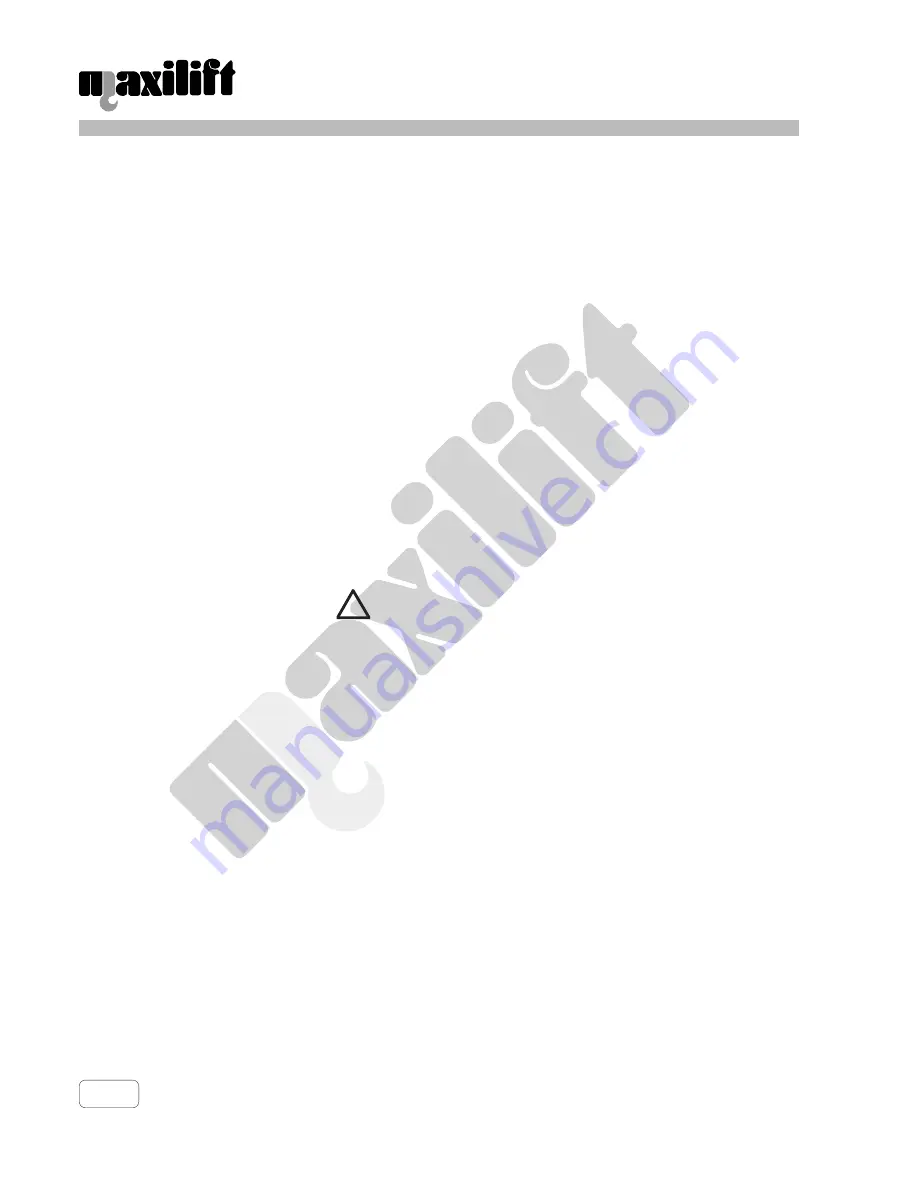
38
9.3.2 Monthly checking
• Check the setting of the pressures in the hydraulic system, and integrity of the seals.
• Check the absence of oil leaks.
• Check integrity and tightening of crane tie rods and bolts.
• Check integrity and tightening of hoses, piping and their fittings.
• Check fastenings and safety devices.
• Check readability of symbols on the remote control.
• Check integrity of hooks, ropes, chain and all the other lifting ancillary equipment.
• Check that all the identification and warning plates are still applied and readable.
• Visually check all the structural components for any deformation, backlash or crack out.
• Clean oil filters.
• Check the oil level and lubricate accordingly to the lubricating and greasing chart.
• Check the regular working of the slewing system, grease with the suggested grease the worm and
the worm gear, replace the grease brush spreader if worn.
• Make a working test of the crane, with and without the load, paying attention to possible unusual
noises coming from the crane parts.
• Grease the hydraulic boom sections.
9.3.3 Checking every six moths
• Wash and clean the crane
ATTENTION
Never wash the crane with chemical products or high pressure water jets, as they can cause the
detaching of the stickers and water entering inside the electrical components and the slewing
case.
• Check the pressure settings in the hydraulic system.
• Check the absence of oil leaks.
• Check integrity and tightening of crane tie rods and bolts.
• Check integrity and tightening of hoses, piping and their fittings.
• Check fastenings and safety devices.
• Make a safety test of the hydraulic system.
• Check correct working of remote control and readability of relevant symbols.
• Check integrity of hooks, ropes, chain and all the other lifting ancillary equipment.
• Check that the all the identification and warning plates are still applied and readable.
• Visually check all the structural components to find any deformation, backlash or crack out.
• Check the oil level and lubricate accordingly to the lubricating and greasing chart.
• Replace the filter of the hydraulic oil.
• Make a working test of the crane, with and without the load, take care of listening to strange noises
coming from the crane parts.
9.3.4 Others
• Stability of unit throughout working area. Check stability procedure annualy or when any change is made to
crane or truck.