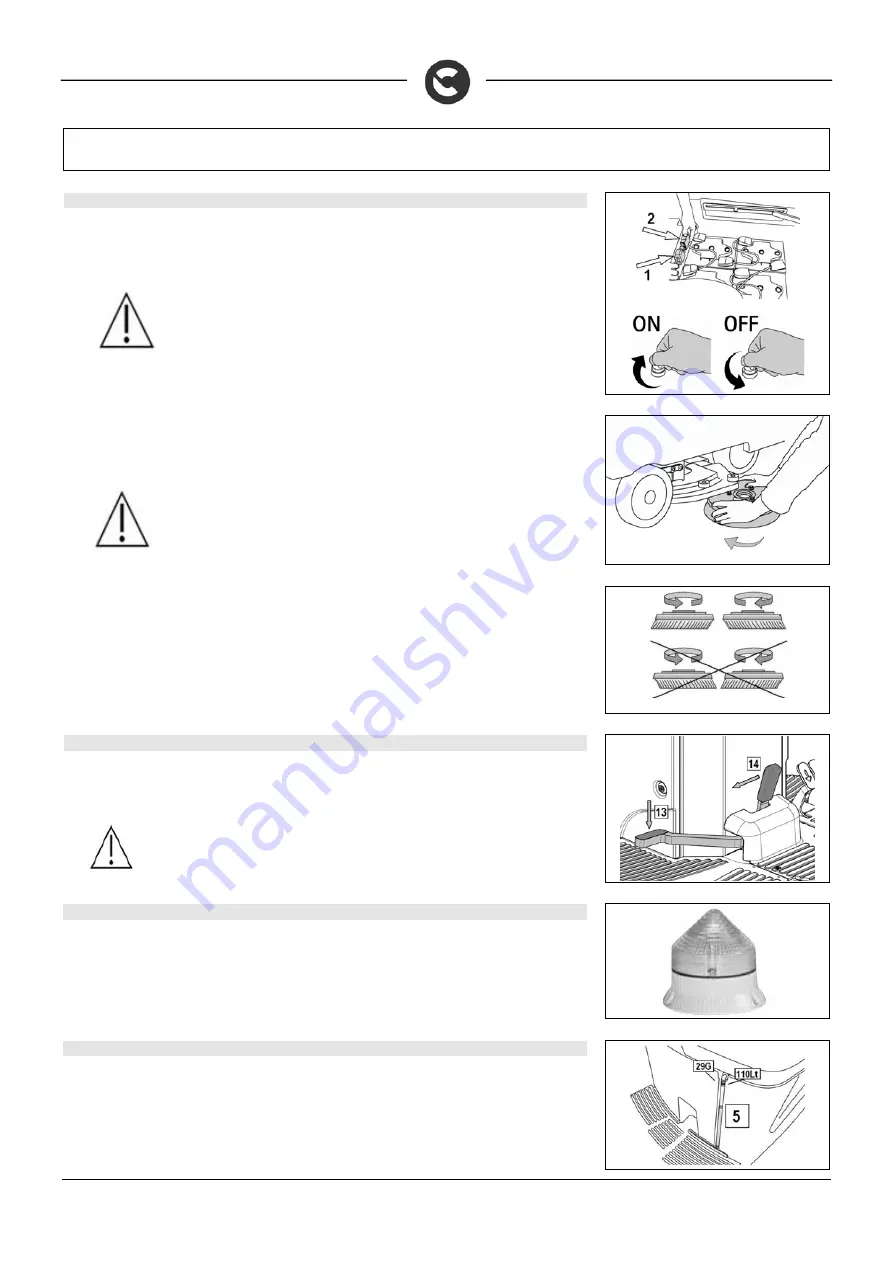
19
MACHINE PREPARATION
28.
DISC BRUSH ASSEMBLY
1.
Make sure the parking brake is engaged and that the main switch is OFF
2.
Connect the battery connector
3.
Turn the key to the "ON/I" position. The base raises automatically.
4.
Turn the key to the “OFF/0” position and remove it from the electrical board.
WARNING: during this operation, verify that there are no people or objects near
the brush.
5.
With the base up, insert the brushes in the plate housing beneath the base, turning them until
the three pins enter the niches in the plate itself; turn until the pin is pushed towards the coupling
spring and is locked into place. The photo shows the rotation direction to hook up the right-hand
brush; for the left-hand one, rotate in the opposite direction.
ATTENTION: You are advised to always wear protective gloves, to avoid the risk
of serious injury to your hands.
You are advised to invert the right and left-hand brushes every day. If the brushes are not new however,
and have deformed bristles, it is better to reassemble them in the same position (the right-hand one on
the right, and the left-hand one on the left), to prevent the different inclination of the bristles producing an
overload on the brush motor as well as excessive vibrations.
29.
SERVICE BRAKE AND PARKING BRAKE
The machine has an electronic braking system. To brake, in normal conditions, just remove your foot from
the accelerator pedal. If this service brake is working badly, or if necessary, activate the brake pedal (13)
pushing it downwards. To engage the parking brake, press the brake pedal (13) and lock it by pulling the
lever (14) to the left. The red indicator light on the instrument panel will switch on.
WARNING: to avoid any damage to the machine, always disengage the parking brake
before beginning to work or before making any transfer manoeuvres
30.
BLINKING LIGHT (OPTIONAL)
The machine can be equipped with a blinking light that turns on automatically when the key in the main
switch is turned on.
31.
EMPTY SOLUTION TANK DEVICE
To check the quantity of water in the solution tank there is a special level indicator tube (5) next to the
driver's seat.