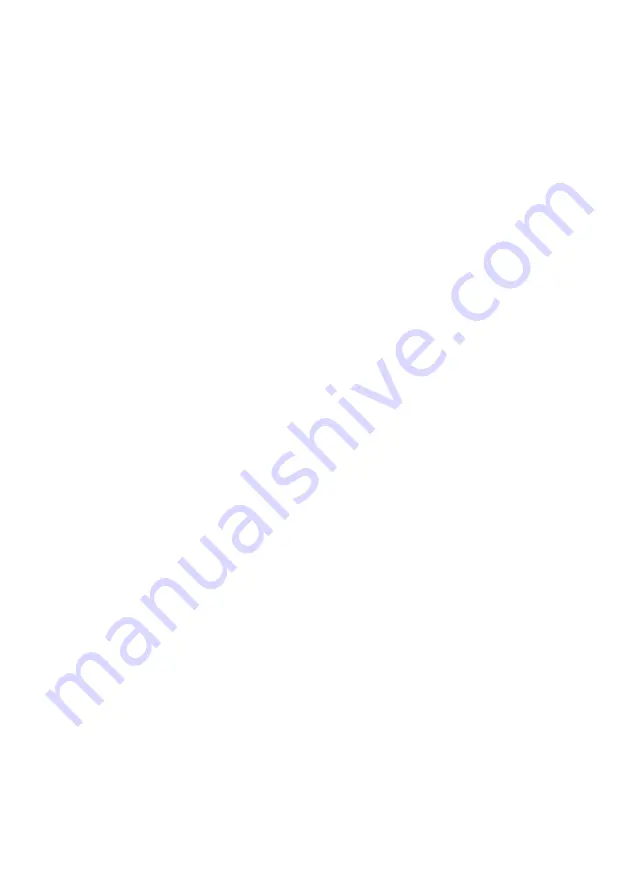
1.1 INTRODUCTION
1.1. This product is designed to meet the demands of today’s modern laboratory and has
been meticulously designed to provide years of service when used as described in the
following pages. This product is a 6-positioned heat and stir reaction station designed
for use with 56mm diameter glass vessels. Smaller diameter vessels can also be
accommodated using optional reducer sleeves (see Spares and Accessories section 10).
1.2. At the heart of this product is an innovative, firmware package designed to provide
enhanced, accurate temperature control of block or vessel content.
Temperatures are sensed either by a high precision platinum sensor embedded within
the vessel block, or via the optional external probe supplied separately. A microprocessor
constantly monitors temperature change many times per second. The products
temperature range is from ambient to +250°C.
1.3. This product comes equipped with ‘Reverse Stir’ facility. A feature that allows the vessel
stirring to be stopped and restarted in the opposite direction.
1.4. This product can interface with a robotic workstation or similar application. Connection
is made via the RS232 or RS485 sockets. The unique ‘Auto Detection’ feature senses the
interface connection and adjusts the set up characteristics accordingly.
1.5. Linked DC motors provide optimum speed control and sensitivity to drive the stir facility.
High performance magnetic sensors carefully measure speed control via a feed back
loop controlled by quartz oscillator and a microprocessor. The stir speed range is 400 –
2000rpm.
1.6. Optional PC based control software is supplied for advanced use with this product.
The RS-250D-250 can be connected via the RS232, 9 way D socket / Plug data cable
available as an accessory (see Spares and Accessories section 10). Stir / heat profiles can
be preset with any number of commands over varying time delays. This provides the end
user with infinite control over the application.
1.7. The vessel block is aluminium with a Teflon coating. The raised case walling reduces heat
loss, which improves energy efficiency and adds to the protection of the user.
3