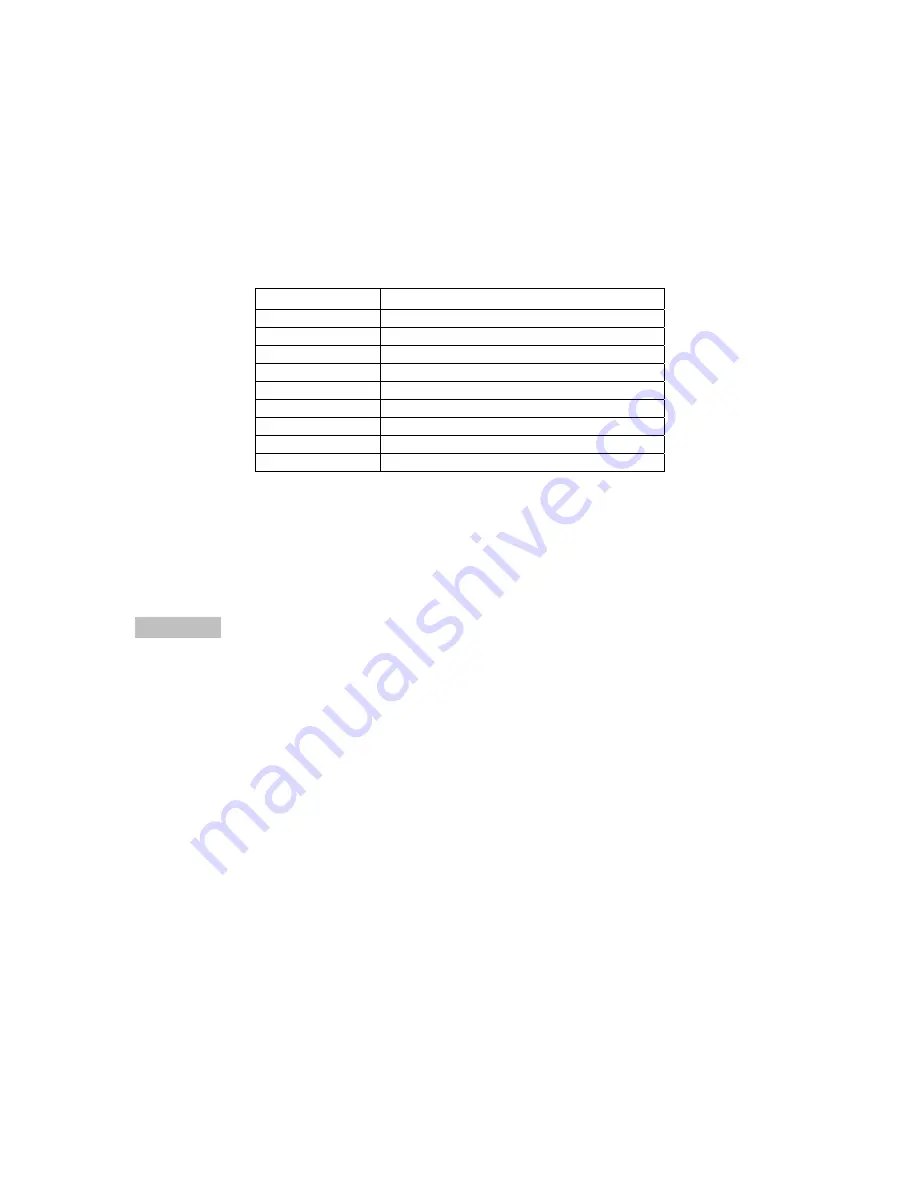
58
Clutch adjustment washers
Your Cobra comes stock with flat washer(s) at the bottom of the spring washer
stack. Cobra offers several thicknesses of thin adjustment washers that allow
clutch engagement tuning. Increasing the flat washer(s) thickness increases the
engine speed for clutch engagement thus increasing the abruptness of clutch
engagement (harder hit). Conversely, decreasing the flat washer(s) thickness
decreases the engine speed for clutch engagement thus decreasing the
abruptness of clutch engagement (softer hit).
Part #
Thickness mm (inch)
HKCSM015 1.5
(0.060)
HKCSM012 1.2
(0.047)
HKCSM008 0.8
(0.031)
HKCSM006 0.6
(0.025)
HKCSM005 0.5
(0.020)
HKCSM004 0.4
(0.015)
HKCSM003 0.25
(0.010)
HKCSM001 0.12
(0.005)
HKAM0022
CLUCTH SHIM KIT
NOTE:
HKAM022 Clutch shim kit includes - 3 each .005”, .010”, .015” and .020”
shims along with 2 clutch to hub spacers and 2 thin clutch to hub spacers.
Use the table above to order adjustment washers. Replace the stock washer with
the proper combination of adjustment washers that delivers the desired clutch hit.
CAUTION:
It is easy to prematurely damage the clutch and other engine components with
improper clutch adjustment. If you are unsure of how to adjust the clutch, contact
the Cobra Technical Support Group before making adjustments.
Clutch shoe wear:
This can be measured by the overall diameter of the shoes installed on the
arbor. This measurement should be greater than 80.5mm
If the clutch has been slipping and shows signs of glazing, it is best to replace
the shoes. We have found that once the shoes are glazed, even if deglazed
with emery paper or a file, the performance is reduced.
The best way to prevent glazing is by not gearing too high, changing the oil as
specified and by not blipping the throttle.
Every time you blip the throttle, you
are working your clutch springs.
Clutch basket wear:
The internal diameter of a new clutch basket should measure ˜84.10mm.
Over time the clutch shoes will wear the internal surface down creating a
bigger ID and causing a later engagement. The maximum ID we recommend
to allow is 84.25mm.
Summary of Contents for CX50 SR
Page 24: ...24 Parts Engine Bottom End and Transmission...
Page 26: ...26 Parts Engine Clutch and Kick Lever...
Page 31: ...31 This Page Intentionally Left Blank...
Page 32: ...32 Parts Forks Triple Clamps...
Page 34: ...34 Parts Forks Leg Assembly Brake Side...