceived in such a way to avoid high velocities. Prevent pulsing flow or
water hammers, which are very harmful for valves and the rest of the components.
- Flooding of the product is not recommended.
- Allow enough space for valve installation, operation and maintenance.
- It is recommended to install a proper sized mesh strainer upstream the valve in order to protect seating surfaces from
abrasion or erosion that could lead to seat leakage.
- Planners / construction companies or the owner are responsible for positioning and installing products.
6. COMMISSIONING & OPERATION
- In case of risk of media freezing inside the valve, take due measures to avoid it.
Page 4
ATTENTION!
- Before commissioning the valve, check the material, pressure, temperature, flow direction and other essential
parameters. Always use the product within the scope of intended service and operating duties.
- Before commissioning, make sure previous chapters have been thoroughly followed.
- Regional safety instructions should be adhered to.
- It is essential to flush the pipe system thoroughly to eliminate all the particles and impurities which could remain
in the pipes and particularly welding residue, chips, tool remains, etc. that could damage the equipment during
start-up. Ensure that during cleaning of the pipe system, any chemicals used and temperature are compatible
with the valve construction.
- Temperatures above 50ºC or below 0ºC may cause personnel injuries if valves are touched.
- Leakage of media through valve, between counterflanges or at closing may also cause scalding, health harm,
pollution, fire or damage to other parts of the installation depending on the media.
Use suitable protection equipment when approaching the valve, ensure that the corresponding warning signs are
displayed on the valve or surrounding area, and/or isolate the equipment in case of danger.
- Before commissioning a new plant or restarting it after repairs or modification, always ensure that:
- All work has been completed correctly.
- The valve is in the correct position for its function.
- Safety devices/ measures have been implemented.
- The filling, warming-up and starting-up of the system shall be gradual so as to avoid any inadmissible stress. Check
for tightness in valve connections, and retighten crosswise and gradually if necessary until leakage elimination.