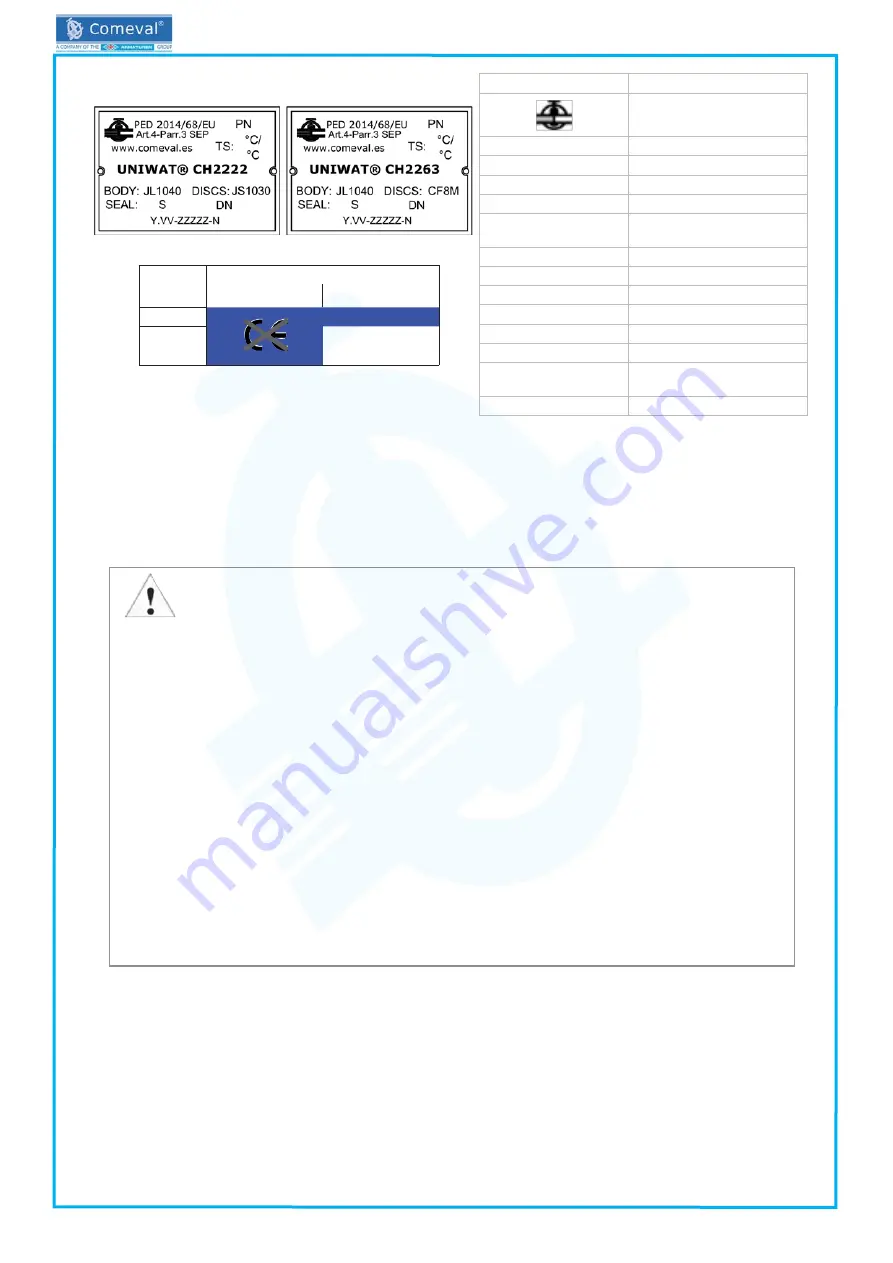
IOM - WAFER DUAL PLATE CHECK VALVES, UNIWAT® CH
©COMEV
AL
V
AL
VE SYSTEMS
Technical Dept. Ref. IOM - W
AFER DUAL
PLA
TE CHECK V
AL
VES, UNIW
AT® CH - Ed.20/06
Comeval V
alve Systems reserves the right to alter any technical data contained in this Manual without prior notice. Regularly updated data on www
.comeval.es
4.4 Marking/nameplate
Nameplate description of the valve:
4.5 CE marking. Intended use acc. to PED
* Classification of fluids group 2 acc. to Directive 2014/68/EU, Article 13.
Check valve selection, material compatibility, pressure and temperature limits and other essential parameters. Ensure
proper safety devices/measures are implemented to prevent exceeding intended use of the product. Contact the manu
-
facturer for advice in case of pressure tests exceeding the intended use. Refer to Data Sheet and consult the manufac
-
turer for further information.
5. INSTALLATION
5.1 General remarks on installation
The following points should be taken into account in addition to the general principles governing installation work:
5.2 Requirements at the place of installation
- Downstream from a disruptive element (pump, valve, elbow, pipe reduction) leave as much distance as possible; mini
-
mum distance recommended: 6 times the valve diameter (6xDN).
- Upstream from a disruptive element leave at least a distance of 2xDN.
- Aggressive environmental conditions may reduce the life span of the product. Consider special construction/protective
measures in such a case.
- Consider the interaction between the system and the equipment. Foresee elements to absorb vibrations, pipe dilata-
tions, guides, anchoring and proper support according to the weight of the components.
- The system and operation protocol should be conceived in such a way to avoid high velocities. Prevent pulsing flow or
water hammers, which are very harmful for valves and the rest of the components.
- Flooding of the product is not recommended.
- Allow enough space for valve installation, operation and maintenance.
Page 3
ATTENTION!
- Before installation, make sure previous chapters are thoroughly followed.
- Ensure safe access and working conditions for proper performance.
- Observe all applicable safety measures during installation.
- Remove remaining packing/storage protection if present.
- Lay pipelines such that damaging transverse, bending and torsional forces are avoided.
- Protect valves from dirt during construction work. The interior of the valve and the pipeline must be free of fo
-
reign particles.
- Protect the valve soft parts from heating caused by welding works at the plant during commissioning.
- Avoid mechanical damage to the seat, discs and rubber gaskets.
- Follow the arrow in the body for normal flow direction for installation. The valves can be assembled vertically on
horizontal pipeline, with hinge pin in vertical position, or horizontally on vertical pipeline with normal flow upwards.
- There is a crushing hazard between the discs and the seat. Ensure the discs are in rest position in case a hand
is introduced inside the valve.
- When installing the valve, there is a crushing hazard between valve and pipe system. Mind the hands to avoid it.
- Install the valves always between flanges, using integral rubber gaskets provided with each valve. Be sure that
the contact faces are free of impurities or fluid residues that may compromise the tightness.
- Big sizes are provided with eye bolt to ease their correct fitting between flanges in horizontal pipelines. For val
-
ves without eye bolt installed in horizontal pipeline, make sure the hinge pin is in vertical position.
- In order to fit the valve between flanges, insert one or two stud bolts and tighten them with nuts without forcing.
Set it on the already inserted stud bolt. Once centered, insert the other stud bolts and tighten them with nuts dia
-
gonally and gradually. Valve should fit smoothly between flanges without building any tension.
Mark
Description
Manufacturer logo
www.comeval.es
Website of manufacturer
UNIWAT®
Brand
CH2222/CH2263
Valve type
S
Seal material (EPDM, NBR)
Y.VV
Manufacturing year
(Y.16 = 2016)
ZZZZZ-N
Batch / Serial no.
TS
Min. / max. temperature
JL1040
Body material
JS1030 / CF8M
Discs material
PED 2014/68/EU
Directive 2014/68/EU
SEP
Sound Engineering Practice
PN
Nominal pressure
(max. pressure in bar)
DN
Nominal Diameter
PS
DN
≤300
350-600
10
16
Out of scope
Liquids of group 2* compatible with materials of construction,
acc. to
Directive 2014/68/EU
Annex II table 9 up to category I