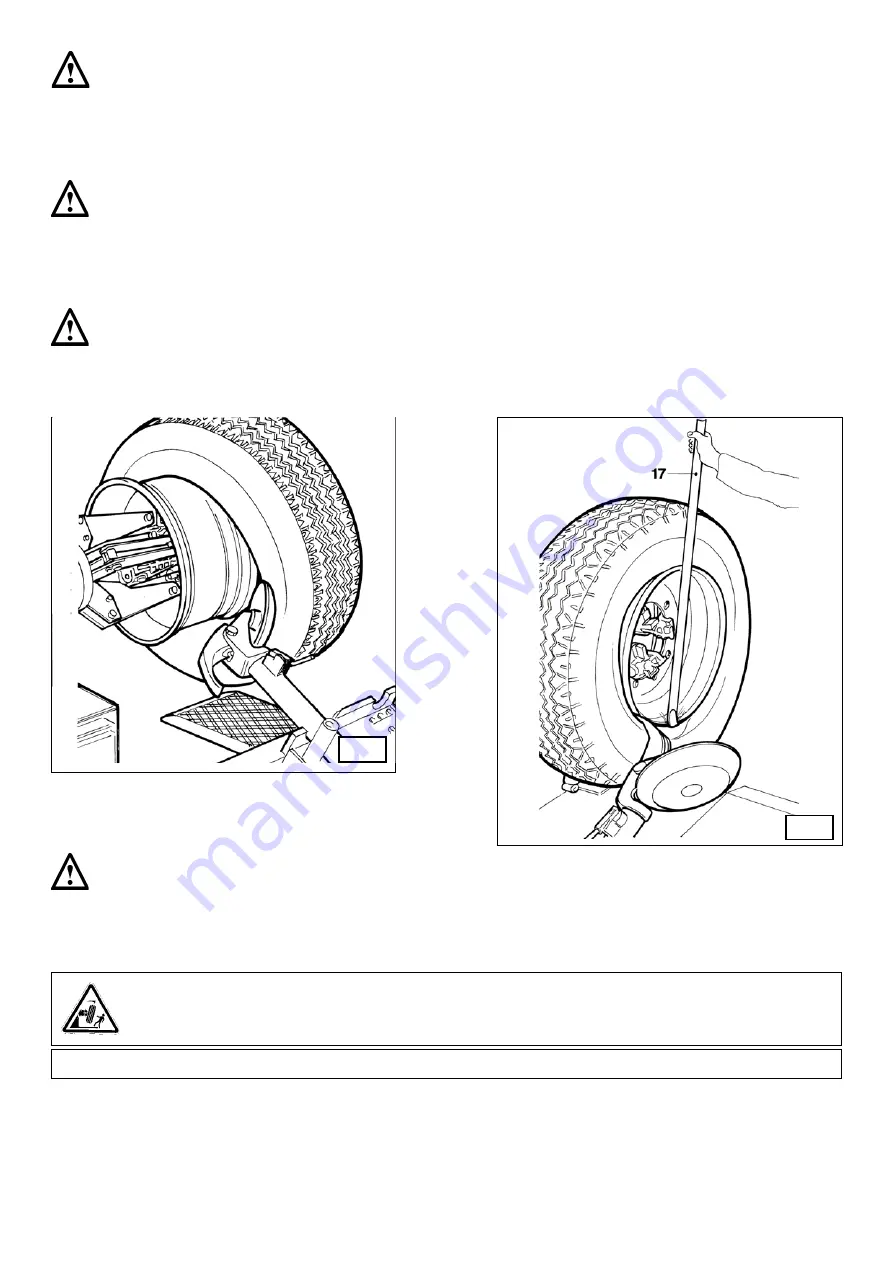
1
- Insert lever
(17, Fig. I) between rim and bead at the right of the tool.
-Press down on the lever and lower the wheel to bring the edge of the rim about 2 inch (5 cm) from the hooked tool.
-Turn the wheel anticlockwise pressing down on lever
until the bead is completely off.
-Move the tool carrier arm to its non-working position and then move it to the inside plane of the wheel.
- Rotate the wheel and at the same time move the hook tool forward inserting it between rim and bead until it is anchored to the bead
(See Fig. I).
-Move the rim 1,5 - 2 inch (4-5 cm) from the tool taking care that it does not unhook from the bead.
-Move the hook tool towards the outside until the red reference dot is by the outside edge of the rim.
-Place the tool carriere arm in its working position, then use the bead disc to push against the inside face of the tire (see fig. H) it is best
to do this with the wheel turning.
-Move the rim about 4-5 cm from the tool making sure the hook does not detach from the rim.
Take the mobile control unit to work position C.
Take the mobile control unit to position B.
Take the mobile control unit to work position D.
H
I
-Always keep the rotating counterclockwise, while pushing with the bead disk
Turn the wheel counterclockwise pushing with disk until the tire comes completely off the rim.
DANGER!
When the beads come off the rim, the tire will fall. Check to make sure there are no by-standers in the work
area.
MOUNTING
Tubeless tires can be mounted using either the
bead breaker disk
or the
hook tool
.
If the tire is not problematic, use the bead loosener disk.
If the tire is very rigid, the hook tool must be used.
Take the mobile control unit to work position B.
Summary of Contents for CHD-9043
Page 27: ...27...