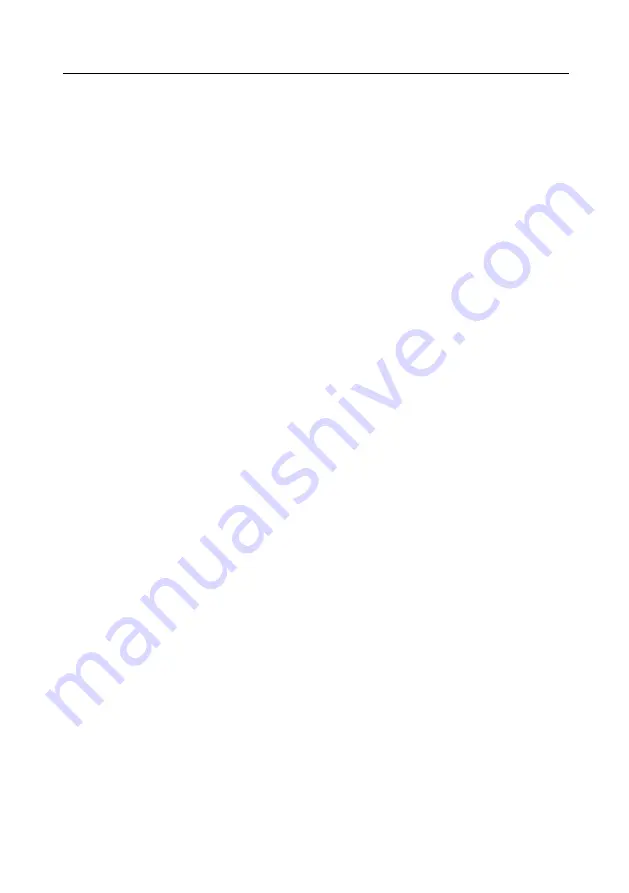
POH LTF-UL-2019 C42B Issue 1 • Pilot Operating Handbook
POH LTF-UL-2019 C42B Issue 1
Page 74 of 84
In most cases the authorized IFC, ISC or ITB which sold and/or installed
your aircraft and original accessories will honour a warranty claim and/or
provide warranty service.
Claiming
In order to claim the warranty service you must return the aircraft and/or
accessory in question to the authorised ISC or ITB in the original
configuration as supplied by Comco Ikarus.
The microlight aircraft should be accompanied with the following information:
-
Name of the owner
-
Address of the owner
-
Telephone number of the owners
-
Email address of the owner
-
Comco Ikarus serial number
-
Total flying hours
-
Number of landings
-
Description of the problem
-
Digital photos if requested
In order to be eligible to receive warranty service, you must present your
receipt of purchase or a comparable substitute proof of purchase bearing
the date of purchase.
You must ensure that all repair or customer service is handled at all times
by the authorized ISC or ITB in accordance with Comco Ikarus service
requirements.
In some cases, you may be requested to provide additional information
concerning the maintenance of the aircraft by the authorized IFC, ISC or ITB
only, therefore it is important to keep a record of any previous repairs, and
make them available if questions arise concerning maintenance.