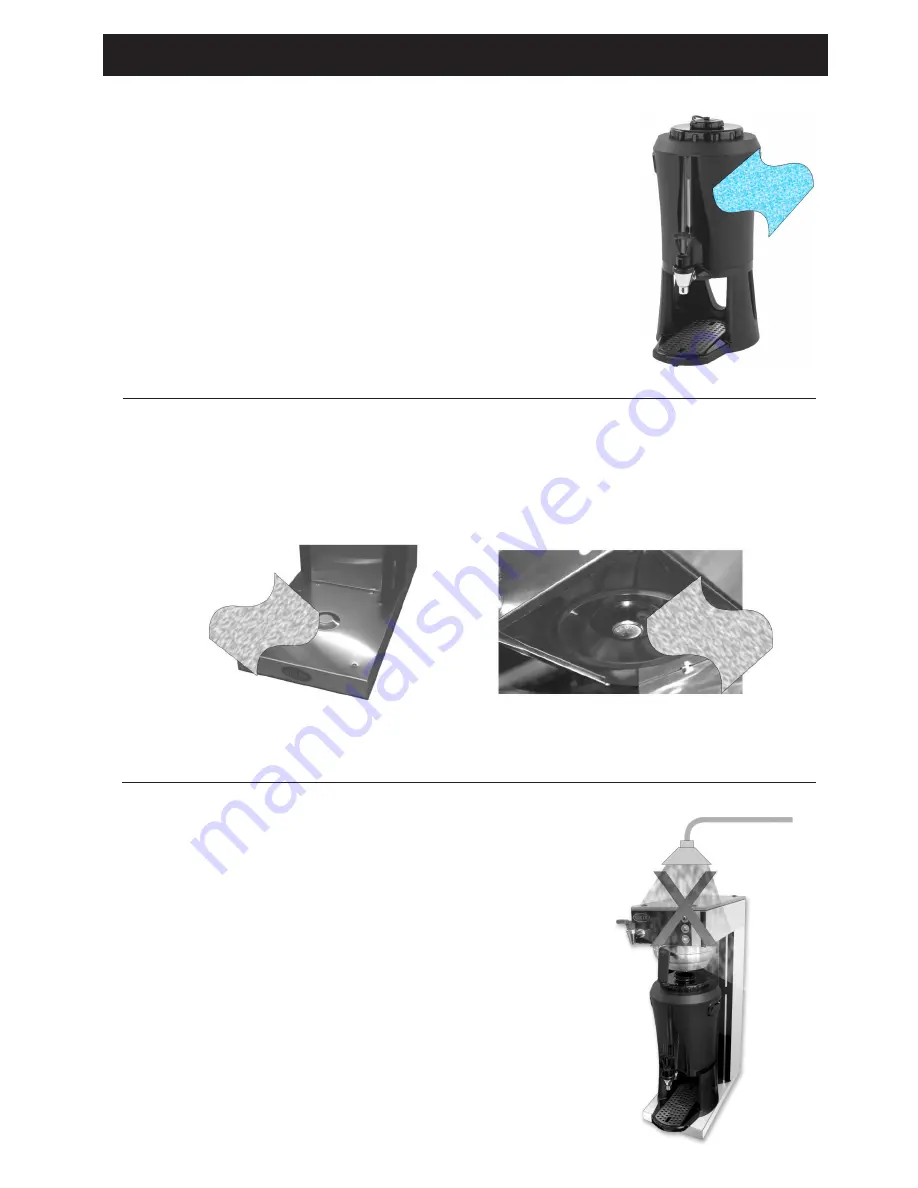
9. Maintenance and cleaning.
Cater Train
11
.
NOTE!
Before each brewing.
Rinse the serving station with fresh tap water.
Each day.
Rinse serving station and filtre holder with hot water.
Outside cleaning use a soft rag and liquid solution that
not prevent scratches.
CAUTION!
The machine should not be
submerged in water or been
washed in a dishwasher
Clean and dry this surfaces!
A
Each day.
Clean the bottom plate (A).
Clean the spray nozzle (B) and the surrounding area.
B
EACH DAY
When needed;
Clean the spray nozzles hole. If necessary loosen spray nozzle and clean/de-scaling
Summary of Contents for CATER
Page 1: ...Service manual Your Dealer COFFEE QUEEN CATER SINGLE Cater Train S EN Rev 100104 ...
Page 14: ...14 11 Dimension sketch Cater Train ...
Page 23: ...16 Exploded view Tank Cater Train 23 32 34 35 30 38 36 41 39 40 33 31 37 42 ...
Page 24: ...16 Exploded view Train components Cater Train 24 8 10 2 6 5 1 9 4 3 11 7 12 ...
Page 26: ...17 Electrical drawing 2x230VAC 1N 230VAC 1NCater train version 26 ...
Page 27: ...18 Mounting and dimension drawings Cater train version 27 Mounting and dimensions bottom ...