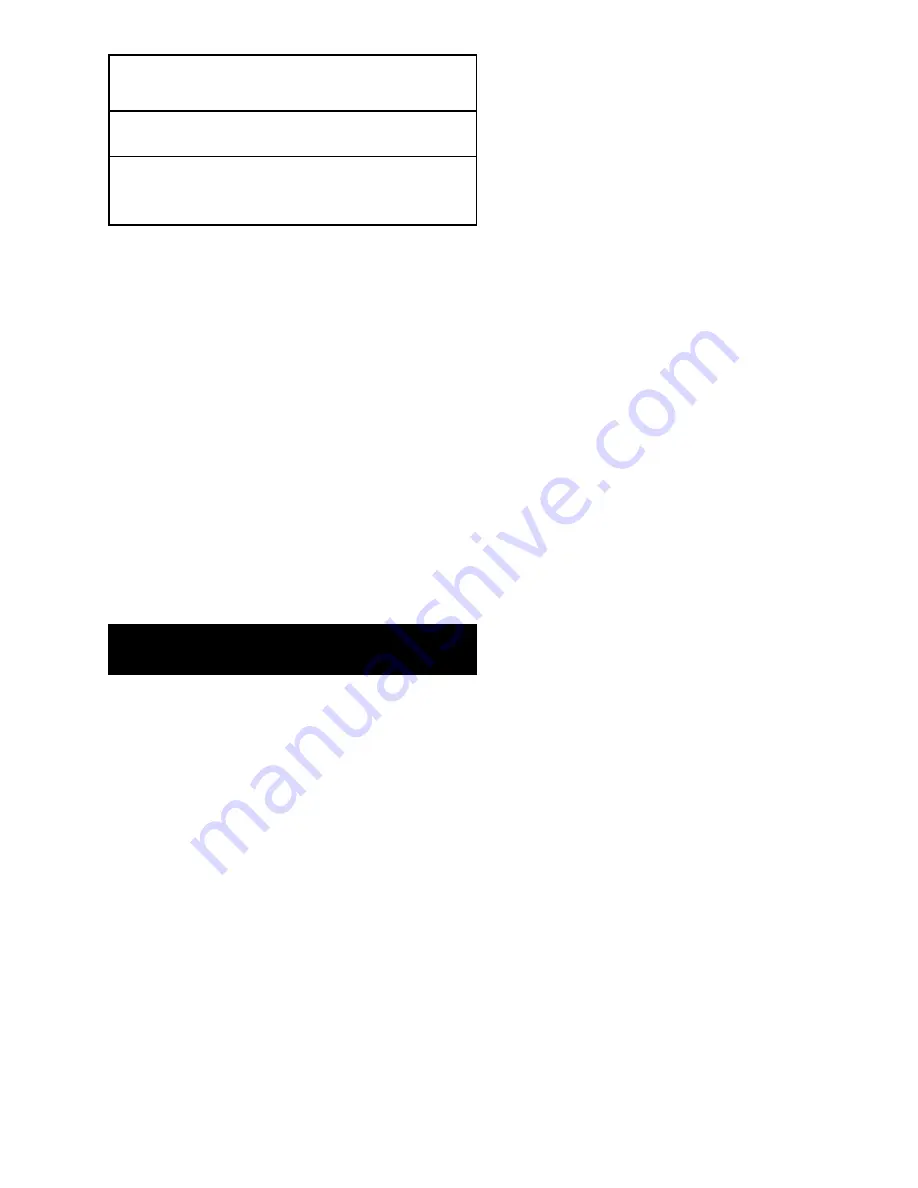
9. On single reeved chain hoist used in conjuction with head
blocks and ground support systems. Check for twists
between the hoist and head block. Twisted load can result
in a jammed liftwheel.
10.Do not allow the load to bear against the hook latch. The
latch is to help maintain the hook in position while the
chain is slack before taking up slack chain.
11. Take up a slack load chain carefully and start load easily to
avoid shock and jerking of hoist load chain. If there is any
evidence of overloading, immediately lower the load and
remove the excess load.
12.Do not allow the load to swing or twist while hoisting.
13.Never operate the hoist when flammable materials or
vapors are present. Electrical devices produce arcs or
sparks that can cause a fire or explosion.
14.
STAY ALERT!
Watch what you are doing and use
common sense. Do not use the hoist when you are tired,
distracted or under the influence of drugs, alcohol or
medication causing diminished control.
To maintain continuous and satisfactory operation, a regular
inspection procedure must be initiated to replace worn or
damaged parts before they become unsafe. Inspection inter-
vals must be determined by the individual application and are
based on the type of service to which the hoist will be subject-
ed and the degree of exposure to wear, deterioration or mal-
function of the critical components.
The type of service to which the hoist is subjected can be clas-
sified as “Normal”, Heavy”, or “Severe”.
Normal Service:
Involves operation with randomly distributed
loads within the rated load limit, or uniform loads less than 65
percent of rated load for not more than 25 percent of the time.
Heavy Service:
Involves operating the hoist within the rated
load limit which exceeds normal service.
Severe Service:
Normal or heavy service with abnormal
operating conditions.
Two classes of inspection - frequent and periodic - must be
performed.
Frequent Inspections:
These inspections are visual exami-
nations by the operator or other designated personnel.
Records of such inspections are not required. The frequent
inspections are to be performed monthly for normal service,
weekly to monthly for heavy service, and daily to weekly for
severe service, and they should include those items listed in
Table 4.
Periodic Inspections:
These inspections are visual inspections
of external conditions by an appointed person. Records of
periodic inspections are to be kept for continuing evaluation of
the condition of the hoist.
Periodic inspections are to be performed yearly for normal
service, semi-annually for heavy service and quarterly for
severe service, and they are to include those items listed in
Table 5.
CAUTION: Any deficiencies are to be corrected before
the hoist is returned to service. Also, the external condi-
tions may show the need for disassembly to permit a
more detailed inspection, which, in turn, may require the
use of nondestructive type testing.
PREVENTIVE MAINTENANCE
In addition to the above inspection procedure, a preventive
maintenance program should be established to prolong the
useful life of the hoist and maintain its reliability and continued
safe use. The program should include the periodic and fre-
quent inspections with particular attention being paid to the lubri-
cation of the various components using the recommended
lubricants (see page 11).
HOOK INSPECTION
Hooks damaged from chemicals, deformations or cracks, or
that have more than a 10
o
twist from the hook’s unbent plane,
excessive opening or seat wear must be replaced. Also, hooks
that are opened and allow the latch to not engage the tip must
be replaced. Any hook that is twisted or has excessive throat
opening indicates abuse or overloading of the unit. Inspect
other load sustaining parts, hook block screws, load pins and
hook block bodies for damage.
On latch type hooks, check to make sure that the latch is not
damaged or bent and that it operates properly with sufficient
spring pressure to keep the latch tightly against the tip of the
hook and allow the latch to spring back to the tip when
released. If the latch does not operate properly, it should be
replaced. See Figure 14 to determine when the hook must be
replaced.
W
WA
AR
RN
NIIN
NG
G
Allowing the load to bear against the hook latch and/or hook
tip can result in loss of load.
T
TO
O A
AV
VO
OIID
D IIN
NJ
JU
UR
RY
Y::
Do not allow the load and/or attachments to bear against
the hook latch and/or hook tip. Apply load to hook bowl or
saddle only.
V
!!
INSPECTION
8
Summary of Contents for LODESTAR B
Page 36: ...Entertainment Direct Control Lodestar Models J L LL R RR Protector Kit 32...
Page 38: ...34 Models J L LL R RR Motor End...
Page 46: ...44 NOTES...
Page 47: ...45 NOTES...
Page 48: ...46 NOTES...