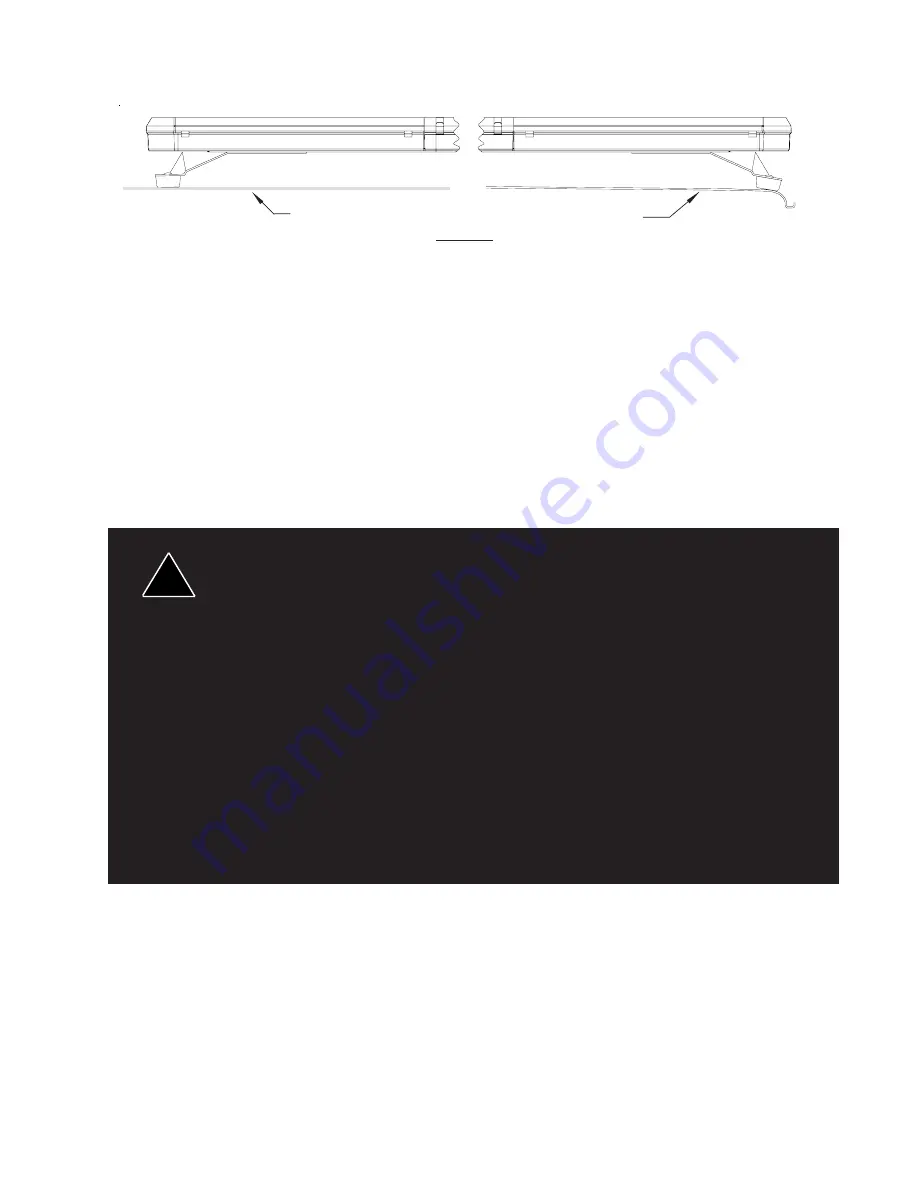
5
FIGURE 4
Once the light bar is level and centered, mark the holes through the mounting tabs and remove the
light bar from the vehicle. Make sure that the drill will not damage anything when penetrating the roof.
Drill the mounting holes and remove any burrs. Attachment can be made using 1/4" cap screws,
toggle bolts, or other fasteners as may be convenient. Use sealant as necessary to prevent water
leakage into the vehicle.
Wiring Instructions
Larger wires and tight connections will provide longer service life for components. For high current wires it
is highly recommended that terminal blocks or soldered connections be used with shrink tubing to protect
the connections. Do not use insulation displacement connectors (e.g. 3M
®
Scotchlock type connectors).
Route wiring using grommets and sealant when passing through compartment walls. Minimize the number
of splices to reduce voltage drop. High ambient temperatures (e.g. underhood) will significantly reduce the
current carrying capacity of wires, fuses, and circuit breakers. Use "SXL" type wire in engine compartment.
All wiring should conform to the minimum wire size and other recommendations of the manufacturer and be
protected from moving parts and hot surfaces. Looms, grommets, cable ties, and similar installation
hardware should be used to anchor and protect all wiring. Fuses or circuit breakers should be located as
close to the power takeoff points as possible and properly sized to protect the wiring and devices. Particular
attention should be paid to the location and method of making electrical connections and splices to protect
these points from corrosion and loss of conductivity. Ground terminations should only be made to
substantial chassis components, preferably directly to the vehicle battery. The user should install a fuse
sized to approximately 125% of the maximum Amp capacity in the supply line to protect against short
circuits. For example, a 30 Amp fuse should carry a maximum of 24 Amps. DO NOT USE 1/4" DIAMETER
GLASS FUSES AS THEY ARE NOT SUITABLE FOR CONTINUOUS DUTY IN SIZES ABOVE 15 AMPS.
Circuit breakers are very sensitive to high temperatures and will "false trip" when mounted in hot environ-
ments or operated close to their capacity.
WARNING!
!
Curved Roof
Flat Roof
Place Feet on
Curved Portion
Before attempting to connect wiring refer to wire tag attached to the lightbar's main cable. Each wire in the cable controls a
separate lightbar function as described in the wire tag.
The only significant difference between the LED X™ 2100 with optional ArrowStik
®
and a conventional LED X 2100, is the
additional, thinner cable exiting the bottom of the lightbar. The larger cable is the lightbar power cable. Route the wiring cable
into the engine or passenger compartment, taking care to use grommets and to apply sealant around openings to keep water
out. It is advisable to leave an extra loop of cable when installing the light bar to allow for future changes or reinstallations.
Connect the black lead to a solid frame ground (earth), preferably, the (-) or ground (earth) side of the battery and bring the
other wires to the control head or switches. Connect the wires as directed by the wiring instructions on the cable.